As the demand for precision and high-quality products continues to grow, plastic injection molding manufacturers face an increasing challenge of meeting the tight tolerance requirements imposed by their customers. Tolerances, in the context of injection molding, refers to the range or limit of acceptable deviation from the intended or specified dimension of a finished product. Inaccurate tolerances can end up affecting the functionality of a product, compromising its quality and performance, and hurt the bottom line of both the manufacturers and customers.
At Longsheng, we understand how important it is to meet tolerance standards for our clients’ plastic parts.To avoid these misfortunes, injection molding manufacturers must fully comprehend the basic principles of tolerances and the various factors that can impact it within the manufacturing process. This article will provide a comprehensive guide to plastic injection molding tolerance standards, discussing everything from the definition of tolerance to the consequences of not meeting these standards.

What are Plastic Injection Molding Tolerance Standards?
Tolerances are an essential aspect of any injection molding operation, and they allow for precise and repeatable manufacturing processes. Tolerance standards, on the other hand, are guidelines or specifications set by manufacturers that outline the allowable variation from the intended or specified dimension of a finished part or product. These standards dictate how much variation is permitted in different dimensions, how they can impact the intended functionality, and how manufacturers can reduce or control these deviations.
Types of Tolerance
Before delving into the different standards, let’s first define the types of tolerances used in plastic injection molding.
Dimensional Tolerance
This type of tolerance refers to the deviation of dimensions from the intended specifications. Dimensional tolerance is denoted in units, such as millimeters or inches.
Geometric Tolerance
This type of tolerance refers to the allowable deviation of geometric features, such as angles, shapes, and profiles. Geometric tolerances are often expressed as a tolerance zone within which the feature must fall.
Material Property Tolerance
This type of tolerance refers to the allowable deviation of the material properties, such as strength, flexibility, or color.
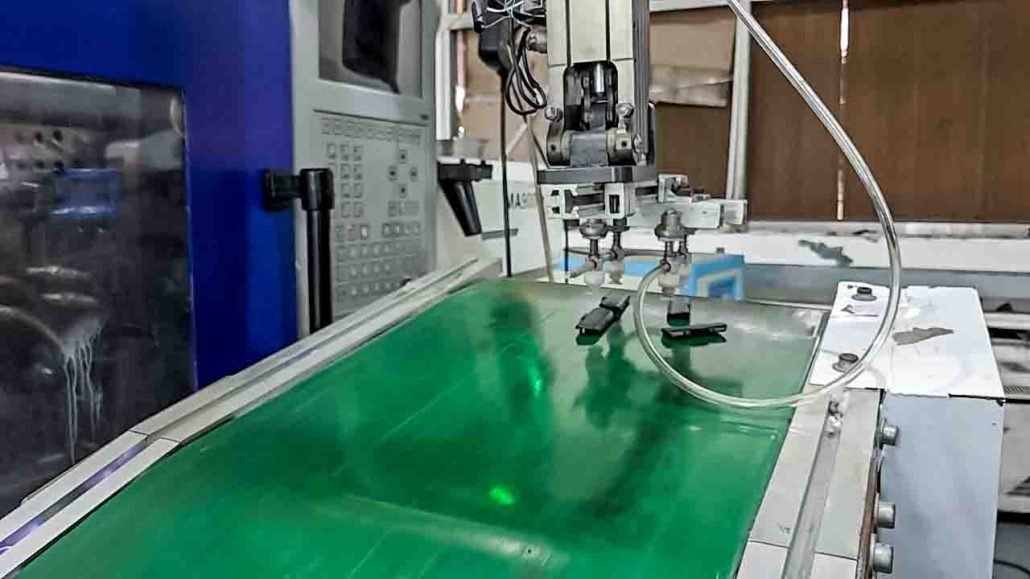
Standards for Plastic Injection Molding Tolerances
There are several industry standards established for plastic injection molding tolerance. Below are some of the commonly used standards:
ISO 20457
This standard covers the general tolerances for plastic injection-molded parts. It includes size tolerances, form and position tolerances, and surface quality requirements.
ASTM D6913
This standard specifies the dimensional tolerance requirements for plastic injection-molded parts. It also provides guidelines for measuring and inspecting the parts.
MIL-STD-130
This standard provides requirements for marking and identifying plastic injection-molded parts. It also includes tolerance requirements for marking and labeling.
Functional Tolerance Standards
Dimensional Tolerance
This is the most common form of tolerance and refers to the acceptable range of variation in a part’s size, shape, and other measurements.
Geometric Tolerance
This type of tolerance refers to the acceptable range of variation in the shape, orientation, or location of features or patterns on the part.
Surface Finish Tolerance
This refers to the acceptable range of variation in the texture, smoothness, or roughness of the surface of the part.
Cosmetic Tolerance Standards
Color Tolerance: This refers to the acceptable range of variation in the color of the product.
Visual Tolerance: This refers to the acceptable range of variation in the part’s appearance, including surface blemishes, scratches, or other imperfections.
Why are Tolerance Standards Important in Injection Molding?
Injection molding tolerance standards are crucial for several reasons. First, they ensure that the final product meets the functional requirements of the customer by ensuring that every critical dimension is within the required specifications. Secondly, they aid manufacturers in designing parts with manufacturability in mind. Tolerance standards help to establish dimensions that are both practical and achievable while accounting for all the variables involved in the process.
Lack of compliance with tolerance standards can lead to several consequences such as functional challenges, product failure, and rejection of parts, all of which can impede productivity, impact customer satisfaction, and even lead to legal implications.

Achieving High-Quality Parts through Tolerance Standards
To achieve high-quality parts, manufacturers must have a robust and systematic approach to measuring and controlling tolerances. Failure to meet these essential standards can lead to significant difficulties and setbacks in production. The following are some essential guidelines to keep in mind when creating high-quality parts:
Collaborate with Clients
Manufacturers must work closely with clients to understand their product and design requirements. Based on these specifications, manufacturers can set the required tolerances for the parts to meet the client’s expectations.
Process Control
Having a reliable and repeatable manufacturing process is essential to maintaining tolerances consistently. Process control techniques such as Statistical Process Control (SPC) help manufacturers achieve tighter tolerances by measuring the variability and taking corrective action when deviations occur.
Use High-Quality Materials
The choice of materials plays a significant role in maintaining consistent tolerances. Manufacturers should select the best high-quality materials from reputable suppliers to ensure minimal variation in properties during the molding process.
Quality Control
Regular quality control checks ensure that parts remain within specified tolerances during and after production. Various inspection techniques such as Coordinate Measuring Machines (CMM) help determine if a part falls within acceptable limits.
Factors Affecting Injection Molding Tolerances
Understanding the factors that impact tolerances is vital for ensuring that manufactured parts meet the established standards. Some of the factors that influence injection molding tolerances include:
Material Variation
Raw materials play a critical role in determining the finished product’s tolerances and ensuring the required quality standard. Factors such as the type of plastic resins, fillers, and additives can impact the final product’s properties, including dimensional stability and strength.
Process Variation
Injection molding is a complex process with many variables that can affect the final product’s dimensional accuracy. These variables can include pressure, temperature, and speed, among others. Any slight change in these variables can have a significant impact on the final product’s dimensional accuracy. It is, therefore, essential to ensure that the production process is maintained at optimal levels and any variations carefully controlled.

Tooling Variation
Tooling variation is one of the most significant contributing factors to variation in tolerances. Tooling can be affected by factors such as tooling design, material variations, and the injection molding process. To ensure accuracy and consistency, tool designs should be optimized and verified regularly.
Controlling Tolerance Standards in Injection Molding
To maintain the required tolerances in injection molding, manufacturers can take several steps that include:
Design for Manufacturability
Designing for manufacturability means that the designer works in close collaboration with the injection molding manufacturer to ensure producibility, functionality, and manufacturability. This helps to establish design tolerances that are both practical and achievable while accounting for all the variables involved in the process.
Regularly Verify Tools
To ensure tooling variation is controlled, manufacturers should regularly verify the accuracy of the tooling used. This involves performing regular checks on the tools to confirm that they are correctly machined, dimensioned, and maintained.
Process Control
Maintaining accurate and consistent plastic injection molding process is crucial to achieving the required tolerances. By monitoring and controlling the variables associated with injection molding, manufacturers can minimize variations significantly.
Benefits of Working with a Professional Injection Molder
Working with a professional injection molder like Longsheng comes with several benefits, including:
Expertise in meeting tolerance standards: Our team has extensive experience and expertise in achieving precise and consistent dimensions for our clients’ plastic parts.
Advanced manufacturing capabilities: We use advanced manufacturing technologies and processes to ensure our clients’ parts meet the most stringent tolerance requirements.
Quality control measures: We have rigorous quality control measures in place to ensure that our clients’ parts meet the required tolerance standards.
Conclusion
In conclusion, tolerances play a vital role in ensuring the final product’s quality and functionality. Injection molding manufacturers must embrace and comply with plastic injection molding tolerance standards to remain competitive and meet their clients’ needs. Failure to comply with tolerance standards can lead to severe consequences, including lower productivity, waste, and ultimately legal implications. By controlling factors that affect tolerances and continually monitoring the injection molding process, manufacturers can achieve the required dimensional accuracy consistently.