Injection molding is a popular manufacturing process used to create complex parts for a variety of industries. From automotive to medical and aerospace, injection molding has become an indispensable tool for producing high-quality parts in large quantities. However, one common problem that manufacturers face during plastic injection molding is weld lines. In this informative article, we will be discussing how to avoid weld lines in injection molding.

What are Weld Lines?
Weld lines are an aesthetic defect that appears on the surface of molded parts. They occur when the material converges after being split at an intersection point. They can also occur when a mixture of two or more streams of molten material meets before filling the mold completely. Weld lines can weaken the structural integrity of the parts, making them more susceptible to damage, and can also cause a reduction in their appearance and functionality.
How to Avoid Weld Lines in Injection Molding?
1.Adjust Injection Speed:
One of the common causes of weld lines is the high injection speed of the molding machine. A high injection speed can cause the material to split, resulting in unwanted weld lines. To avoid this problem, the injection speed should be adjusted during the molding process to reduce the risk of split material. By slowing down the injection speed, the melt front can move smoothly to fill the mold cavity with uniformity.
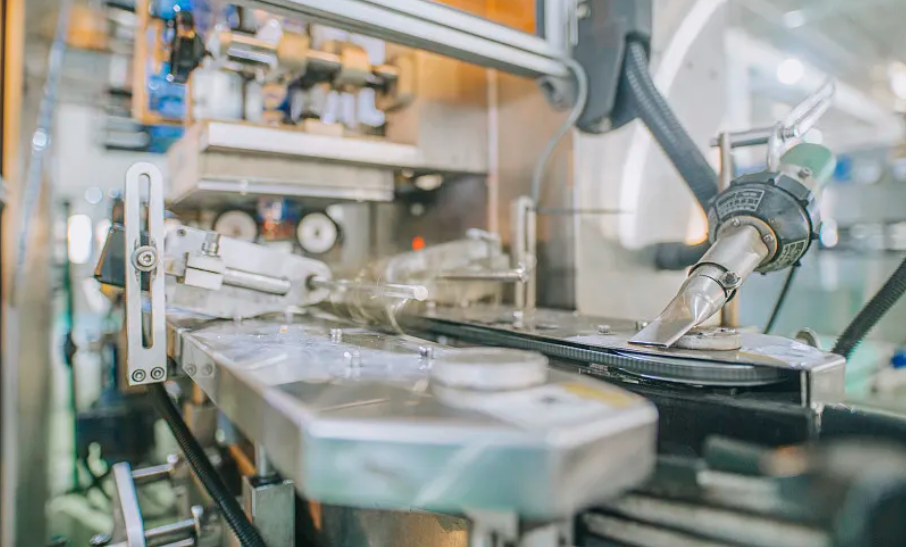
2.Optimize Gate Design:
The gate design plays a vital role in the injection molding process. The gate is the point where the molten material enters the mold. A gate that is too small can cause the material to split, leading to unwanted weld lines. On the other hand, a gate that is too large can lead to over packing, resulting in sink marks. Therefore, it is essential to optimize the gate design based on the material and part geometry to avoid weld lines.
3.Select Appropriate Material:
The type of material used in injection molding can also affect the occurrence of weld lines. Certain materials are more prone to weld lines than others. It is crucial to select a material that is appropriate for the part design to reduce the risk of weld lines. A material with low melt viscosity can help minimize the occurrence of weld lines, as it can flow easily without splitting.
4.Proper Mold Design:
The mold design also plays a critical role in the occurrence of weld lines. The use of complex mold designs can lead to the formation of weld lines. Therefore, it is essential to design molds that are simple and have smooth surfaces. It is also crucial to ensure that the mold is maintained adequately and cleaned regularly to avoid any contamination that can cause unwanted weld lines.
Weld lines are a common problem in injection molding, but they can be avoided by following specific guidelines. The four tips mentioned above are just a few of the many ways to avoid weld lines in injection molding. By optimizing the gate design, selecting appropriate material, adjusting injection speed, and proper mold design, manufacturers can reduce the risk of weld lines and produce high-quality parts that meet their customer’s needs.