In the realm of CNC machining, surface finishing quality is a crucial factor that can make or break the effectiveness of a part. Whether it’s a critical component in the aerospace industry or a surgical instrument in the medical field, the surface quality of a CNC machined part refers to the overall finish, texture, and appearance of the part’s surface after being subjected to various machining processes.
Benefits and Advantages
The benefits of achieving a high-quality surface finish in CNC machining parts are manifold. Firstly, a smooth surface finish can reduce the coefficient of friction, which in turn can enhance the part’s functionality and performance. This can be especially crucial in high-stress applications where any reduction in friction can lead to significant improvements in efficiency and durability. Secondly, a polished surface can improve the part’s aesthetic appeal and provide a better overall user experience. This can be important for products that are intended for consumer use or in applications where presentation is important. Thirdly, a high-quality surface finish can also reduce the risk of corrosion, wear and tear, and other types of damage that can affect the part’s longevity and durability. This can be especially important in applications where the part is exposed to harsh environments or repeated use.

Types of Machining Processes
precision CNC machining parts can be created using a wide variety of processes, each of which can have a different impact on the surface quality of the final product. Some of the most common machining processes used to create high-quality surface finishes include turning, milling, grinding, and polishing. Each of these processes has its own unique advantages and disadvantages, and the choice of process will depend on the specific requirements of the part and the desired surface finish.
Turning, for example, is a process that is often used to create cylindrical or conical shapes. It involves rotating the part while a cutting tool removes material from the surface, resulting in a smooth and even finish. Milling, on the other hand, is a more versatile process that can be used to create a wide variety of shapes and features. It involves moving a cutting tool across the surface of the part in a series of carefully controlled movements. Grinding is another process that can be used to achieve a high-quality surface finish. It involves using an abrasive wheel to remove material from the surface of the part, resulting in a smooth and uniform finish. Finally, polishing is a process that is used to create a mirror-like finish on the surface of the part. It involves using a series of polishing pads and abrasive compounds to bring the surface of the part to a high shine.
Application Areas
The surface quality of CNC machined parts is essential across a wide range of industries and applications. In the aerospace industry, for example, the surface quality of critical components such as turbine blades and engine parts is crucial for ensuring optimal performance and safety. Any defects or imperfections in the surface of these parts can lead to catastrophic failure, so achieving a high-quality surface finish is essential. In the medical industry, the surface quality of surgical instruments and implants is essential for reducing the risk of infection and improving patient outcomes. A smooth and uniform surface finish can help to prevent the buildup of bacteria and other pathogens, reducing the risk of infection and improving the overall safety of medical procedures.
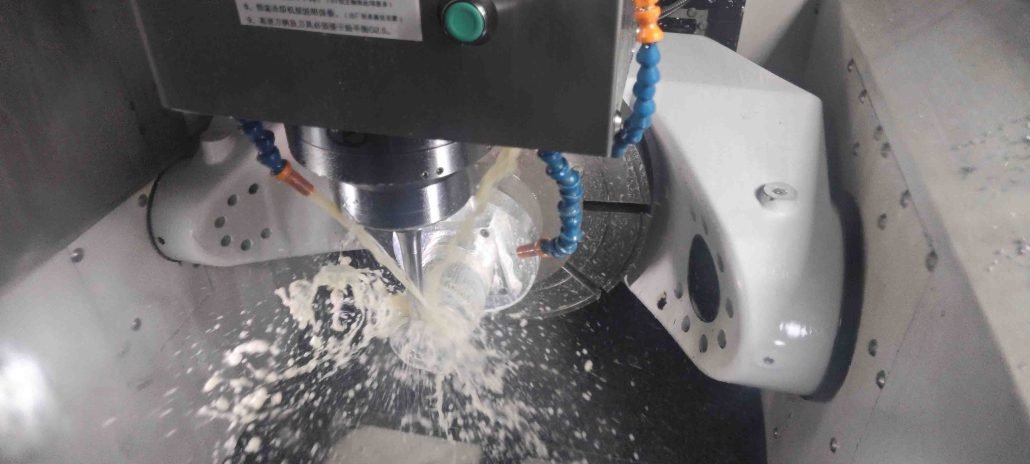
Precision and Quality
In addition to the benefits and application areas, it is worth noting that surface quality is also an essential factor in determining the overall precision and quality of CNC machined parts. A high-quality surface finish indicates that the part has been manufactured with the utmost precision and care, using advanced equipment and techniques. This can be especially important in industries where the safety and reliability of the product are paramount, such as aerospace, medical, and automotive industries. Achieving a high-quality surface finish is a sign of quality and attention to detail, and it can help to build trust and confidence in the final product.
In conclusion, achieving high-quality surface finishes in CNC machining parts is a critical factor in enhancing functionality, improving the aesthetic appeal, and ensuring the longevity and durability of the final product. Understanding the importance of surface quality and selecting the appropriate machining processes can help manufacturers create parts that meet the highest standards of precision and quality. With the right processes and techniques, it is possible to achieve surface finishes that are not only functional but also visually appealing and reliable, making CNC machined parts a crucial component in a wide range of industries and applications.