If you need to manufacture high-precision, high-strength and high-quality parts, then titanium alloy may be your best choice. Compared with other metals, titanium alloys have better corrosion and wear resistance, and are also lighter. However, when you are machining titanium alloys, you need to use the right tools and equipment.
Choosing a suitable CNC machining tool for titanium has a crucial role in improving production efficiency and product quality. This article will show you how to choose a suitable CNC machining tool for titanium in order to achieve the best machining results.
Titanium alloy introduction
Titanium alloy is a high-strength, low-density metal material, its density is about 60% of aluminum, but has higher strength than steel, better electrical conductivity than silver and other excellent properties. Titanium alloy has good chemical stability and strong corrosion resistance, and is very suitable for use in high temperature, high pressure and strong corrosion environment.

Types and properties of titanium alloys
Titanium alloy refers to the alloy material composed of titanium and other metal elements. According to different alloying elements and proportions, it can be divided into α type, β type and α+β type three. The properties of each titanium alloy material are also different, so when choosing CNC machining titanium tools, it is necessary to choose the corresponding tools according to different titanium alloy types.
Grade | Description | Density (g/cm³) | Melting Point (℃) | Thermal Conductivity (W/m·K) | Young’s Modulus (GPa) | Tensile Strength (MPa) | Yield Strength (MPa) | Elongation (%) |
---|---|---|---|---|---|---|---|---|
Grade 1 | Commercially pure titanium, low oxygen content, excellent corrosion resistance, good formability, and weldability. | 4.51 | 1668 | 21.9 | 116 | 240 | 170 | 24 |
Grade 2 | Commercially pure titanium, slightly higher oxygen content than Grade 1, good corrosion resistance, excellent formability, and weldability. | 4.51 | 1668 | 21.9 | 116 | 345 | 275 | 20 |
Grade 3 | Commercially pure titanium, higher oxygen content than Grade 2, good corrosion resistance. | 4.51 | 1668 | 21.9 | 116 | 450 | 380 | 18 |
Grade 4 | Commercially pure titanium, higher oxygen content than Grade 3, good corrosion resistance. | 4.51 | 1668 | 21.9 | 116 | 550 | 483 | 15 |
Grade 5 (Ti-6Al-4V) | Titanium alloy with 6% aluminum and 4% vanadium, excellent combination of high strength, lightweight, and corrosion resistance. | 4.43 | 1660 | 6.7 | 113.8 | 895 | 828 | 10 |
Grade 7 | Titanium alloy with 0.2% palladium, excellent corrosion resistance and weldability. | 4.51 | 1668 | 21.9 | 116 | 345 | 275 | 20 |
CNC machining titanium tool types
There are many types of titanium knives, each with a specific purpose. Here are some of the most common titanium tools:
1.Solid titanium carbide cutting tool
Solid carbide titanium cutters are made of a hard tungsten carbide alloy. This alloy is very durable and can withstand high pressures and temperatures in CNC cutting. Solid titanium carbide cutting tools are usually suitable for slotting, milling and drilling. Their advantage is that they perform very well in the machining of high-strength materials.
2.PCD titanium tool
PCD titanium cutter is a superhard material made of polycrystalline cube diamond. Because the PCD titanium tool is very hard and tough, it can be processed on high-hardness materials. This tool is suitable for high-speed drilling, cutting and rapid material removal. At the same time, the advantages of PCD titanium tools are their long life and low production costs.

3.CBN titanium cutting tool
CBN titanium cutters are superhard materials made of boron nitride. The CBN titanium tool performs well because it can handle high-hardness materials well, while also removing materials easily and cutting at high speeds, suitable for high-precision drilling and thread manufacturing. Their advantages include their high efficiency and increased productivity.
4.Tungsten steel titanium tool
Tungsten titanium cutters are usually made of tungsten steel alloy and are suitable for drilling, milling and cutting hard materials. Their advantage is that tungsten steel has a relatively low cost, and has excellent hardness and wear resistance. Tungsten steel titanium cutters can also drill and cut metal or wood.
5.Titanium cutting tool
Titanium alloy Titanium cutter is a tool made of titanium and is very useful for machining titanium alloys and other light and strong metals. Such tools tend to have tungsten-cobalt blades, which allows them to drill and cut metal by rotating at high speeds. Titanium alloy Titanium tools have the advantage of performing well when handling very large and strong titanium alloys.
6.Ceramic titanium cutter
Ceramic titanium cutters are superhard materials made of alumina or silicon nitride that can be used to cut steel, aluminum and copper. Due to the excellent wear resistance and thermal properties of this tool, it is very suitable for high-speed machining. Ceramic titanium tools have a longer life due to their much higher tool quality, making them ideal for high-quality titanium tools.
7.Diamond titanium cutter
Diamond titanium cutters are superhard materials made from natural diamonds or manufactured diamonds. They are commonly used to cut materials such as glass, plastic and fiberboard. Diamond titanium cutters are more resistant to wear and handling than other titanium cutters and can greatly improve machining efficiency in terms of sliding and milling.
Tool Type | Advantages | Disadvantages |
---|---|---|
Solid Carbide | High hardness and wear resistance, suitable for high-speed cutting. | Expensive, susceptible to impact and vibration damage. |
PCD Tool | Extremely high hardness and wear resistance, suitable for high-speed cutting and precision machining. | Expensive, susceptible to impact and vibration damage, not suitable for cutting high-temperature titanium alloys. |
CBN Tool | High hardness and thermal stability, suitable for cutting hard titanium alloys and high-temperature titanium alloys. | Expensive, susceptible to impact and vibration damage. |
High-Speed Steel | Good rigidity and impact resistance, suitable for general cutting and rough machining. | Not suitable for high-speed cutting and precision machining, relatively shorter tool life. |
Titanium Alloy | Specifically designed for titanium alloy machining, excellent rigidity and heat resistance. | Higher tool cost, may require specialized coolant and cutting parameter settings. |
Ceramic Tool | High hardness, high thermal stability, and low friction coefficient, suitable for high-speed and dry cutting. | Susceptible to impact and vibration damage, prone to chipping. |
Diamond Tool | Extremely high hardness and wear resistance, suitable for high-speed cutting and precision machining. | Expensive, susceptible to impact and vibration damage, not suitable for cutting high-temperature titanium alloys. |
Recommendations for choosing cnc machining titanium tools
When choosing the right titanium tool, there are several key aspects to consider:
1.material
The material of titanium cutting tool should be a high-quality alloy material with high hardness, deep hardening, strong wear resistance and high film quality. At present, mainly the use of tungsten molybdenum, tungsten molybdenum titanium, tungsten molybdenum cobalt, tungsten carbide (superhard) and other materials for manufacturing.
2.Tool shape and geometric parameters
The shape and geometric parameters of titanium cutting tools should adopt advanced shape design and manufacturing technology with high strength and high stability to make their cutting stability and high machining accuracy.
3.Cutting edge machining technology and coating technology
The cutting edge of titanium tool has an important effect on the machining quality. Effective cutting edge treatment can ensure the cutting performance of titanium tools. Now commonly used coating materials are PVD coating, CVD coating, PAVD coating and so on.
4.Tool life and economy
The service life and economy of titanium tools is an important consideration in the selection of titanium tools, and titanium tools with longer service life and higher economy should be selected according to the machining materials, machine tools and equipment.

For some special machining processes, special titanium tools must be selected to be used together, such as:
1.High-speed cutting
When cutting at high speed, it is necessary to select titanium tools with high rigidity and high speed, pursue high precision cutting surface, and solve the problem of milling black surface.
2.Boring holes
When boring, it is necessary to select titanium tools that can meet the accuracy requirements of parts, have good tip performance and cutting edge to process.
Titanium alloy machining difficulty
The machining difficulty of titanium alloy is mainly manifested in the following aspects:
1.High hardness
The hardness of titanium alloy is very high, generally can reach more than 350HB, and the hardness of Ti-6Al-4V alloy can reach 440HB in common titanium alloys. This makes titanium alloys difficult to process in conventional machining or cold machining processes, which usually require the use of hot machining processes such as heating.
2.Low thermal conductivity
The thermal conductivity of titanium alloy is very poor, which makes it difficult for titanium alloy to dissipate heat in time during machining , easily leading to workpiece deformation and tool damage.
3.Burning explosive
Titanium alloy is very easy to burn at high temperatures, and the oxides released during the combustion process are strong oxidants, which will accelerate combustion and lead to loss of control
solution
Although the machining difficulty of titanium alloy raw materials is higher than other materials, there are many solutions that can reduce the difficulty.
1.Use molybdenum tungsten alloy cutting tools. Due to the hardness of titanium alloy, it is easy to wear the cutting tool head, and molybdenum tungsten alloy is more durable, extending the life of the cutting tool.
2.Use the latest machining tools. Because titanium alloys are difficult to process, newer machining tools are more suitable for special requirements of titanium alloys, such as extending service life and reducing machining costs.
3.Reduce cutting speed. Titanium alloys can reduce overheating by reducing the cutting speed, and reduce the risk of tool head damage and bonding.
4.Use the latest coolant. The use of high quality coolant can reduce the machining temperature and reduce the failure caused by machining .
cNC machining of titanium surface finishing
After CNC machining of titanium materials, some surface treatment methods can be taken to improve its performance and appearance. Here are some common CNC machining titanium surface treatment options
1.pickling
2.polishing
3.passivation
4.nitriding
5.anodizing
6.coating
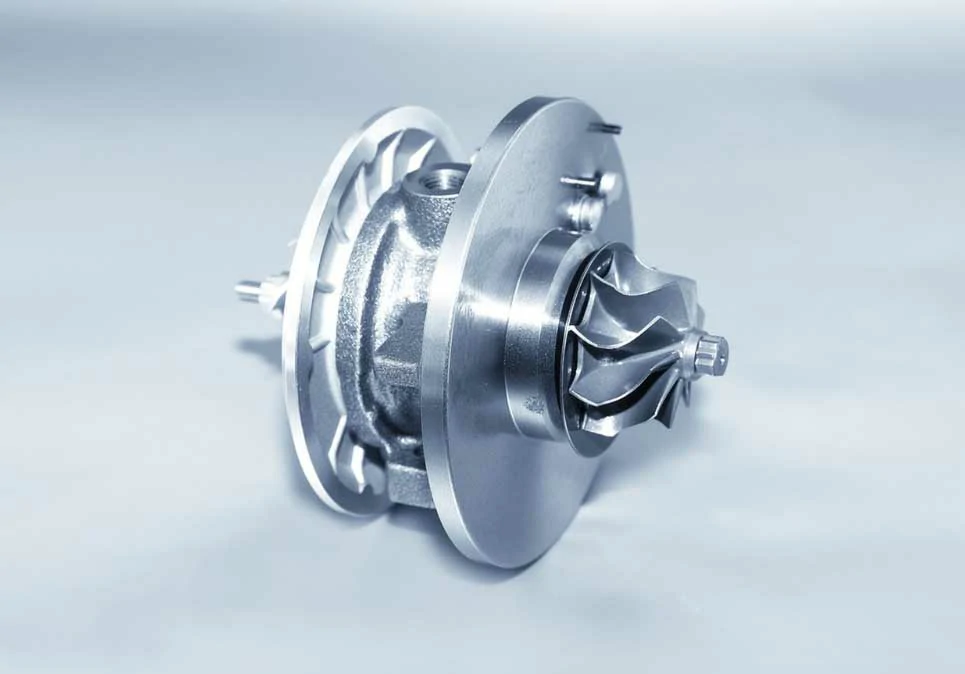
Surface Treatment | Characteristics | Applications | Color | Texture |
---|---|---|---|---|
Acid Etching | Removes oxide and contaminants, improves smoothness and purity | Cleansing and purifying the surface | Colorless or slight yellow | Smooth |
Polishing | Improves surface smoothness and appearance | Beautification and decoration | Bright or mirror-like shine | Smooth |
Passivation | Forms an oxide film, enhances corrosion resistance | Enhancing corrosion resistance | Black, blue, gold, etc. | Smooth |
Nitriding | Increases hardness, wear resistance, and corrosion resistance | Improving surface hardness and wear resistance | Black | Smooth |
Anodizing | Forms a hard, wear-resistant, and corrosion-resistant oxide film | Providing surface protection layer | Stainless steel, black, gold, etc. | Smooth or slightly rough |
Coating | Provides additional functional and decorative coatings | Enhancing friction performance, wear resistance, corrosion resistance, etc. | Varies depending on the type of coating | Smooth or varies depending on the type of coating |
Titanium tool maintenance and maintenance
When using titanium tools, proper maintenance and maintenance can extend the service life of the tool and improve machining efficiency. The following are some suggestions for the maintenance and maintenance of titanium tools:
A. Anti-rust treatment
Titanium cutters are prone to rust, so you need to treat them with rust prevention and keep them dry and clean in daily use.
B. Clean regularly
Regular cleaning ensures that the surface of the titanium tool remains smooth and bright, as well as the removal of debris, dust and other materials attached to the tool.
C. Tool care lubrication
During online CNC machining, tool surfaces need to be kept clean and lubricated. Therefore, you need to use special care lubricants for titanium tools to ensure that the cutting surface is smooth and does not rust.
custom CNC machining titanium parts near me
Are you looking for a titanium CNC manufacturer that can provide you with services from design to rapid prototyping? Then you have come to the right place, at Longsheng Technology, we provide services from design to rapid prototyping to support the development and manufacture of titanium products, including custom parts, high volume production and rapid prototyping.
Contact us and let us help you with your CNC machining needs!
Mobile:+86 185 6675 9667(Gloria Wu)
E-Mail:gloria.wu@longshengmfg.com