Injection molding is a widely used manufacturing process used to create parts and products in numerous industries, including automotive, medical, and electronics. It is a complex process that involves various parameters, including pressure, temperature, and shear rate. In this article, we will focus on what shear rate is, its importance in injection molding, and how it can affect the quality of the final products.
What Is Shear Rate?
Shear rate is defined as the rate at which a fluid is subjected to deformation caused by a shear stress. In the context of injection molding, the shear rate is the velocity gradient at which the polymer melt is subjected to deformation in the cavity. It is the change in velocity per unit distance and is usually measured in inverse seconds (s^-1).
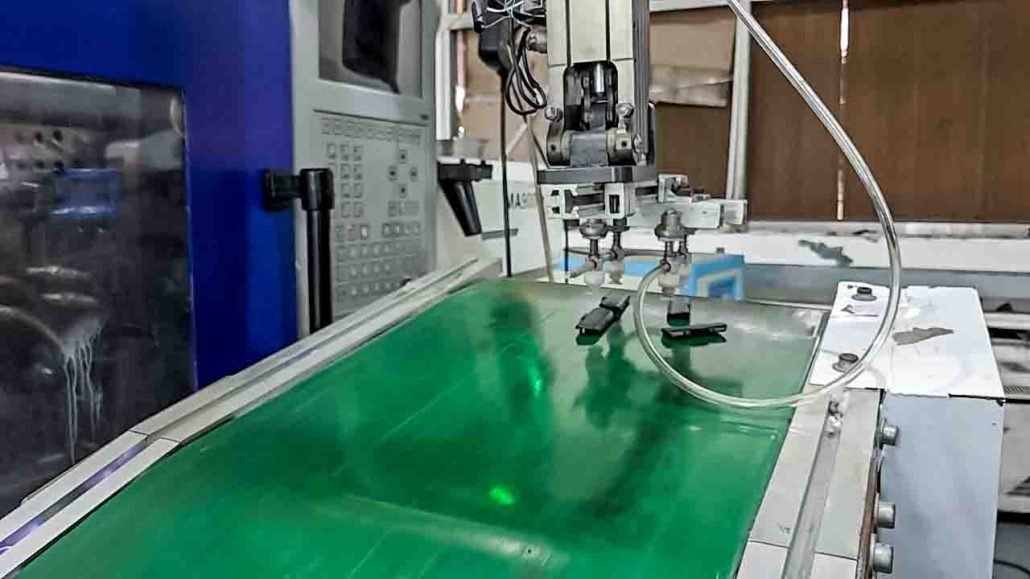
The Importance of Shear Rate in Injection Molding
Shear rate has a significant impact on the quality and properties of the final products. It affects the viscosity, molecular orientation, and shear stress of the polymer melt. Understanding the shear rate is critical to achieving consistent dimensional accuracy, surface finish, and mechanical properties.
For instance, a low shear rate can result in incomplete filling of the cavity, causing flashing and short shot parts. It can also lead to high molecular orientation, resulting in high levels of residual stresses and warpage. On the other hand, a high shear rate can cause degradation of the polymer, resulting in discoloration, gas formation, and mechanical properties deterioration.
Factors That Affect Shear Rate
Several factors can influence the shear rate in injection molding, including:
Injection speed: A faster injection speed can result in a higher shear rate as the polymer melt undergoes more deformation before it solidifies.
Wall shear stress: The shear stress exerted by the walls of the cavity can also affect the shear rate. Higher wall shear stress can lead to a higher shear rate.
Polymer viscosity: The viscosity of the polymer melt also plays a role in the shear rate. Higher viscosity polymers require more shear stress to flow, resulting in a higher shear rate.
Cavity geometry: The shape and size of the cavity can also affect the shear rate. A smaller cavity with more complex geometry can result in higher shear rates.
Additionally, shear rate also affects the cooling rate of the material, as the amount of energy imparted by the flow can influence the heat dissipation rate. This can be especially critical for high-performance thermoplastics, as improper cooling can lead to residual stress and subsequent part failure.
Controlling Shear Rate in Injection Molding
To ensure consistent part quality and properties, it is essential to control the shear rate during the injection molding process. This can be done by:
Choose the right material: Different plastic materials have different viscosity and shear rate properties. Selecting the right material for your application can help you achieve optimal shear rates.
Control the melt temperature: The melt temperature of the plastic material can affect the shear rate. A higher melt temperature can result in a higher shear rate, while a lower melt temperature can result in a lower shear rate. You need to find the right balance for your specific material and application.
Optimize the injection speed: The injection speed affects the shear rate and the cooling time of the plastic material. A higher injection speed results in a higher shear rate and faster cooling times, while a slower injection speed results in a lower shear rate and slower cooling times. You will need to experiment and find the optimal speed for your specific application.
Adjust the mold temperature: The mold temperature affects the cooling time of the plastic material, which in turn affects the shear rate. A higher mold temperature can result in a lower shear rate, while a lower mold temperature can result in a higher shear rate. You will need to experiment and find the optimal temperature for your specific application.
Conclusion
Shear rate is a critical parameter in injection molding that can significantly impact the quality and properties of the final products. By understanding the factors that affect shear rate and how to control it, injection molders can achieve consistent part quality and properties, reduce rejects, and increase production efficiency.