CNC machining technology has been widely used in many industries, can provide enterprises with high-precision, high-efficiency parts machining services, however, even the most modern CNC machine tools, there are some errors, these errors for high-precision parts machining, may lead to product waste, reduce its durability, loss costs and affect customer satisfaction.
But what exactly is the CNC process? Are you confused about the error of CNC machining parts? How to avoid reducing part error during machining? Improve product accuracy and durability. In this article, we provide a comprehensive overview of how to reduce errors in cnc machining parts, covering everything from problems to advanced considerations. Whether you have extensive experience or new processing techniques, this guide will help you make an informed decision.

What is the error of CNC machining parts?
CNC machining parts error refers to the error caused by various factors in the process of machining, such as machine accuracy, tool wear, workpiece deformation, etc. These errors are unavoidable, but their effects can be minimized by controlling the machining conditions and various parameters in the process.
The size of error has a great influence on the quality of machined parts. If the error is too large, the machined parts will not meet the design requirements, or even cannot be used. Therefore, it is very important to ensure as little error as possible during CNC machining.
Working principle of CNC machining parts
CNC machining using digital control, that is, CAD model, CAM program and other data into CNC control system identification of digital signals, in order to control the relative motion between the tool and the workpiece, to achieve parts machining.
The key of the whole machining process is CNC controller, controller is the core component that decides the machining accuracy and efficiency. It can realize the tool and workpiece position, direction and speed control, and according to the machining program Settings and data input information on its operation.
CNC machining of the specific steps
CNC machining steps mainly include three parts: data input, machining preparation, machining process. Below we will introduce each.
(1) Data input
CNC machining needs to input CAD model, CAM program or G-code and other data into CNC controller system, which is analyzed by the controller and converted into machine instructions. During data input, personnel can set certain parameters to ensure the accuracy and stability of machining.
(2) preparation for machining
Before machining, should carefully check the parts design, tool, fixture selection and installation as well as the running state of the machine and other aspects, to ensure that all conditions are in line with the requirements of machining. The more preparation work, the more successful the subsequent machining work.
(3) machining process
At the time of machining, the controller will start and run in turn according to the program set. The CNC controller will realize the control of axes, tools and workpieces by continuously sending signals. The machining process may consist of multiple steps, each of which requires precise control to ensure a high quality and efficient finish.
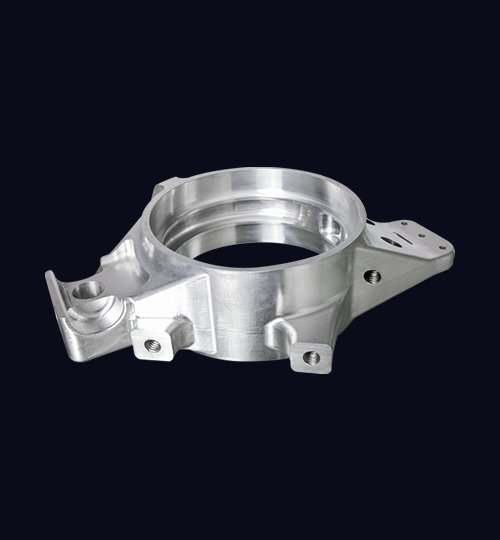
Advantages and disadvantages of CNC machining
Understanding the advantages and disadvantages of CNC machining can help you understand the appropriate machining methods, so that enterprises can get better production efficiency
Advantages:
High degree of automation
The biggest advantage of CNC machining is a high degree of automation, can realize automatic assembly line operation. Through pre-programming, CNC machining can automatically complete all machining procedures, reducing labor costs and time costs. Therefore, CNC machining is suitable for mass production and high precision requirements.
Improved machining quality
CNC machining can achieve high precision machining, because it can control the movement of machine tools through computer instructions, so as to achieve more accurate machining. This machining method can greatly improve the quality and precision of products, and reduce the errors and waste in production.
Can adapt to a variety of materials
CNC machining can adapt to a variety of materials, including plastic, metal, wood and so on, whether flat, curved surface, complex parts can be processed. This flexibility makes CNC machining suitable for many different industries.
Disadvantages:
High cost
Although CNC machining can reduce labor costs and time costs, the price of CNC machine tools is very high and requires a lot of investment. In addition, CNC operators need professional technical training and maintenance costs, increasing the operating costs of enterprises.
Pre-programming is required
CNC machining requires pre-programming, which requires a complete production plan and design drawings. This process is time-consuming, requires a large amount of manpower and technical reserves, and increases the operating costs of enterprises.
Not suitable for small batch production
The most basic advantage of CNC machining is batch manufacturing. But if only a small number of parts need to be processed, the cost of CNC machining will be higher, then it is not as good as manual machining. Therefore, CNC machining is not suitable for small batch production.

Cause of error of CNC machining parts
The reasons for the error of CNC machining parts are very complex. The following lists several main factors affecting the error:
Part design
One of the main causes of CNC machining error is the unreasonable and inappropriate part design. Too complex, too compact and geometric shape unreasonable design density, will affect the implementation of CNC machining technology.
CNC programming error
To properly execute CNC programs, human programming must meet specific requirements. In practice, however, human programming can make mistakes. These errors may lead to errors in CNC machining parts.
The machine itself is not accurate enough
In the process of using machine tools, due to the natural aging of materials and working background, it is easy to appear swing deviation and wear. Especially small machine tools, it is usually unable to meet the high accuracy requirements after a long time of use
Material quality
The quality and stability of parts materials will also affect the error of CNC machining parts. Material surface wear and deformation, material hardness, elasticity and wear and tear will affect the manufacturing quality of parts. In order to avoid these problems, detailed pretreatment of materials is needed in the machining process to improve the accuracy and stability of parts.
Tool wear
CNC machining requires the use of different tools, and tool wear will affect the manufacturing quality of parts. Worn tools tend to lose accuracy and create more marks and cutting force. These will lead to a decline in machining quality, resulting in errors in parts.
Process flow
CNC machining process is another cause of parts error. Depending on the materials and machining methods, the speed and depth of each process requires careful design, practice and joint testing. This helps ensure that each part fits perfectly.
Types of CNC machining errors
Difference is the difference between the workpiece and the design size. Errors are divided into many types. To master different types of errors is the necessary prerequisite for improving CNC machining accuracy. Several common error types are as follows:
First, linear error
Linear error is the most basic error type in CNC machining. It is usually caused by the error of the tool, the stiffness of the machine tool and the characteristics of the workpiece. Linear error can be divided into position error, straightness error and parallelism error.
(1) straightness error
Straightness error refers to the error between any straight line on the workpiece and the coordinate axis. In CNC machining process, straightness error may be caused by uneven surface of guide rail, deformation of machining track, unbalance of spindle rotor and other factors. When straightness error is large, it will affect the appearance of parts, and then affect the use effect of parts.
(2) relative position error
Relative position error refers to the error between the position deviation between two or more features, including parallelism, perpendicularity, relative position error, etc. This error will affect the workpiece installation and relative position of the match, directly affect the user’s overall use effect.
(3) parallelism error
This is due to the workpiece surface and the working face is not parallel to the error. The error of parallelism may be caused by the improper adjustment of the machine tool, the different size of the workpiece or the vibration of the machine tool during machining.
(4) Shape and size error
Shape error refers to the deviation between the shape and size of the workpiece and the shape required by the design drawing. Shape error can be divided into linear error and surface error. Among them, linear error includes straightness error, inclination error, curvature error and so on. Surface errors include flatness errors, surface errors, etc. These errors may lead to adverse effects in the assembly and use of the workpiece, such as poor fit, stuck, leakage, etc.
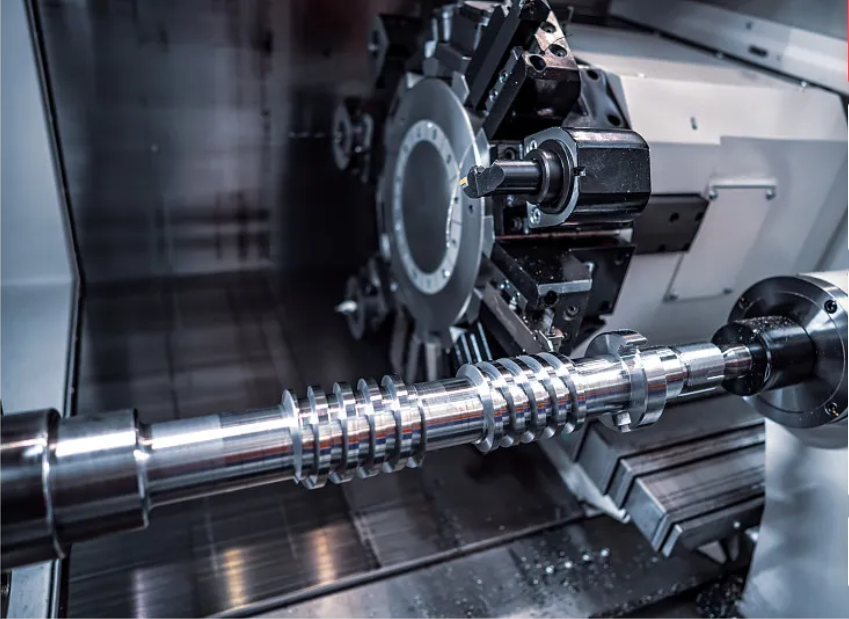
two,Temperature error
The temperature change in CNC machining process will lead to expansion or contraction of machine tools and tools, which will affect the size and accuracy of parts. The temperature error can be divided into cooling error and thermal deformation error.
(1) Thermal error
The change of temperature during machining will lead to the expansion and contraction of CNC machining tools, resulting in errors. In order to avoid thermal error, the temperature and humidity of the control space must be strengthened.
(2) Cooling error
Lubricants used in the cutting process must cool tools and workpieces to prevent overheating, but excessive coolant can cause problems with too low a temperature, which can lead to errors.
Three, Angle error
Angle error is usually caused by factors such as inaccurate tool Angle or workpiece positioning during machining parts. They include right Angle error, flatness error and roundness error.
(1) Roundness error
Roundness error refers to the error between the diameter of the outer circle or inner circle of a part and the theoretical value. In the process of CNC machining, the roundness error may be caused by the jig or spindle axis is not vertical, tool deviation and other factors. When roundness error is large, it will not only affect the appearance of parts, but also affect the use effect of parts.
(2) attitude error
Attitude error refers to the error between the workpiece’s relative attitude and the axis of spindle rotation. In the process of CNC machining, the attitude error may be caused by the workpiece surface uneven, the fixture is not vertical, the geometric accuracy of the spindle and other factors. Attitude error will lead to uneven surface, inaccurate contour shape, uneven aperture and other problems after machining.
(3) right Angle error
This is due to the workpiece surface and machining tool Angle does not match the error. For example, if the edges of the workpiece are not perfectly vertical or horizontal, a right Angle error may arise.
(4) Flatness error
This is due to the workpiece surface is not smooth or due to the tool does not adequately cover the entire surface of the error.
Four, mechanical vibration error
Mechanical vibration error is caused by the vibration of machine tools and tools, which is usually related to the running speed. Rapid cutting may cause mechanical vibration and affect the size and shape of the machining.
(1) Mechanical error
Mechanical error is the error caused by the mechanical part of CNC machine tool. These errors can be due to low precision manufacturing processes and materials used. For example, a screw may be somewhat bent or worn. This error is usually due to operator negligence or machine aging. Mechanical errors usually cause errors in several parts.
(2) Positioning error
Positioning error refers to the error between the spindle and the workpiece holding system. In CNC machining, positioning error may be caused by fixture fixing instability, workpiece material uneven, clamping force is too large or too small, fixture surface damage and other factors. When the positioning error is large, the machining accuracy of the parts cannot be guaranteed, thus affecting the use effect of the parts.
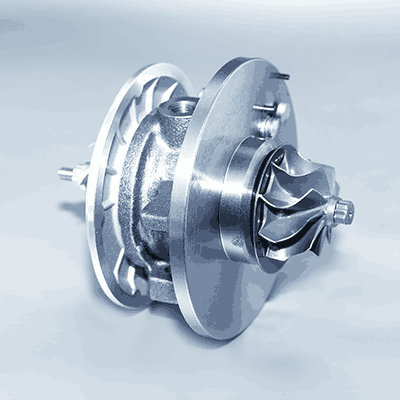
CNC machining parts error solution
What are the reasons for the error of CNC machining parts? There are mainly the following points:
- Wear and offset of cutting tools;
- Improper fastening of the fixture or the accuracy of the fixture;
- The accuracy of the machine tool itself;
- Material or process parameters;
- The operator is not skilled enough.
After determining the cause of the error in CNC machining, what measures should we take to eliminate the error?
Improve the accuracy and stability of machine tools
The accuracy and stability of machine tools have great influence on the errors in CNC machining. The more advanced and stable the machine, the smaller the error. Therefore, we should give priority to the use of high-precision and high-stability machine tools.
Proper tool placement
In order to make the tool service life longer, more stable cutting, we need to reasonably place the tool and determine the correct feed mode.
Improved cutting parameters
In the process of CNC machining, the value of cutting parameters will have a very important impact on the machining quality. We should adjust the cutting speed, cutting depth and feed, and use the appropriate coolant to ensure proper cutting quality.
Improve machining technology
The difference of machining technology often affects the manufacturing quality of parts. The more advanced the technology, the smaller the machining error. Therefore, we should improve the machiningg skills of workers, adopt high quality process specifications, and improve the processing accuracy through continuous accumulation of experience.
In addition, the error can also be solved by means of multi-process machining, compensation, calibration and so on. These methods need to be carried out according to the actual situation.
Finally, it needs to be emphasized that the error is very common in CNC machining, and solving the error problem is not an overnight process, the need for manufacturers and engineers to constantly summarize and improve, boldly try new technology, new methods, and actively apply them to improve the quality of products and work efficiency.
This article introduces part of the solution to CNC machining parts error is too large, I hope to help you. For more information about CNC machining and precision machining, please pay attention to us.
Longsheng Technology