In the process of precision parts machining , selecting appropriate materials is crucial for the performance and quality of the parts. CNC machining, as a high-precision and high-efficiency machining method, provides a good solution for the manufacturing of precision parts.
In this article, we will provide detailed guidance on material selection in CNC machining to help engineers make accurate material choices in practical applications.
CNC Machining Overview
CNC machining is an automatic machining method based on computer numerical control technology. Through pre-written program instructions, the machine tool is controlled for precise cutting and machining operations. CNC system is composed of computer, controller and machine tool, through the transmission of programming instructions and motion control signals, to achieve the accurate positioning and machining of the workpiece in multiple axes.
The advantage of CNC machining is that it can achieve high precision, high efficiency and flexibility, and can be applied to the manufacturing of parts with various complex shapes and precision requirements.
It is widely used in many fields, including aerospace, automotive, medical, electronics and mold manufacturing. By using CNC machining, you can improve the accuracy, consistency and productivity of part machining while reducing the need for manual operation.
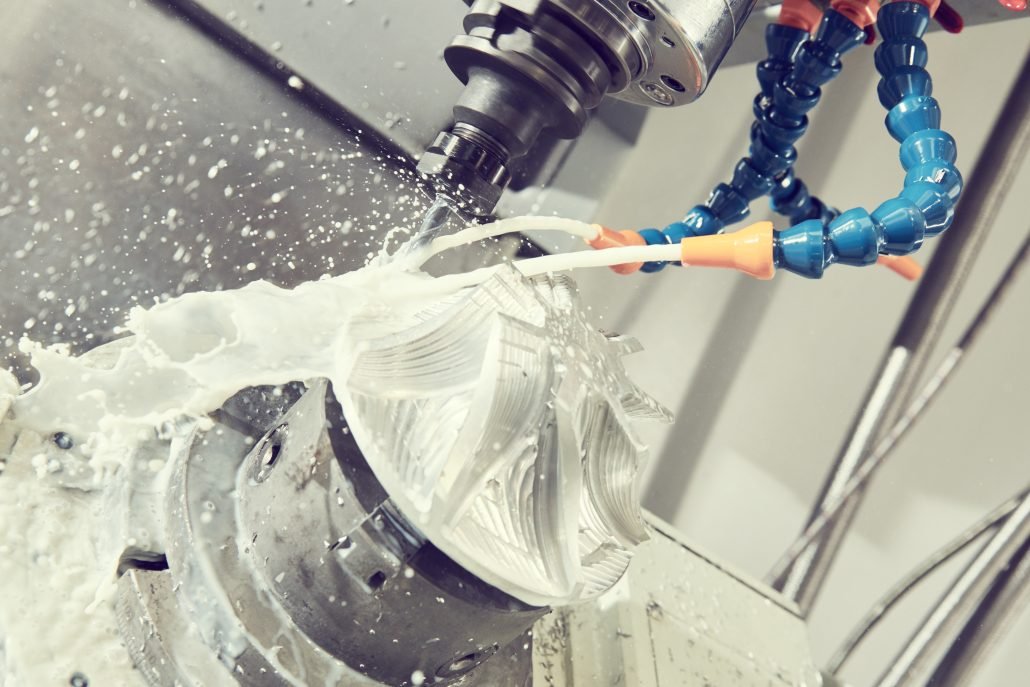
importance of material selection
Choosing the right material has a significant impact on the mechanical properties, physical properties and durability of the final part. Only through the right material selection can we meet the high requirements for precision parts in different industries and applications
Key factors in selecting the right material:
Application requirements: Consider the function of the part, the use of the environment and working conditions, choose the material that can meet the application needs. Different applications may have specific requirements for the properties and characteristics of the material.
machining difficulty: Consider the machining performance and machining difficulty of the material, including cutting performance, machining deformation and tool life. Select materials that are easy to process and have good cutting properties to improve processing efficiency and quality.
Cost-effectiveness: Consider the cost and availability of materials to ensure that materials that are economically viable and have good properties are selected. Balance the relationship between material quality and cost so that material selection achieves the best results in terms of cost effectiveness.
Option 1:metallic material
1.steels
Common types and characteristics of steel
The following is an introduction to common types of steel and their characteristics:
Steel Type | Characteristics | Applications |
---|---|---|
1045 Carbon Steel | Medium carbon content, easy to machine and heat treat | Bearings, shafts, gears, bolts, fasteners, etc. |
4140 Alloy Steel | High strength, good toughness and wear resistance | Forgings, bearings, gears, hydraulic piston rods, etc. |
316 Stainless Steel | Good corrosion resistance, high temperature resistance, and oxidation resistance | Chemical equipment, food machining equipment, ship components, etc. |
H13 Tool Steel | Excellent heat resistance and wear resistance, maintains dimensional stability | Plastic molds, die casting molds, hot press molds, extrusion molds, etc. |
A2 Tool Steel | Good cutting performance and toughness, suitable for highly precise machining | Die molds, cutting tools, blades, punches, etc. |
D2 Tool Steel | High hardness and excellent wear resistance, maintains dimensional stability | Cutting tools, dies, blades, punches, stamping molds, etc. |
CNC machining applicability of steel and matters needing attention
Steel is widely used in CNC machining, with good machining performance and a wide range of uses. However, different types of steel may have some specific applicability and limitations during machining . The following is the general applicability of CNC machining of steel and some precautions:
Carbon steel: Carbon steel has good machinability and is suitable for most CNC machining operations. They are easy to cut and form and have a low cost. However, for high-carbon steel and quenched carbon steel, due to its higher hardness and brittleness, it may be necessary to use more suitable tools and processes to ensure machining quality and tool life.
Stainless steel: Stainless steel has good corrosion resistance and mechanical properties, and is often used in CNC machining parts that require corrosion resistance. The machining of stainless steel is more challenging than carbon steel, because stainless steel usually has higher hardness and lower thermal conductivity, which can easily lead to tool wear and machining difficulties. For stainless steel, the choice of the right tool and cutting parameters is crucial to improve machining efficiency and quality.
Alloy steel: Alloy steel usually has high strength, high hardness and good wear resistance. Due to the addition of alloying elements, machining will increase a certain degree of difficulty. Alloy steel has poor machinability and great tool wear. When machining alloy steel, the appropriate tool materials and coatings should be selected, and the appropriate cutting speed and feed speed should be used to ensure the machining quality and tool life.
Tool steel: Tool steel usually has high hardness, high wear resistance and excellent cutting properties. However, due to its high hardness and toughness, machining tool steel may require the use of more wear-resistant tools and more stable cutting conditions. For the machining of tool steel, precise cutting process control and cooling lubrication are usually required.

2.Aluminium alloy
Common aluminum alloy types and characteristics
The following is an introduction to the common types and characteristics of aluminum alloys in CNC machining:
Aluminum Alloy | Characteristics | Applications |
---|---|---|
6061 Aluminum Alloy | Moderate strength, good weldability and corrosion resistance | Aerospace components, bicycle frames, automotive parts, sporting equipment, electronic equipment housings, etc. |
7075 Aluminum Alloy | High strength, excellent corrosion resistance and fatigue resistance | Aerospace components, high-pressure vessels, racing parts, bicycle parts, rock climbing equipment, etc. |
2024 Aluminum Alloy | High strength, good toughness, and heat treatable response | Aircraft structural components, aircraft bolts, spacecraft structural components, racing parts, motorcycle parts, etc. |
5083 Aluminum Alloy | Good corrosion resistance and weldability, high strength and seawater corrosion resistance | Ship structural components, offshore platforms, storage tanks, automotive body parts, bridges, etc. |
6063 Aluminum Alloy | Good formability and corrosion resistance, easy to machine and weld | Construction and architectural decorations, window frames, door frames, rail transportation components, electronic heat sinks, etc. |
5052 Aluminum Alloy | Good corrosion resistance and tensile strength, easy to form and machine | Automotive body panels, electronic equipment housings, aerospace components, ship structural components, etc. |
Aluminum alloy CNC machining applicability and precautions
Aluminum alloy has a wide range of applicability in CNC machining, with light weight, high strength and good machining properties, so it is widely used in various industrial fields. However, different types of aluminum alloys may have some specific applicability and limitations during machining . The following is the general applicability of CNC machining aluminum alloy and some precautions:
6061 aluminum alloy: 6061 aluminum alloy has moderate strength, good weldability and corrosion resistance. It is a commonly used aluminum alloy that is easy to process in CNC machining and suitable for most applications. However, for higher strength parts, appropriate tools and machining parameters may be required to avoid excessive heat treatment leading to part deformation.
7075 aluminum alloy: 7075 aluminum alloy has high strength, excellent corrosion resistance and fatigue resistance. However, due to its higher hardness, machining may require the use of more wear-resistant tools and appropriate cutting parameters. In addition, 7075 aluminum alloy is sensitive to thermal deformation, so it is necessary to pay attention to controlling cutting temperature and cooling lubrication during machining .
2024 aluminum alloy: 2024 aluminum alloy has high strength, good toughness and heat treatment response. Due to its high hardness and brittleness, it is necessary to use appropriate tools and cutting parameters during machining to avoid cracks and deformation. In addition, since 2024 aluminum alloy is sensitive to corrosion, care should be taken to keep the machining environment dry and clean.
5083 aluminum alloy: 5083 aluminum alloy has good corrosion resistance and weldability, as well as high strength and seawater corrosion resistance. When machining 5083 aluminum alloy, attention should be paid to selecting the appropriate cutting fluid and cooling lubrication to avoid hot cracks and hot deformation.
6063 aluminum alloy: 6063 aluminum alloy has good plasticity and corrosion resistance, easy to process and weld. When machining 6063 aluminum alloy, the conventional cutting process can be used, but care needs to be taken to maintain the appropriate cutting speed and feed speed to avoid excessive heat treatment and cutting vibration.
5052 aluminum alloy: 5052 aluminum alloy has good corrosion resistance and tensile strength, easy to form and process. When machining 5052 aluminum alloy, it is necessary to pay attention to controlling the cutting parameters and the use of cutting fluid to avoid excessive cutting and the generation of hot cracks.
3.Copper and its alloys
Common types and characteristics of copper and its alloys
The following is an introduction to the types and characteristics of copper and its alloys commonly used in CNC machining:
Copper and Alloy | Characteristics | Applications |
---|---|---|
Electrolytic Copper | High purity, excellent conductivity and thermal conductivity | Electronic devices, wires, electrodes, connectors, etc. |
Brass | Alloy with zinc, good ductility and corrosion resistance | Keys, watches, decorative items, pipes and fittings, etc. |
Red Copper | Alloy with higher copper content, good conductivity and thermal conductivity | Cables, wire terminals, water pipes, electrical sockets, etc. |
Bronze | Alloy with tin or other alloying elements, high strength and corrosion resistance | Sculptures, clock parts, ship components, mechanical parts, etc. |
Copper-Nickel Alloy | Alloy with nickel, good corrosion resistance and wear resistance | Ship equipment, marine engineering, chemical equipment, chemical storage tanks, etc. |
Aluminum Bronze | Alloy with aluminum and zinc, good wear resistance and corrosion resistance | Automotive engine parts, turbine blades, aerospace components, etc. |
Applicability and considerations for CNC machining of copper and its alloys
Copper and its alloys have a wide range of applicability in CNC machining, with good electrical conductivity, thermal conductivity and plasticity, so it is widely used in electronics, machinery, construction and other fields. However, different types of copper and their alloys may have some specific applicability and limitations during machining . The following are the general applicability and some considerations of CNC machining copper and its alloys:
Electrolytic copper: electrolytic copper has high purity, good electrical and thermal conductivity, and is suitable for the machining of precision electronic devices. Due to its low hardness, electrolytic copper is easy to cut and form. During the machining process, attention should be paid to controlling tool wear and avoiding excessive heating.
Brass: Brass is an alloy of copper and zinc with good plasticity and corrosion resistance. Brass is easy to process and is suitable for making accessories, clocks, pipes and fittings. When machining brass, attention should be paid to controlling the cutting speed and the use of lubricants to avoid excessive heating and tool wear.
Red copper: Red copper is an alloy with a higher copper content and has good electrical and thermal conductivity. Red copper is widely used in cable, terminal, water pipe and electrical socket and other fields. When machining red copper, it is necessary to select the right tool and cutting parameters to achieve accurate machining and high-quality surface quality.
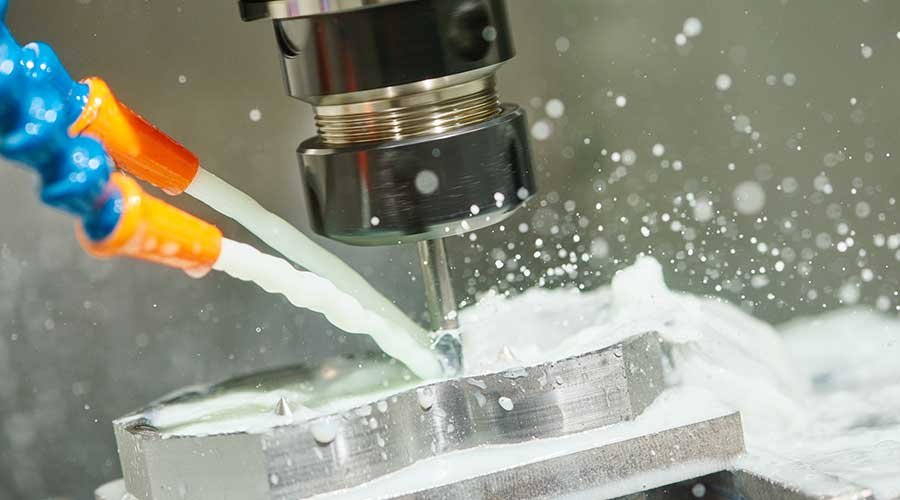
Bronze: Bronze is a copper alloy containing tin or other alloying elements, which has high strength and corrosion resistance. Bronze is often used in the fields of sculpture, watch parts, ship parts and mechanical parts. When machining bronze, appropriate cutting tools and cooling lubrication measures should be selected to control the cutting temperature and extend the tool life.
Copper-nickel alloy: Copper-nickel alloy contains nickel and has good corrosion resistance and wear resistance. They are suitable for Marine equipment, Marine engineering, chemical equipment and chemical storage tanks. When machining copper-nickel alloy, appropriate tool materials and cutting parameters should be selected to control cutting heat and improve machining efficiency.
Aluminum bronze: Aluminum bronze is a copper alloy containing aluminum and zinc, which has good wear resistance and corrosion resistance. They are suitable for automotive engine parts, turbine blades, aerospace parts and other fields. When machining aluminum bronze, it is necessary to select wear-resistant tools and appropriate cutting parameters to maintain machining accuracy and extend tool life.
4.Titanium and its alloys
Common types and characteristics of titanium and its alloys
Titanium and Alloy | Characteristics | Applications |
---|---|---|
Pure Titanium | High strength, lightweight, excellent corrosion resistance, and biocompatibility | Medical devices, aerospace, chemical, marine engineering, etc. |
Ti6Al4V Alloy | High strength, good mechanical properties, heat-treatable, and corrosion resistance | Aerospace, automotive, marine, medical devices, sports equipment, etc. |
Ti-5553 Alloy | High strength, excellent corrosion resistance, and fatigue resistance | Aerospace, marine, automotive, high-performance mechanical parts, etc. |
Ti-3Al-2.5V Alloy | Good ductility, toughness, and corrosion resistance | Aerospace, marine, automotive, sports equipment, electronic devices, etc. |
Ti-6Al-2Sn-4Zr-6Mo Alloy | High strength, corrosion resistance, and fatigue resistance | Medical devices, aerospace, marine, sports equipment, chemical equipment, etc. |
Ti-6Al-2Nb-1Ta-0.8Mo Alloy | High strength, excellent toughness, and corrosion resistance | Aerospace, marine, chemical equipment, sports equipment, electronic devices, etc. |
CNC machining applicability and precautions of titanium and its alloys
Titanium and its alloys are widely used in CNC machining due to their excellent strength-to-weight ratio, corrosion resistance and biocompatibility. However, there are some factors and limitations that need to be considered when machining titanium and its alloys. The following is a discussion of the applicability and limitations of titanium and its alloys in CNC machining, as well as machining methods and considerations for different types of titanium and its alloys:
Pure titanium
Applicability: Pure titanium has good machining properties and is suitable for many fields such as medical implants, aerospace parts and chemical equipment.
Note: Pure titanium has a high chemical reactivity and requires care in tool selection and cutting parameter control to control heat generation and prevent tool wear.
Ti6Al4V alloy (Grade 5 titanium)
Applicability: Ti6Al4V is one of the most common titanium alloys and is widely used in many industries such as aerospace, automotive and medical. It has good strength, weight ratio and corrosion resistance.
Note: Ti6Al4V has a tendency to work hardening, which can lead to increased cutting forces and tool wear. Appropriate cutting parameters, tool selection and cooling lubrication are critical to maintaining machining efficiency and surface quality.
Other titanium alloys (e.g. Ti-5553, Ti-3Al-2.5V, Ti-6Al-2Sn-4Zr-6Mo, Ti-6Al-2Nb-1Ta-0.8Mo)
Suitability: These titanium alloys are specifically designed for high performance applications such as aerospace, Marine and chemical, requiring superior strength, corrosion resistance and fatigue.
Note: Machining these alloys may require the use of specialized cutting tools such as coated carbide or ceramic blades to withstand high temperature cutting and maintain tool life. Controlling cutting parameters, tool wear and chip removal is essential to ensure successful machining.
CNC machining of titanium needs to pay attention to the following matters:
Tool selection: Use appropriate tool materials, such as carbide or ceramic tools, to cope with the high hardness and high temperature of titanium.
Cutting parameters: Adjust cutting speed, feed speed and cutting depth to control cutting temperature and reduce cutting pressure.
Cooling lubrication: Use sufficient cutting fluid or lubricant for cooling and lubrication to reduce cutting temperature and extend tool life.
Tool wear monitoring: Regular inspection and replacement of severely worn tools to maintain good machining quality and efficiency.
Thermal deformation control: When machining large or complex shaped titanium parts, appropriate cooling measures need to be taken to control thermal deformation
5.Stainless steel
Common types and characteristics of stainless steel
Stainless Steel Type | Characteristics | Applications |
---|---|---|
304 Stainless Steel | Good corrosion resistance, strong oxidation resistance, easy to process and weld | Construction, decoration, kitchenware, food machining equipment |
316 Stainless Steel | Excellent corrosion resistance, good heat resistance, high strength, and wear resistance | Chemical, marine, medical devices, food machining equipment |
430 Stainless Steel | Good corrosion resistance, easy to polish, heat and magnetism resistant | Construction, appliances, kitchenware, automotive components |
201 Stainless Steel | Good corrosion resistance, easy to process and shape, moderate strength | Construction, decoration, furniture, electronics |
410 Stainless Steel | High hardness, good wear resistance, excellent heat treatability | Tools, bearings, valves, pressure vessels |
904L Stainless Steel | Excellent corrosion resistance, strong acid resistance, good resistance to stress corrosion cracking | Chemical, petroleum, marine, pharmaceutical |
Stainless steel CNC machining applicability and precautions
Stainless steel CNC machining. The applicability and limitations of stainless steel in CNC machining are discussed below, and machining methods and considerations for different stainless steels are provided.
Suitability of stainless steel
Corrosion resistance: Stainless steel has excellent corrosion resistance and is suitable for applications requiring durability and corrosion resistance.
Strength: Stainless steel has a high strength and is suitable for applications requiring high strength and rigidity.
Temperature stability: Stainless steel can maintain stability at high temperatures and is suitable for high temperature applications.
Sanitary performance: Stainless steel has excellent sanitary performance and easy to clean characteristics, suitable for food machining and medical equipment and other fields.
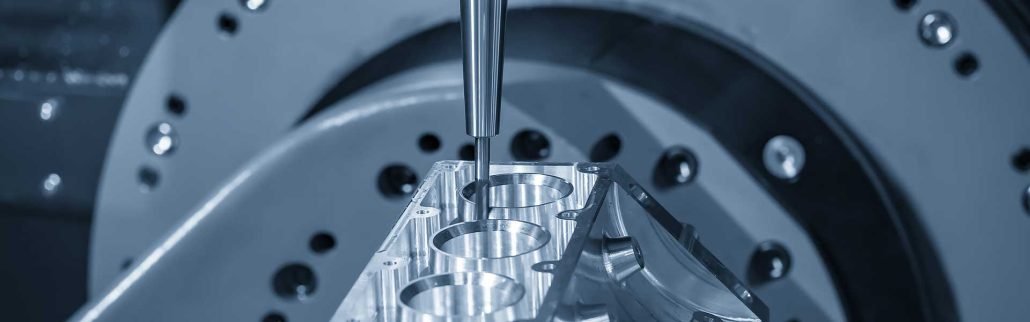
Stainless steel limitations
Hardness: Stainless steel is relatively hard, has a certain impact on tool wear, may need to use wear-resistant tools.
Thermal conductivity: The thermal conductivity of stainless steel is low, and it is easy to generate heat when cutting, and it is necessary to reasonably control the cutting speed and cutting depth to avoid overheating.
Machinability: stainless steel machinability is relatively poor, easy to produce cutting force, need to choose the right cutting parameters and tools to reduce cutting pressure.
For different stainless steel machining methods and precautions:
304 stainless steel: has good machining properties, suitable for general CNC machining operations. Be careful to avoid overheating and excessive cutting pressure.
316 stainless steel: Better corrosion resistance, the need to use high-hardness tools, and take appropriate cutting parameters and cooling measures.
430 stainless steel: easy to cut and form, but with high thermal conductivity, pay attention to reasonable control of cutting speed and cooling lubrication.
201 Stainless steel: easy to process and form, suitable for general CNC machining operations, pay attention to avoid overheating.
410 stainless steel: harder, need to use high hardness tools, and appropriate cutting parameters adjustment and cooling lubrication.
904L stainless steel: Better corrosion resistance, the need to use special tools and appropriate cutting parameters, pay attention to control the cutting temperature.
Note:
Tool selection: According to the hardness and heat resistance of stainless steel, select the appropriate tool material and tool coating.
Cutting parameters: Adjust cutting speed, feed speed and cutting depth to control cutting temperature and cutting force.
Cooling lubrication: Cooling and lubrication with appropriate cutting fluid or lubricant to reduce heat and tool wear.
Prevent cross contamination: Avoid cross contamination of stainless steel with other metal materials to prevent corrosion and surface contamination.
Option 2:Non-metallic material
1.plastic
Common types and characteristics of plastics
Plastic Type | Characteristics | Applications |
---|---|---|
Polyethylene (PE) | Lightweight, flexible, corrosion-resistant, high impact strength | Packaging materials, plastic bags, bottles, household items |
Polypropylene (PP) | High strength, good rigidity, corrosion-resistant, high temperature resistance | Food containers, medical devices, automotive components |
Polyvinyl Chloride (PVC) | Durable, low cost, heat-resistant, good insulation properties | Construction materials, wire and cable insulation, pipes, window frames |
Polystyrene (PS) | Rigid, transparent, easy to process, good impact resistance | Food packaging, electronic products, household items |
Polycarbonate (PC) | High strength, high temperature resistance, high transparency, good impact resistance | Automotive parts, electronic components, eyeglasses, safety equipment |
Polyethylene Terephthalate (PET) | Strong, temperature-resistant, chemical-resistant, easily recyclable | Beverage bottles, fiber products, plastic films, industrial applications |
Polytetrafluoroethylene (PTFE) | Non-stick, high temperature resistance, corrosion-resistant, good electrical insulation | Non-stick cookware, sealing materials, wire and cable insulation, chemical pipelines |
Polyurethane (PU) | High strength, wear-resistant, oil-resistant, heat-resistant, tear-resistant | Shoe soles, car seats, foam filling materials, coatings |
Plastic CNC machining applicability and precautions
The following discusses the applicability and limitations of plastics in CNC machining, and provides machining methods and considerations for different plastics.
Suitability of plastics:
Machinability: Plastics usually have good machinability and are easy to cut, drill, mill and turn.
Lightweight properties: Plastics have lightweight properties and are suitable for applications that require lightweight, such as the aerospace and automotive industries.
Chemical resistance: Many plastics have good chemical resistance and are resistant to corrosion and solvents.
Insulation properties: Plastics usually have good insulation properties and are suitable for electronic and electrical fields.
Plastic limitations:
Heat sensitivity: Some plastics will soften or deform at high temperatures, so the machining temperature needs to be controlled during machining .
Melting point and fusibility: plastics have different melting points and fusibility, so it is necessary to control the speed of heating and cooling during machining .
Cutting performance: The cutting performance of different plastics is different, and different tools and cutting parameters may be required.
Surface quality: Some plastics may appear cutting marks or melt marks, need to pay attention to the quality of the machined surface.
machining methods and precautions for different plastics:
PE, PP and other low melting point plastics: control the machining temperature, the use of appropriate tools and cutting parameters to avoid overheating and melting.
PVC, PS and other high melting point plastics: control the heating and cooling speed, the use of high hardness tools for cutting.
PC, PET and other high temperature resistant plastics: using low speed cutting and cooling lubrication, control the cutting temperature to avoid melting and deformation.
Non-adhesive plastics such as PTFE: Use low-speed cutting and lubricants to avoid adhesion and heat accumulation.
2.Composite material
Common types and characteristics of composite materials
Composite Material | Characteristics | Applications |
---|---|---|
Carbon Fiber Composite | High strength, lightweight, good rigidity, corrosion-resistant, high temperature resistance | Aerospace, automotive, sporting goods, marine, construction, etc. |
Glass Fiber Composite | Good mechanical properties, strong corrosion resistance, excellent insulation properties | Construction, automotive, marine, wind energy, electronics, etc. |
Prepreg Composite | High strength, heat-resistant, corrosion-resistant, easy to shape | Aerospace, automotive, sporting goods, construction, electronics, etc. |
Steel-Plastic Composite | Combines the strength of steel and the lightweight properties of plastic | Construction, bridges, vehicle manufacturing, structural engineering, etc. |
Aluminum-Based Composite | Good strength, rigidity, lightweight, excellent corrosion resistance | Aerospace, automotive, construction, electronics, etc. |
Carbon Nanotube Composite | High strength, lightweight, good electrical conductivity, thermal stability | Aerospace, electronic devices, sporting goods, energy storage, etc. |
applicability and precautions of CNC machining of composite materials
The following discusses the applicability and limitations of composites in CNC machining, and provides machining methods and considerations for different composites.
Suitability of composite materials:
High strength and lightweight properties: Composites with high strength and lightweight properties are suitable for applications requiring strength and weight advantages.
Corrosion and heat resistance: Composite materials usually have good corrosion and heat resistance, suitable for harsh environments or high temperature applications.
Design flexibility: The composition of the composite material can be adjusted to meet different design requirements.
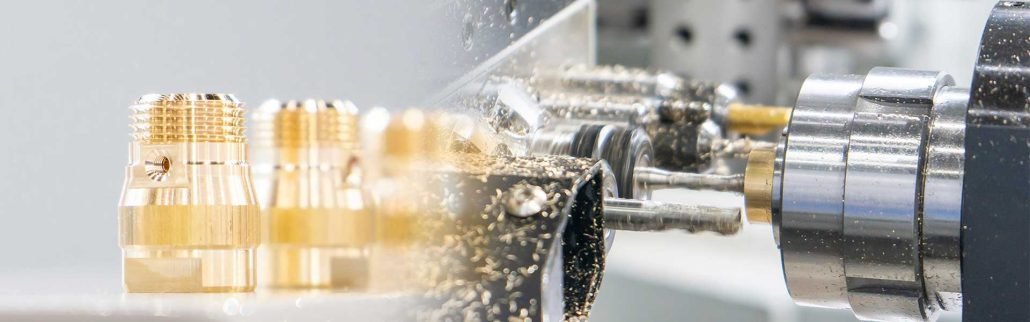
Limitations of composite materials:
Cutting difficulty: Composite materials usually have high hardness and strength, so the appropriate tool and cutting parameters need to be used when cutting to prevent excessive wear or damage to the tool.
Fiber orientation: The fibers in the composite have specific directivity, which can lead to the stripping or breaking of the fibers during the cutting process, so it needs to be handled carefully.
Chip management: The chip generated by the composite material during the cutting process is relatively fragile, and appropriate chip management measures are needed to avoid the chip blocking or damaging the workpiece surface.
Adhesion issues: The cutting process of composite materials can cause adhesion and heat buildup, requiring cooling and lubrication measures to reduce adhesion and extend tool life.
machining methods and precautions for different composite materials:
Carbon fiber composites: Use high hardness tools and appropriate cutting parameters to control cutting temperature and cutting force to avoid fiber breakage and stripping.
Glass fiber composite material: The use of high-speed cutting and cooling lubrication, pay attention to the direction of the fiber and the management of cutting chips.
Prepreg composites: Select the appropriate tool and cutting parameters, control the cutting temperature and cutting force, avoid overheating and fiber damage.
Steel-plastic composites: Using the appropriate cutting tools and cutting parameters, pay attention to the differences in cutting characteristics between plastic and steel.
Aluminum matrix composites: Use the right cutting parameters and tool materials to avoid overheating and aluminum adhesion problems.
Carbon nanotube composites: Select appropriate cutting tools and cutting parameters, and pay attention to the electrical conductivity and thermal stability of carbon nanotubes.
3.ceramics
Common types and characteristics of ceramics
Common Types of Ceramics and Their Characteristics:
Ceramic Type | Characteristics | Applications |
---|---|---|
Alumina Ceramic | High hardness, good wear resistance, excellent corrosion resistance, good insulation properties | Mechanical parts, abrasives, electronic ceramics, thermal barrier coatings, medical instruments, etc. |
Silicon Nitride Ceramic | High hardness, good wear resistance, high temperature resistance, strong chemical stability | Cutting tools, bearings, nozzles, valves, abrasives, etc. |
Zirconia Ceramic | High strength, high hardness, good wear resistance, good corrosion resistance, high temperature stability | Chemical equipment, medical instruments, grinding media, electrolytes, etc. |
Silicon Carbide Ceramic | High hardness, good wear resistance, high temperature resistance, excellent chemical stability, good thermal conductivity | High temperature equipment, electronic devices, grinding media, thermal oil pump bearings, etc. |
Aluminum Nitride Ceramic | High hardness, good wear resistance, high temperature resistance, good thermal conductivity | Electronic devices, cutting tools, grinding media, thermal barrier coatings, etc. |
Ceramic Composites | Combine the characteristics of different ceramics, such as high strength, high hardness, wear resistance, and corrosion resistance | Aerospace, chemical equipment, mechanical parts, heat treatment tools, etc. |
Ceramic CNC machining applicability and precautions
The following discusses the applicability and limitations of ceramics in CNC machining, and provides machining methods and considerations for different ceramics.
Applicability of ceramics:
High hardness and wear resistance: Ceramics typically have extremely high hardness and excellent wear resistance and are suitable for applications that require high wear resistance and rigidity.
High temperature resistance: Many ceramics have excellent high temperature resistance and are suitable for applications in high temperature environments.
Good insulation properties: Ceramics have excellent insulation properties and are suitable for electrical and electronic applications.
Ceramic limitations:
Brittle: Ceramic materials are usually fragile and prone to fracture or fragmentation, requiring careful handling and machining .
Difficult-to-process: Due to the high hardness and brittleness of ceramic materials, the selection of tools and machining parameters requires higher requirements, and the machining is more difficult.
Surface quality: The surface of ceramic materials is prone to scratches and damage, so appropriate machining methods and process control need to be taken to obtain good surface quality.
machining methods and precautions for different ceramics:
Alumina ceramics: Use diamond or polycrystalline cubic boron nitride cutting tools, with low cutting speed and high cutting force control, pay attention to the cooling of the tool and cutting lubrication.
Silicon nitride ceramics: Choose carbide or cubic boron nitride cutting tools, using high-speed cutting and cooling lubrication, control the cutting temperature.
Zirconia ceramics: Use diamond tools, control cutting speed and cutting force, avoid overheating, pay attention to ceramic and tool wear.
Silicon carbide ceramics: Use carbide or diamond tools, control the cutting speed and cutting force, pay attention to the wear and adhesion of ceramics and tools.
Aluminum nitride ceramics: Choose diamond or polycrystalline cubic boron nitride cutting tools, using high cutting speed and cutting force, paying attention to cutting temperature and tool cooling.
Ceramic composite materials: According to the specific composition and characteristics of the composite material to select the appropriate tool and machining parameters, pay attention to control the cutting temperature and cutting force.
Influence of material parameters
1.hardness
Influence of hardness on CNC machining
Selecting the appropriate hardness grade standards and hardness test methods can help engineers evaluate the material’s cutting performance, surface quality requirements and machining stability, so as to optimize the CNC machining process and results, the following discussion of the importance and influence of hardness in CNC machining, and introduce hardness test methods and common hardness grade standards.
importance of hardness
Cutting performance: The hardness of the material directly affects the tool wear and cutting force during the cutting process. Higher hardness will increase the wear and cutting force of the cutting tool and reduce the machining efficiency.
Surface quality: Hardness has an important effect on the finish and roughness of the machined surface. Harder materials often require higher machining accuracy and surface quality requirements.
machining stability: Materials with high hardness have better deformation resistance and thermal stability, and can maintain good machining stability under high load and high temperature environment.
Hardness test method
Brinell Hardness: Hardness is measured by applying an indentation diameter under a certain load to the surface of a material.
Rockwell Hardness: Hardness is measured by indentation depth under a certain load applied to the surface of a material.
Vickers Hardness: Hardness is measured by applying a microscopic indentation length under a certain load to the surface of a material.
Common hardness grading standards
Hardness rating standards are usually developed according to different material types and application needs. Common hardness grading criteria include:
International Hardness Scale (IHS)
FHS (Fahrenheit Hardness Scale)
Rockwell Hardness Scale (RHS)
Brinell Hardness Scale (BHS)
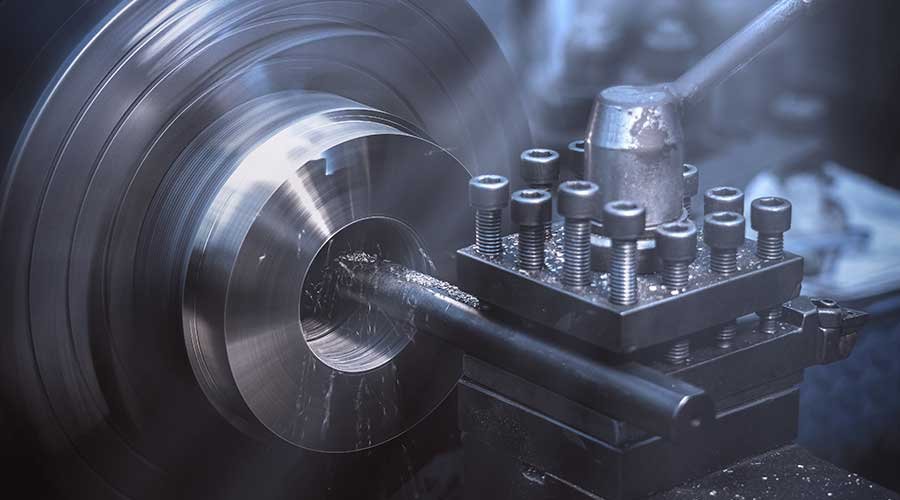
machining methods and precautions for materials with different hardness
When machining materials with different hardness, the appropriate cutting tools and cutting parameters should be selected according to the material characteristics and machining requirements. The following is a guide for the selection of cutting tools and cutting parameters for materials with different hardness, and discusses the challenges and solutions that may be encountered.
machining methods and precautions for materials with different hardness:
When machining materials with different hardness, it is very important to choose the appropriate cutting tools and cutting parameters. The following is a guide to the selection of cutting tools and cutting parameters for different hardness materials, and discusses possible challenges and solutions.
Low hardness materials (such as aluminum, plastic, etc.) :
Cutting tools: ordinary HSS (high speed steel) tools or solid carbide tools.
Cutting parameters: higher cutting speed and feed speed, larger cutting depth.
Challenges and solutions: Avoid excessive heating, control cutting forces, and prevent tool clamping.
Medium hardness materials (such as carbon steel, alloy steel, etc.) :
Cutting tools: solid carbide tools, coated tools (TiN, TiAlN, etc.).
Cutting parameters: moderate cutting speed and feed speed, moderate cutting depth.
Challenges and solutions: Control tool wear, use appropriate cutting lubricants, pay attention to tool cooling.
High hardness materials (such as stainless steel, titanium alloy, etc.) :
Cutting tools: coating tools (TiAlN, AlCrN, etc.), cubic boron nitride tools.
Cutting parameters: lower cutting speed and feed speed, smaller cutting depth.
Challenges and solutions: Control the cutting temperature, pay attention to cutting forces and tool wear, and use appropriate cutting lubricants.
Superhard materials (such as ceramics, silicon carbide, etc.) :
Cutting tools: diamond tool, polycrystalline cubic boron nitride tool.
Cutting parameters: low cutting speed and feed speed, small cutting depth.
Challenges and solutions: Control cutting temperature and tool wear, pay attention to cutting forces, use cutting lubricants and cooling.
2.Thermal conductivity
Influence of thermal conductivity on CNC machining
In CNC machining, for materials with low thermal conductivity, heat accumulation can be reduced by increasing the cutting speed, reducing the cutting temperature, using cutting lubricants and other measures, the importance and influence of thermal conductivity in CNC machining are discussed below, and the influence of thermal conductivity on machining temperature control and thermal deformation is discussed
Importance of thermal conductivity:
Temperature control: Thermal conductivity determines the heat conduction capacity of the material during machining , affecting the distribution and stability of the machining temperature. Higher thermal conductivity can better disperse and release the heat generated during the machining process, which is conducive to controlling the machining temperature.
Thermal deformation: The heat generated during machining can cause thermal expansion and deformation of the material. Higher thermal conductivity allows faster transfer of heat to the surrounding environment, reducing the risk of heat buildup and thermal deformation.
Influence of thermal conductivity on machining temperature control:
Materials with high thermal conductivity: Materials with high thermal conductivity can better disperse and conduct the heat generated during machining , helping to control the rise and distribution of machining temperatures. This helps reduce heat buildup and heat damage, and improves machining quality and stability.
Materials with low thermal conductivity: Materials with low thermal conductivity tend to accumulate heat during machining , resulting in local temperature increases. This may cause problems with thermal stress and thermal deformation, and may affect the dimensional accuracy and surface quality of the part.
The influence of thermal conductivity on thermal deformation:
Materials with high thermal conductivity: Materials with high thermal conductivity are able to transfer heat to the surrounding environment more quickly, reducing heat accumulation and thermal stress, and reducing the risk of thermal deformation. This is particularly important for machining materials that are prone to thermal deformation at high temperatures.
Materials with low thermal conductivity: Materials with low thermal conductivity may be difficult to dissipate heat rapidly during machining , easily leading to local temperature increases and thermal stress accumulation. This can cause problems with thermal deformation and dimensional instability.
machining methods and precautions for different thermal conductivity materials
When machining materials with different thermal conductivity, heat dissipation design and cutting process optimization need to be considered. The following is the heat dissipation design and cutting process optimization recommendations for different thermal conductive materials, and emphasizes the thermal stress problems and solutions that need to be paid attention to in the machining of thermal conductive materials.

High thermal conductivity materials (such as copper, aluminum, etc.) :
Heat dissipation design: Increase the heat dissipation contact area between materials and cutting tools, and use heat dissipation devices such as heat sinks and radiators to improve heat dissipation efficiency.
Cutting process optimization: High cutting speed and feed speed are used to control cutting temperature to avoid excessive heating and heat accumulation.
Thermal stress problem: high thermal conductivity materials are prone to thermal stress during machining , resulting in deformation and dimensional instability of parts. Solutions include increasing the flow and pressure of the cutting coolant, using low temperature cutting fluid, and adequate cooling.
Low thermal conductivity materials (such as plastics, ceramics, etc.) :
Heat dissipation design: Consider the heat dissipation characteristics and heat capacity of the material, and use heat dissipation equipment and heat dissipation structure to improve heat dissipation efficiency.
Cutting process optimization: reduce cutting speed and feed speed, avoid local overheating and heat accumulation, reduce thermal stress and deformation.
Thermal stress problem: Low thermal conductivity materials are prone to thermal stress during machining , especially when cutting at high speed. Solutions include cutting lubrication with coolant, reducing the cutting temperature, and using cutting methods that reduce heat accumulation (such as spiral inserts).
Medium thermal conductivity materials (such as alloy steel, titanium alloy, etc.) :
Heat dissipation design: According to the thermal conductivity and heat capacity of the material, select the appropriate heat dissipation structure and cooling equipment to improve heat dissipation efficiency.
Cutting process optimization: According to the material characteristics, select the appropriate cutting parameters, control the cutting temperature, avoid excessive heating and heat accumulation.
Thermal stress problem: Medium thermal conductivity materials may produce large thermal stress during machining , resulting in deformation and dimensional instability. Solutions include cutting lubrication with cooling lubricants, controlling cutting temperatures and cutting forces, and using appropriate cutting strategies (such as reducing the depth of cutting).
3.intensity
Influence of strength on CNC machining
The strength of Cnc machining materials it affects the tensile, compressive and bending resistance of parts under stress. The following is an explanation of the importance and influence of strength in CNC machining, and explores the influence of strength on the tensile, compressive and bending resistance of parts under stress.
importance of strength:
Structural stability: Strength is the ability of a part to resist external loads and internal stresses, and is essential to ensure the structural stability and safety of a part.
Load carrying capacity: Strength determines the maximum load carrying capacity of a part when it is stressed, which is essential to withstand working conditions in high strength and high stress environments.
influence of strength on the mechanical capacity of parts:
Tensile capacity: Strength determines the tensile capacity of a part under tensile load, that is, how much tension it can withstand without damage. Higher strength means that the part has higher tensile strength and can withstand greater tensile loads.
Compressive strength: Strength is equally important to the ability of a part to withstand compressive loads. Higher strength means that the parts have higher compressive capacity and can withstand greater compressive loads.
Bending capacity: Strength also affects the bending capacity of a part under bending load. Higher strength means that the part is better able to resist bending stress and has better rigidity and bending strength.
machining methods and precautions for materials of different strength
When machining materials of different strengths, it is necessary to consider the appropriate machining technology and fixture design. The following are the machining process and fixture design recommendations for different strength materials, and highlight the cutting problems and solutions that may be encountered in the machining of strength materials.
High-strength materials (such as high-strength steel, titanium alloy, etc.) :
machining technology: Appropriate cutting parameters, such as cutting speed, feed speed and cutting depth, are used to reduce cutting heat and cutting force. Use suitable cooling lubricants for cutting lubrication, control process temperature and thermal stress.
Fixture design: Design a robust fixture to stabilize the workpiece and reduce vibration and deformation. Consider the rigidity requirements and fixed position during the machining process to ensure that the fixture can effectively transfer the cutting force.
Medium strength materials (such as ordinary steel, aluminum alloy, etc.) :
machining technology: Select the appropriate cutting parameters, according to the characteristics of the material and machining requirements, control the cutting temperature and cutting force. Adjust the cutting speed and feed speed for the best machining results.
Fixture design: According to the shape and structural characteristics of the workpiece, design the fixture to provide adequate support and stability. Ensure the rigidity and precise positioning of the fixture to maintain the accuracy and stability of the workpiece.
Low strength materials (such as plastic, wood, etc.) :
Machining process: Reduce cutting speed and feed speed to avoid excessive cutting and damage to the material surface. Select the appropriate tool type and tool geometry to get the best cutting results.
Fixture design: Considering the deformation and displacement characteristics of the workpiece, design the fixture to provide adequate support and fixation. Ensure proper contact between the fixture and the material, and avoid excessive stress on the material caused by the fixture.
Sample bill of materials
Sample list of metal materials
Here are some examples of common metal material lists:
- Carbon steel
- Stainless steel
- Aluminium alloy
- copper
- Titanium alloy
- Magnesium alloy
- zinc
- Nickel alloy
- lead
- iron
- Cobalt alloy
- Chromium alloy
- silver
- tungsten
- Molybdenum alloy
Sample list of non-metallic materials
Here are some examples of common non-metallic material lists:
- plastic
- glass
- ceramic
- rubber
- Fiber composite
- polymer
- polyester
- polyurethane
- polythene
- polypropylene
- Polyvinyl chloride
- polystyrene
- polycarbonate
- Polyether ketone
- Polyether sulfone
conclusion
In this paper, we discuss the importance of material selection in CNC machining and highlight the impact of material selection on precision part machining. In CNC machining, factors such as application requirements, machining difficulty and cost effectiveness should be comprehensively considered to ensure the selection of the most suitable materials.
As a CNC machining service provider, we are committed to providing quality machining solutions to our customers. If you are looking for precision parts machining services, we invite you to take the next step and contact us. We have advanced equipment, experienced engineers and professional teams to meet your customized needs and provide high quality machining services.
Whether you need single-piece machining or mass production, we will be happy to provide you with excellent service. Contact us and let us make your project a success!
gloria.wu@longshengmfg.com
FAQ
When selecting materials, specific requirements and application requirements of the parts should be considered, such as mechanical performance, corrosion resistance, temperature stability, etc. At the same time, it is also necessary to consider factors such as the processability, availability, and cost-effectiveness of the material.
For different materials, appropriate cutting tools, machining strategies and machining equipment can be selected according to their characteristics, such as high-speed milling, wire cutting, milling machining centers, etc.
For cutting fragile materials, suitable fixtures and support structures can be used to reduce material vibration and deformation, and appropriate cutting tools and parameters can be selected to reduce the risk of fracture.