Injection molding is a widely used manufacturing process across different industries. It is particularly popular in the production of plastic parts for various applications such as toys, automotive components, and consumer electronics. This process involves melting plastic pellets and injecting them into a mold to create a desired shape. In this article, we will explain the steps involved in the injection molding process and how it works.
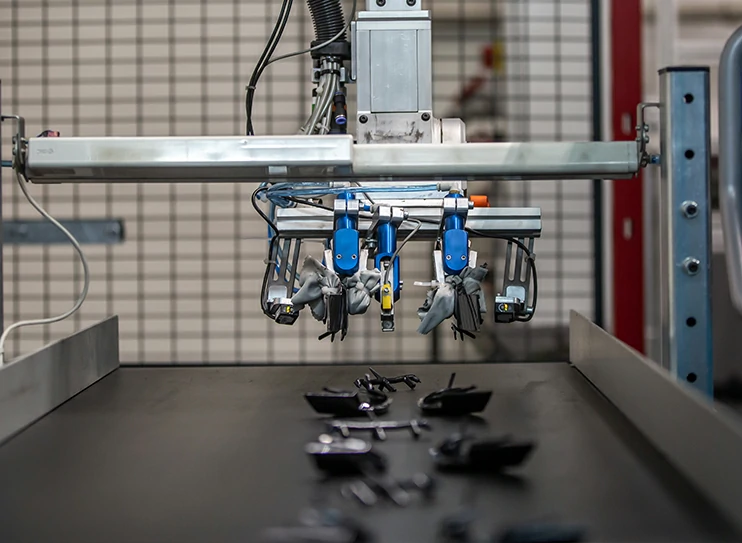
Injection molding process
Injection molding typically involves four stages: clamping, injection, cooling, and ejection. We will explain each of these stages in more detail.
Clamping
This stage involves securing the two halves of the mold, which is typically made of steel, in place. The mold is designed to have a cavity, which is the exact shape of the final product. The mold also has channels or runners that allow the plastic to flow into the cavity. During the clamping stage, the mold is securely closed, and the plastic is injected into the cavity.
Injection
Once the mold is securely closed, plastic pellets are loaded into the hopper of the injection molding machine. The pellets are heated to a liquid state and then forced into the mold cavity under high pressure. The pressure and temperature used in the injection stage depend on the type of plastic being used and the complexity of the part being produced.
Cooling
After the plastic is injected into the mold cavity, it needs time to cool and solidify. During the cooling stage, the mold remains closed to maintain the shape of the part. The cooling time depends on the thickness and complexity of the part being produced.
Ejection
Once the plastic has cooled and solidified, the mold is opened, and the part is ejected from the cavity. The ejection stage involves using ejector pins to push the part out of the mold. The part is then inspected for quality and, if necessary, further processing such as trimming or painting may be done.

How Injection Molding Works
Injection molding is an efficient and cost-effective manufacturing process. It allows for the rapid production of high-quality, complex parts with tight tolerances. The process is highly customizable, allowing for the production of parts in a wide variety of sizes and shapes. It is also environmentally friendly, as excess plastic can be recycled, and the energy required for the process can be reduced through the use of efficient machines.
As a manufacturer, using injection molding can help you produce parts with reduced lead times and lower costs. This is especially important in today’s competitive business landscape, where speed and cost-effectiveness are significant factors. The process can also help you to create parts with fewer defects, improving the quality of your products and your customer satisfaction.
Conclusion
Injection molding is a highly versatile and efficient manufacturing process that is widely used in the production of plastic parts. It is a process that involves several stages, including clamping, injection, cooling, and ejection. Using injection molding can help manufacturers to produce high-quality parts at a lower cost and reduced lead time. With proper maintenance and optimization, injection molding can be an excellent choice for your manufacturing needs.