In the rapidly developing manufacturing industry, the CNC machine tool industry is facing unprecedented opportunities and challenges. As the market demand for high-efficiency customized parts continues to increase, the CNC machine tool industry must continue to innovate and improve its service capabilities. As an advanced CNC network solution, Direct CNC Net is gradually becoming an important promoter of customized parts services for the enhanced CNC machine tool industry. This article will prompt everyone to discuss how Direct CNC Net plays a key role in this field.
What is a Direct CNC Net?
Direct CNC Net are automated machine tools that are operated by a computer executing a preprogrammed sequence of control commands. Direct CNC Net are essentially the opposite of “old school” equipment, which is manually controlled with a handwheel or lever, or mechanically automated with only a cam. Today’s modernDirect CNC Net understand and run using a CNC machining language, known as G-code, which tells them precise production measurements such as feed rates, speeds, positions and coordination.
Today, CNC systems design and machine parts to a high degree of automation, unlike the old, dangerous factory machines of the past. The mechanical dimensions of the part are defined using computer-aided design (CAD) software and then translated into manufacturing instructions using computer-aided manufacturing (CAM) software. Therefore, it is important to have CNC machinists and programmers who are knowledgeable in the industry to operate this high-tech machine.

Direct CNC Net and its impact on CNC machining?
※Improve production efficiency
Direct CNC Net may reduce manual intervention and improve the automation of the production process through automation and intelligent technology, thereby shortening the production cycle and improving production efficiency. Monitor the operating status and production progress of CNC machine tools in real time through the network, realize intelligent scheduling and optimization of production tasks, and avoid production bottlenecks and waste.
※Improve processing accuracy
Direct CNC Net may provide higher-precision control algorithms and parameter settings to ensure that CNC machine tools can accurately execute predetermined procedures during processing and improve processing accuracy. By collecting and analyzing machining data in real time, Direct CNC Net can promptly discover and correct deviations in the machining process to ensure the accuracy and consistency of machining results.
※Enhance flexibility
Direct CNC Net may support rapid adjustment of production plans and processing procedures to adapt to rapid changes in customer needs and improve market response speed. Through reprogramming and software updates, CNC machine tools can easily switch from one part to another to support diverse production needs.
※Reduce production costs
Automated and intelligent production reduce reliance on labor and lower labor costs. Optimize material utilization plans through data analysis, reduce material waste, and reduce material costs.
※Improve safety and reliability
Direct CNC Net may have real-time monitoring and early warning functions, which can promptly discover and deal with potential safety hazards and faults, and improve the safety and reliability of the production process. Provide data encryption, access control and other security measures to ensure the security of production data and equipment.
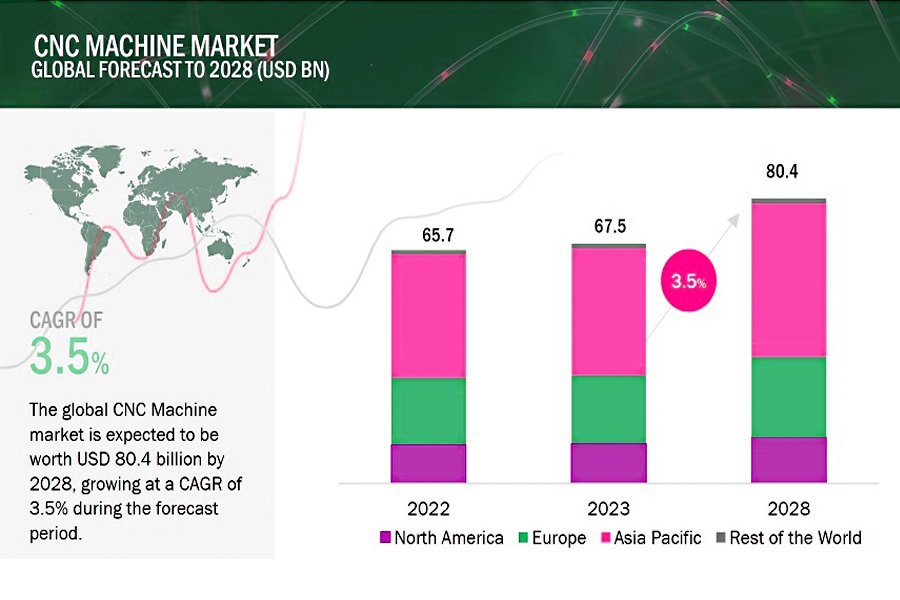
Advantages And Disadvantages Of Direct CNC Net
Advantages
- Improve system reliability: Direct implementation of CNC machine tools can reduce the involvement of paper tape readers in the processing process, thereby reducing the risk of system failures. In the DNC computer system, the machine tool is directly controlled, reducing the intermediate gap and improving the stability and reliability of the entire system.
- Optimize resource allocation and utilization: One computer can control multiple CNC machine tools at the same time, maximizing production efficiency. Especially suitable for small and medium-sized batch production. The CNC network is directly connected to the machine tool, which can realize remote operation of programming, debugging and maintenance, saving technicians time traveling to the machine tool and improving work efficiency.
- Improve the flexibility of the system: Direct network connection of CNC machine tools can increase or decrease the number of consoles at any time to meet demand, making the system more flexible and adaptable to diversified production scales. Multiple parts can be processed simultaneously or separately during processing, improving system response speed and flexibility.
- Achieve prescient maintenance: integrated data acquisition system, direct CNC network real-time monitoring of machine tool operating status and online monitoring data, realizing predictive maintenance, helping to detect problems in time, reduce time, and avoid accidents.
Disadvantages
- High technical complexity: CNC machine tools are directly connected to the CNC network, which requires knowledge in multiple professional fields such as computer networks and CNC technology. The technical requirements are very high, and operating and maintenance personnel need to have high-level professional skills.
- The initial investment is high: To establish a CNC machine tool network, funds need to be invested to purchase computers, network equipment, CNC equipment and software systems, which may not be easy for small and medium-sized enterprises to afford.
- Network security risks: With the continuous development of network technology, network security issues have become increasingly prominent. As a network-based system, the CNC machine tool direct sales network also faces network security risks. Once the system is attacked or infected with a virus, it may lead to serious consequences such as data loss and machine tool loss of control.
- Difficulty in maintenance: The direct CNC network of CNC machine tools is composed of multiple components. Each component is interrelated and affects each other, which increases the difficulty and complexity of system maintenance. Once a component fails, it may affect the normal operation of the entire system.

HOW Direct CNC Net Enhances Custom Part Services in the CNC Machine Industry?
Improve production efficiency and flexibility
direct CNC net allows one computer to control multiple CNC machine tools at the same time to achieve centralized management and scheduling, which greatly improves production efficiency and flexibility. For custom parts services, this flexibility means faster responses to customer needs and shorter production cycles. The direct CNC net supports remote programming and program transmission, allowing CNC programs to be quickly transmitted from the design department to the machine tool, reducing time delays during program transmission and speeding up the production process.
Promote technological innovation and industrial upgrading
The direct CNC net is an integration of advanced technologies such as CNC technology, computer technology, and network technology. Its application promotes technological innovation and industrial upgrading in the CNC machine tool industry. In customized parts services, this kind of technological innovation helps enhance the competitiveness and market position of enterprises. With the development of intelligence and automation technology, the direct CNC net is constantly being upgraded and improved. The future direct CNC net will pay more attention to the application of intelligent and automated control technology to provide more efficient and accurate solutions for customized parts services.
Simplify operating procedures and reduce maintenance costs
The direct CNC net simplifies the CNC programming and debugging process and reduces the technical requirements for operators. In custom parts service, this helps reduce technician training costs and time and improves overall productivity. The direct CNC net supports remote maintenance functions, allowing technicians to remotely solve machine tool faults and problems, reducing maintenance costs and time. This is particularly important for the CNC machine tool industry that provides customized parts services, as it can ensure the continued stable operation of machine tools and timely response to customer needs.

What are the core functions of Direct CNC Net?
Core Functions | Describe |
Network connection and management | realize network connection between CNC machine tools, as well as data exchange and collaborative work between machine tools and upper-level management systems |
Real-time monitoring and diagnosis | Through sensors and data analysis technology, the operating status and processing quality of machine tools can be monitored in real time, and potential problems can be discovered and diagnosed in a timely manner. |
Intelligent control and optimization | Use advanced control algorithms and artificial intelligence technology to intelligently control and optimize the processing process of machine tools to improve processing accuracy and efficiency. |
Remote operation and maintenance | Supports remote programming, debugging and maintenance functions, reducing on-site operation costs and improving response speed. |
Data analysis and decision support | Conduct in-depth mining and analysis of production data to provide decision support for enterprise production management. |
Which industries or fields are likely to be the first to use Direct CNC Net?
- Precision manufacturing and machining: By using Direct CNC Net for precision manufacturing and machining, we can further optimize the accuracy of machining and improve the efficiency of production. With the advancement of technology, more and more precision parts, such as aircraft parts, automobiles, etc., need to be processed with high precision and efficiency, which makes CNC processing more important. In the mold manufacturing process, there are extremely high requirements for processing accuracy and efficiency. The use of CNC methods can effectively ensure the quality of mold manufacturing, while also greatly improving production efficiency. The precise control and real-time monitoring functions of Direct CNC Net play a positive role in improving the quality and efficiency of mold production.
- Aerospace: Parts have extremely high requirements on accuracy, reliability and durability. Direct CNC Net’s high-precision machining and intelligent control capabilities meet these requirements. The manufacturing of key components such as aerospace engines requires high-precision and complex machining processes. The application of Direct CNC Net will help improve manufacturing efficiency and product quality.
- Automobile industry:Since a large number of high-precision parts are required, the use of Direct CNC Net technology can significantly improve the manufacturing efficiency and precision of automotive parts, and also help reduce overall production costs. The automobile body is one of the important components of automobile products. It not only requires beautiful appearance, but also has high requirements for quality. In the process of manufacturing and assembling automobile bodies, Direct CNC Net helps achieve automation and intelligent control, thereby improving the efficiency of the entire production line.
- Medical device manufacturing:In the field of medical device manufacturing, there are extremely high requirements for manufacturing accuracy and reliability. The application of CNC technology can significantly improve the manufacturing accuracy and product quality of medical devices. Especially in the manufacturing of artificial organs and implants, the precision processing capabilities of CNC ensure the safety and effectiveness of products.
- Electronic products:Many components in electronic products require high-precision processing. The application of Direct CNC Net can meet this demand and improve the production efficiency and product quality of electronic components.

Summary
Direct CNC Net has significantly enhanced the custom parts service capabilities of the CNC machine tool industry by improving machining accuracy and flexibility, optimizing design and programming processes, realizing intelligent production and management, promoting resource sharing and collaborative innovation, and improving customer service experience. With the continuous advancement of technology and changing market demands, Direct CNC Net will play a more important role in the future and promote the development of the CNC machine tool industry to a higher level.Visit our Instant Quote Engine to get a free, no-obligation quote in minutes.
Disclaimer
The content appearing on this webpage is for informational purposes only. LongSheng makes no representation or warranty of any kind, be it expressed or implied, as to the accuracy, completeness, or validity of the information. Any performance parameters, geometric tolerances, specific design features, quality and types of materials, or processes should not be inferred to represent what will be delivered by third-party suppliers or manufacturers through LongSheng’s network. Buyers seeking quotes for parts are responsible for defining the specific requirements for those parts. Please contact to our for more information.
Team LongSheng
This article was written by various LongSheng contributors. LongSheng is a leading resource on manufacturing with CNC machining, sheet metal fabrication, 3D printing, injection molding,metal stamping and more.
FAQs
How does Direct CNC Net improve the machining accuracy of custom parts?
Direct CNC Net uses a high-speed and stable data transmission protocol to ensure that processing instructions are accurately transmitted to the machine tool control system and reduce errors in the data transmission process. Integrate advanced control algorithms to accurately control the motion trajectory, speed, acceleration, etc. of the machine tool to ensure stability and consistency during the machining process. The operating status and processing quality of the machine tool are monitored in real time through sensors, and the processing parameters are automatically adjusted based on the monitoring results to ensure that the processing accuracy of the parts meets the requirements.
How does Direct CNC Net realize intelligent production and management of customized parts?
Seamlessly connects with the production management system to realize automatic scheduling and scheduling of production plans and optimize the allocation of production resources. Monitor the operating status and processing quality of machine tools in real time through Internet of Things technology, and provide timely warnings and take measures when abnormalities are discovered. Use big data technology to conduct in-depth mining and analysis of production data, discover bottlenecks and problem points in the production process, propose improvement measures, and continuously optimize the production process.
What are the main functions of Direct CNC Net?
Realize network connections between CNC machine tools, as well as data exchange and collaborative work between machine tools and upper-level management systems.
Through sensors and data analysis technology, the operating status and processing quality of machine tools can be monitored in real time, and potential problems can be discovered and diagnosed in a timely manner. Advanced control algorithms and artificial intelligence technology are used to intelligently control and optimize the processing process of machine tools to improve processing accuracy and efficiency. Support remote programming, debugging and maintenance functions, reduce on-site operation costs and improve response speed. Conduct in-depth mining and analysis of production data to provide decision-making support for enterprise production management.
How to choose the Direct CNC Net solution suitable for your business?
Identify your company’s production needs, goals, and pain points so you can choose a solution that addresses them. Evaluate the technical strength, R&D capabilities and after-sales service level of the solution provider to ensure the stability and reliability of the solution. Consider the solution’s compatibility with existing equipment as well as future scalability so that it can be easily upgraded and expanded if needed. Comprehensively consider the initial investment, operating costs and long-term benefits of the solution, and choose a cost-effective solution.
Pingback: What to Expect in a CNC Machining Quote?
Pingback: How to Choose the Best CNC Machining Provider: A Guide to Evaluating Top Companies
I am no longer sure the place you are getting your info, however good topic. I must spend a while learning much more or figuring out more. Thank you for great information I was in search of this information for my mission.
Thank you for your support, each article is written by ourselves, we will update the article every day, you can subscription LS, wish you a happy day.
I got what you mean ,saved to my bookmarks, very nice internet site.
Thank you for your attention, please subscribe to us and share valuable information with your friends in need, have any needs, please send us an inquiry.