With the progress of modern science and technology, the manufacturing industry is developing. Extrusion molding technology is used to make a wide range of products, from automotive parts to building materials to aerospace and defense technology.
If you’re interested in learning more about extrusion moulding and its benefits, you’ve come to the right place. In this article, we’ll provide an in-depth overview of this manufacturing process, including its history, key components, advantages, and limitations. By the end of this article, you’ll have a better understanding of extrusion moulding and how it can be used to create high-quality products with ease.

A Brief History of Extrusion Moulding
The extrusion process has been around for centuries, dating back to the early Egyptian and Mesopotamian civilizations. However, it was not until the mid-1800s that the first extrusion machines were invented, which were primarily used for the production of lead and other metals.
It wasn’t until the 1930s that extrusion moulding became widely used in the plastics industry. With the development of new materials such as polyvinyl chloride (PVC) and polyethylene (PE), extrusion became a popular and cost-effective method for producing plastic products in mass quantities.
Today, extrusion moulding is used in nearly every industry that requires the production of plastic products.
What is Extrusion Moulding
Extrusion moulding is a manufacturing process that involves heating, melting, and forming plastic materials into a continuous profile shape. The process can also involve other materials such as metals and ceramics. Extrusion moulding is carried out using an extrusion machine, which consists of a barrel, a screw, a die, and a motor.
The process begins by feeding raw materials into the barrel, where they are heated and melted using the heat generated by the motor. The melted materials are then forced through the screw, which rotates in the barrel, and into a die. The die is designed to give the material its desired shape and size. The material is then cooled and cut to the right length.
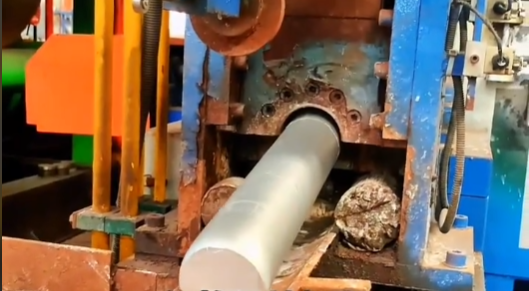
Types of Extrusion Moulding
Extrusion moulding comes in various types, depending on the product being manufactured. Some common extrusion processes include:
- Blown film extrusion: This process produces thin films of plastic material that are used in packaging applications.
- Tubing extrusion: This process produces tubes of different sizes that are used for various applications such as medical tubing, garden hose pipes, and irrigation systems.
- Sheet extrusion: This process produces plastic sheets of varying thickness used in signs, industrial packaging, and automotive applications.
- Coextrusion: This process combines two or more different materials into a single extruded product. The result is a product with improved mechanical, physical, and barrier properties.
Key Components of Extrusion Moulding
Extrusion moulding is a relatively simple process that consists of several key components:
- Extruder – This is the machine that feeds the raw material into the process and melts it down into a molten state.
- Die or nozzle – This component shapes the molten material into the desired shape or form.
- Cooling system – Once the material has been formed, a cooling system helps to solidify it into its final shape.
- Take-up system – This is used to pull the extruded material through the process and ensure it maintains its shape.
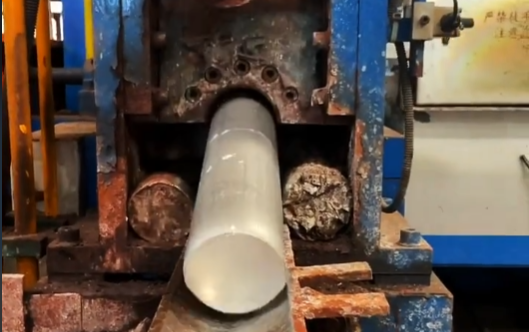
Advantages of Extrusion Moulding
There are several advantages to using extrusion moulding for the production of plastic products, including:
- Cost-effective – Extrusion moulding is a highly efficient process that can produce large quantities of products quickly and at a low cost.
- Versatile – This process can be used to create a wide range of shapes and forms, making it a popular choice for a variety of industries.
- Consistent quality – Since the process is highly automated, it is easy to maintain a consistent level of quality throughout the production process.
- Green production methodology given that it provides minimal wastage through recycling and reuse of scrap materials.
Limitations of Extrusion Moulding
While extrusion moulding is a popular and versatile process, it does have some limitations, including:
- Design limitations – Since the process involves forcing molten material through a die or nozzle, there are limitations to the complexity of shapes that can be produced.
- Material limitations – Extrusion moulding is primarily used for the production of plastic products, meaning it may not be suitable for other materials or applications.
- Heavy upfront investment – Setting up an extrusion moulding line requires a significant upfront investment in machinery and equipment making it difficult for small-scale entrepreneurs to invest in it.
Extrusion moulding is a highly efficient and cost-effective method used for creating plastic products. This process offers a range of benefits, including versatility, scalability and consistent quality. Understanding the different components of the process, as well as its advantages and limitations, can help you make informed decisions about how to use extrusion moulding in your manufacturing, and contribute positively to sustainability.
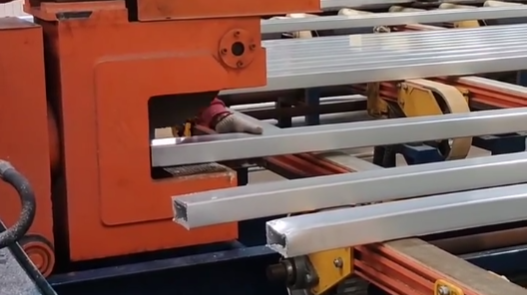
How Extrusion Moulding can Benefit Your Manufacturing Process
If you are in the manufacturing industry, you can benefit from using extrusion moulding in the following ways.
Firstly, extrusion moulding can help you reduce your production costs. The process is efficient, and it can produce large quantities of plastic products in a short time. This can help you meet your production targets and improve your bottom line.
Secondly, extrusion moulding can help you produce high-quality plastic products. The process is precise, and it can create products with accurate dimensions and shapes. This can help you meet your clients’ specifications and improve your reputation in the industry.
Finally, extrusion moulding can help you reduce your environmental footprint. The process uses recycled materials, which can help you reduce your carbon emissions and contribute to a sustainable future.
Compared with traditional metalworking methods, extrusion molding can easily produce a part with fine lines and smooth curves using a set of steel dies. In addition, due to the high precision of extrusion molding, the manufactured parts can fully meet the requirements of any product. This has led to a wide range of applications in the automotive, aerospace and construction industries where product quality is highly required.