CNC machining technology is a kind of advanced machining technology, it will transfer the computer program instructions to the CNC machine tool, the realization of digital control machining , with high precision, high efficiency, high flexibility and so on. In the field of aerospace, CNC machining technology has been widely used, become an important means to promote the design and manufacture of aircraft.
Aerospace engineering is a field of high precision and high requirements, requiring component size, shape and surface quality to reach extremely high levels. CNC machining technology to meet these requirements show superiority.
In this blog of Longsheng Technology website, we will provide information about the technical difficulties of CNC machining and the challenges you may encounter and their solutions. So read on.
Aerospace CNC machining: Purpose and application
CNC machining is a kind of computer numerical control machining technology, in the process of aircraft manufacturing, its main purpose is to achieve high precision, high quality, high efficiency, high stability of the parts machining . The machining requirements of these parts are very high, once the problem will directly affect the safety and reliability of aircraft. CNC machining technology can better meet these requirements, to ensure that the aircraft performance indicators meet the design requirements. At the same time, CNC machining technology can also greatly reduce the complexity of the process, improve production efficiency, reduce production costs.
Parts manufacturing in the aerospace field is very complex and requires a variety of different types of machining . CNC machining technology can be applied to a variety of different parts machining , common including:

Aircraft structural parts machining
These components generally refer to the fuselage, wing, tail and other structural components, complex shape, high precision requirements. CNC machining can quickly and accurately process various shapes of structural parts by controlling the motion of the tool in the three-dimensional space.
Engine parts machining
Aero-engine is one of the most important parts of aircraft, it needs a variety of different types of parts to support the work. Such as turbine, impeller, shaft, tank, etc., the quality and accuracy of these components have a direct impact on the operation of the engine. CNC machining technology can accurately process these parts to ensure that their accuracy and quality meet the requirements.
Avionics component machining
The electronic equipment of modern aircraft is very complex, including radar, navigation, communication, control and other systems. The precision parts of these devices need to be finished by CNC machining.
Basic design guidelines for aerospace parts
The design of aerospace parts requires compliance with specific guidelines to ensure accuracy and optimal performance. The following summarizes the basic design guidelines for aerospace parts and introduces you to how to design aerospace parts with high performance, safety, reliability, and economic utility
Material selection guide
Parts in the aerospace industry must withstand high temperature, high pressure, high speed and other environmental tests. Therefore, in the selection of materials, need to consider its strength, corrosion resistance, temperature tolerance and other factors. In CNC machining, choosing the right machining material can reduce the difficulty of machining , while greatly increasing the service life of parts. Common materials for machining include:
Material Type | Characteristic | Application Field | Other |
---|---|---|---|
Aluminium alloy | High strength, light weight and excellent corrosion resistance | Other aircraft components such as wings and hull structures | Common Aluminum alloys include Aluminum 2024, Aluminum 6061, and Aluminum 7075 |
Titanium alloy | It has good heat resistance, corrosion resistance and strength | Structural parts of aircraft and spacecraft, engine blades, suspension systems and braking systems | Common titanium alloys include Ti-6Al-4V, Ti-5Al-2.5Sn and Ti-3Al-2.5V |
Stainless steel | High strength and corrosion resistance | Propeller and engine | Common stainless steel materials in the field of aerospace include AISI 304, AISI 321 and AISI 347 |
superalloy | High temperature and corrosion resistance | Materials for high-temperature components such as engines, turbines and jet engines | |
Composite material | Excellent strength, stiffness and corrosion resistance | Important materials used to make key parts of aircraft such as surfaces and structures | |
Carbon fiber reinforced composites | With light weight, high strength, high stiffness, corrosion resistance and other excellent characteristics | Manufacture the wings, tail fins and horizontal stabilizer | |
Tungsten alloy | High hardness and corrosion resistance | It is often used to make engine parts, hubs and rotors | |
Resin-based composites | High strength, high modulus, fatigue resistance, corrosion resistance, good insulation performance | Manufacture hydraulic fuel tank, evaporator and other aviation assembly parts | |
Ceramic material | Strong heat resistance, corrosion resistance and shock resistance | Aircraft combustion chamber, engine turbine and other components manufacturing | |
Nickel-based alloy | High temperature corrosion resistance, high strength | Manufacturing high-temperature components such as gas turbines, jet engines and turbine blades | |
Cobalt-base alloy | High temperature corrosion resistance, high temperature strength, high temperature hardness and heat fatigue | Manufacturing of high-temperature components such as gas turbines, turbine blades and jet engines |
Structural design
In the structural design of aerospace parts, the structure of the parts should be accurate, necessary, practical and stable, in order to ensure that it can play a good performance in space, high altitude and harsh environment. Therefore, we need to fully consider the various parameters of the design of mechanical parts, such as size, weight, strength and so on, in order to obtain the best structural performance.
In the structure design of CNC machining parts, the following principles need to be followed:
Meet the design specifications: the design of CNC machining parts must meet the specifications and standards of aircraft design, shall not violate national laws and regulations and technical standards.
Strengthen science and practicality: consider science and practicality simultaneously, evaluate the feasibility of the structure, and ensure that other requirements are not destroyed while achieving the objectives.
Pay attention to weight reduction: in the design of CNC machining parts, the weight of parts should be reduced as far as possible, but the strength and reliability of parts should not be affected.
Improve reliability and life: the reliability and service life of parts should be improved from the aspects of material, structural form, manufacturing process and detection to ensure the safety and reliability of parts under high load and harsh environment.

Dimension and tolerance design
The size and tolerance of aerospace parts are very important, which is directly related to the quality and performance of the parts, so the size and shape of the parts need to be clear in the design. Dimensions here include length, width, height, diameter and other basic parameters. Shape refers to the geometry of a part, such as cylindrical, conical, spherical, etc. In determining the size and shape, factors such as the actual use, process and material of the part need to be considered. In the actual design, we can use CAD technology for 3D modeling, in order to better grasp the size and shape of parts.
Secondly, we need to determine the tolerance requirements of the parts. Tolerance refers to the permissible size deviation range of parts. It is an important means to control the dimensional accuracy of parts. The tolerance requirements of aerospace parts are very high, usually within 0.01mm. In determining the tolerance requirements, it is necessary to consider the use of parts, process requirements and other factors, but also need to combine the characteristics of materials, machining accuracy and other factors for comprehensive consideration.
In order to ensure the parts machining accuracy, we need to use high-precision machining equipment and technology, as well as reasonable fixtures, tools and other tools to ensure the machining accuracy.
Surface quality requirement
Aerospace parts usually have high requirements for surface quality. Because aerospace parts are subjected to extreme conditions, including high temperature, high pressure, violent vibration, etc., if the surface roughness is too high or the flatness is insufficient, the parts may be damaged or lose function, so ensure that the finish, roughness, flatness and perpendicularity of the processed surface meet the design requirements, and carry out appropriate surface finishing, such as polishing, electroplating, etc., the specific requirements are as follows:
Surface smoothness
CNC machining parts surface must be smooth, no roughness and bumpy situation. The smoothness of the surface must meet certain standards to ensure normal operation, and the smoothness can be measured on the surface roughness meter. If the surface smoothness is not up to the standard, follow-up machining is required.
Surface hardness
The surface hardness of CNC machining parts is very important. Hardness can ensure that the parts have enough durability and protection to reduce the occurrence of major failures in the course of aerospace applications. Surface hardness can also be tested using a durometer.
Surface cleanliness
CNC machining parts in the production process will produce certain pollutants, if not cleaned, will affect the performance and accuracy of the parts. Therefore, the surface of CNC machining parts must have high quality cleanliness, to ensure that the performance and accuracy of parts are guaranteed.
Surface oxidation and corrosion
Due to the extreme environment of parts in the aerospace and aviation industries, the surfaces of CNC machined parts must be treated against oxidation and corrosion. Anti-oxidation and anti-corrosion treatment can reduce the corrosion and peeling of parts in use, and further improve the service life of parts.
Surface coating
CNC machining parts through oxidation and adhesion of surface coating, surface quality can be greatly improved. The surface coating can reduce the loss and degradation of parts in use, while reducing the failure and problems caused by their surface properties.
Tool path planning
Whether it is aircraft or rocket, reasonable planning CNC machining tool path, in order to minimize the machining time, improve the machining efficiency and ensure the machining accuracy. At the same time, avoid excessive cutting force and vibration in the cutting process.
Depending on the material and shape, we can use different cutting tools and machining techniques. For example, when machining high-strength materials, high-speed drills and ultra-hard cutting tools can be used to reduce tool wear and machining time. At the same time, we can take advantage of advanced CNC machining technology to ensure that the tool path design is more efficient and accurate.
The following are the key points of tool path planning:
1.Depth of cutting and feed rate. The cutting depth and feed speed should be selected according to the material of the parts and the different machining objects, in order to achieve the best machining effect and quality.
2.Tool radius and angular radius. The choice of tool radius and sharp Angle radius is related to the shape and size of parts and other factors, should be reasonable according to the specific situation.
3.Tool wheel path and tool return path. Tool wheel path and back path should be based on the shape of the workpiece and contour distribution and other factors to ensure that the cutting process will not produce unnecessary stress and deformation of the parts.
4.Tool motion path and machining route. Tool trajectory and machining route and cutting Angle, cutting Angle, feed Angle and other factors, need to be reasonable distribution and arrangement according to the specific situation, in order to ensure machining efficiency and quality.
Design documentation and identification
In order to ensure the traceability of parts and production quality management, detailed design documentation of parts is recorded, and the unique identifying information of parts is identified, such as part number, batch number, serial number, etc.
The aerospace parts design document shall contain the following information:
1.Parts drawing: including 3D model, size, material, tolerance and other information.
2.Design specification: describes the functions, requirements and usage scenarios of the parts in detail.
3.Design check list: check whether the requirements of function, performance, process, material, appearance and other aspects of parts are met.
4.Process documents: including process route, machining method, inspection standard, etc.
5.Test file: a detailed record of the parts tested.
The above information shall be detailed, accurate and completely recorded to facilitate management and inspection in the production process. Accurate design documentation can greatly improve the efficiency of parts manufacturing and avoid defects in production.

Other considerations for aerospace parts design practice
In addition to basic design guidelines, aerospace parts design practices need to consider the following aspects:
Material performance verification
The material properties of aerospace parts must be verified, including the strength, hardness, toughness, fatigue life, etc. Material testing and analysis is usually required to ensure that the material selected conforms to the design requirements.
System integration
Aerospace parts usually exist as part of a system, so the design needs to consider the coordination and interface with other parts, to ensure the interaction and coordination of each part.
Environmental adaptability
Aerospace parts operate in different environmental conditions, including high temperature, low temperature, high pressure, low pressure and other extreme conditions. The adaptability and performance stability of parts in these environments need to be considered in the design.
Reliability and safety
Reliability and safety of aerospace parts are key considerations. The design needs to take into account the life of parts, failure rate, fatigue performance, etc., to ensure that the parts can operate normally within the service life and meet the safety requirements.
Manufacturing feasibility
The manufacturing feasibility and manufacturing cost of parts should be considered in the design process. Select appropriate machining techniques and methods to ensure that parts can be mass-produced at a reasonable cost.
Repair and maintenance
The repair and maintenance of aerospace parts is necessary and needs to be designed with repairability and maintainability in mind. Reasonable design can simplify the maintenance process and reduce the maintenance cost.
Lightweight design
The aerospace field pursues lightweight components to reduce the weight and fuel consumption of aircraft. The design should take into account the structural strength and reduce the weight of parts as much as possible.
Modern design tools
The use of modern design tools and software, such as computer-aided design (CAD) and computer-aided engineering (CAE), can improve the accuracy and efficiency of design.
These are some of the key factors that need to be considered in the aerospace parts design practice. Designers need to make comprehensive tradeoffs and decisions while ensuring performance and safety.
Aerospace CNC machining parts challenges and solutions
Aerospace CNC machining parts face many challenges. The following are some common challenges and their solutions:
Complex geometry
Aerospace parts usually have complex geometric shapes, such as surfaces, holes, etc. This increases the difficulty and complexity of machining
Solution
For complex shapes and high precision requirements, we need to make full use of 5-axis and multi-axis CNC machine tools. These machine tools have higher flexibility and customizability, which can better meet the machining needs of different shapes of parts. In addition, we also need to use advanced CAD/CAM software in the process of programming and machining to ensure the accuracy and stability of machining.
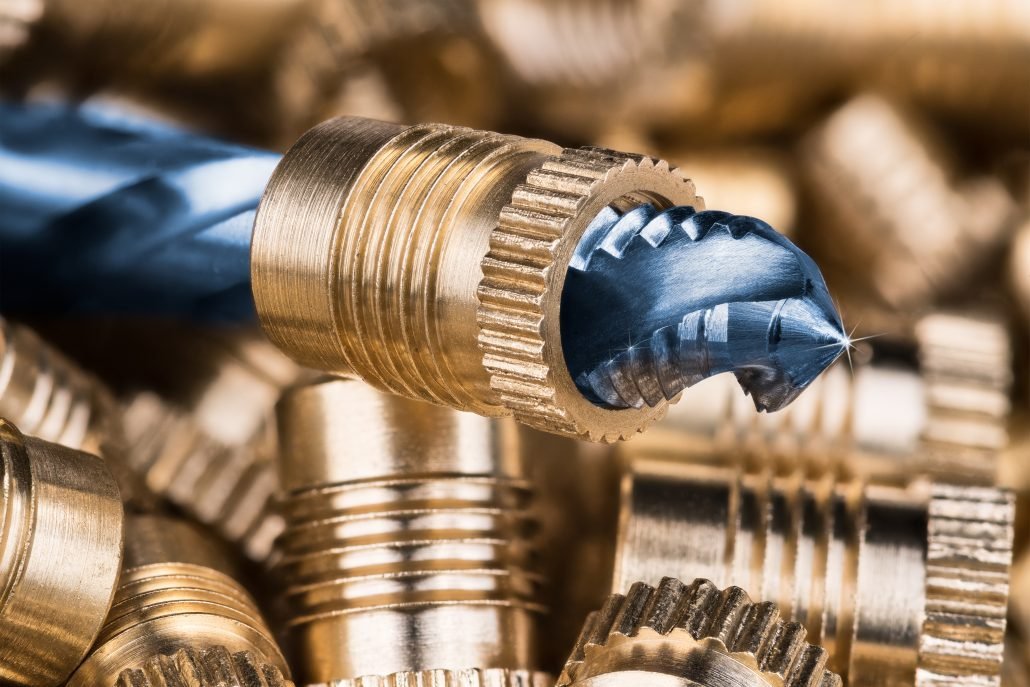
High precision requirement
In the aerospace industry, high precision requirements are a must. Even small size deviations can cause mechanical failure. Therefore, when CNC machining aerospace parts, it must be processed in strict accordance with the requirements. Specifically, it is necessary to apply a variety of processes and technologies in parts machining , including machining methods, process parameters, tool selection and so on. In addition, shorten the machining time and reduce the precision error should be considered in the process of parts machining .
Solution
In the parts machining , must be in strict accordance with the machining requirements of the operation, and regularly check the performance of online CNC machining equipment. In addition, the use of high precision CNC machine can ensure that the machining meets the requirements. CNC control system high precision, can control the machining process of each parameter, to ensure the machining accuracy. At the same time, the CNC machine can preheat the workpiece to achieve higher stability.
Difficult material
Aerospace parts often use high strength, high temperature materials, such as titanium alloy, nickel base alloy, these materials are difficult to process.
Solution
First of all, according to the actual requirements of the parts, choose the appropriate cutting tools and cutting parameters, the use of advanced tool coating and coolant, in order to improve the cutting efficiency and reduce the cutting force, or the use of ultrasonic machining , it can reduce the heat generated in the machining process, reduce the possibility of mechanical deformation of the workpiece. Ultrasonic machining can also control the vibration in the machining process, so as to improve the machining precision.
Process reliability and stability
In the field of aerospace, every part plays a vital role, any parts damage or failure may cause irreversible consequences, so in the process of CNC machining parts, we must ensure high reliability and stability.
Solution
It is necessary to strengthen quality management in the design and operation of CNC machining equipment to achieve process reliability and stability. Moreover, the quality and performance of the parts can be ensured through the most advanced inspection and testing equipment. In addition, AI technology can also help in process control and quality inspection.
Personnel training and management
CNC machining technology is a technology that requires rich experience and skills, which requires a long time of training and experience accumulation. Moreover, the talents needed in the field of aerospace are very scarce, which brings certain difficulties to the cultivation of talents.
Solution
It is necessary to pay attention to the importance of talent cultivation and management, and actively carry out professional training and skill upgrading to actively cope with the talent problem of enterprises. At the same time, it can attract more experienced and skilled talents to enhance the technical level and innovation ability of enterprises.

Do you need aerospace CNC machining parts?
Whether you need high quality aerospace parts, it is up to you again! Longsheng technology CNC machining services can meet your exact requirements.
Longsheng Technology as a professional production of high precision parts, we have rich experience in aerospace CNC machining parts manufacturing, and strictly follow the ISO9001 quality management system standards to ensure the quality of each part. Our machines and equipment have been professionally adjusted and calibrated, with high precision, high speed and efficient machining capabilities.
In addition, we use advanced CAD/CAM software, capable of 3D design and simulation, and provide digital guidance for the entire production process. This not only greatly improves the precision and efficiency of parts machining , but also can better meet customer needs. In the process of parts machining , we will strictly follow the quality control process to ensure that the quality of each part meets customer requirements.
If you need aerospace CNC machining parts services, please feel free to choose Longsheng Company. We will be dedicated to provide you with professional and efficient service. Whether you need aerospace parts such as aircraft structural parts, engine parts or satellite probe parts, we are able to provide targeted solutions and ensure the quality of parts meet international standards to ensure the safety, reliability and high quality of parts.
Any need please feel free to contact us, we will serve you wholeheartedly