In the field of metal processing, aluminum blocks inherit good thermal conductivity, plasticity and relatively light weight and are widely evaluated in aerospace, automobile manufacturing, electronic equipment and other industries. For milling processing, choosing the right aluminum block is very important, as it directly affects the processing efficiency, finished product quality and production cost. In this article, Longsheng will help everyone explore the secrets of choosing the perfect aluminum block, and help us not be confused when choosing aluminum blocks.
What are the advantages of milling aluminum blocks?
- High processing precision:Milling processing can achieve higher precision requirements and meet the needs of precision manufacturing. Micron-level processing accuracy can be achieved through high-precision machine tools and CNC systems.
- High processing efficiency:Milling processing can realize high-speed, continuous cutting process and significantly improve production efficiency. Especially in mass production, milling can significantly shorten the production cycle.
- High processing quality:During milling, the tool maintains good contact with the surface of the aluminum block, which can avoid problems such as surface pinch deformation, bubbles, and subsurface defects, and improve processing quality. At the same time, by selecting appropriate cutting parameters and tools, a smooth and flat machined surface can be obtained.
- High processing flexibility:Milling can process parts and components of various complex shapes to meet diverse processing needs. By adjusting the tool path and cutting parameters, machining of different shapes and sizes can be achieved.
- Good heat dissipation performance:Aluminum alloy has good thermal conductivity, and the heat generated during the milling process can be quickly dissipated, helping to maintain the cutting performance of the tool and the processing quality of the workpiece.
- Enhance workpiece strength:A suitable aluminum block milling process can greatly improve the surface hardness of aluminum alloy workpieces and enhance the strength and corrosion resistance of the workpieces.
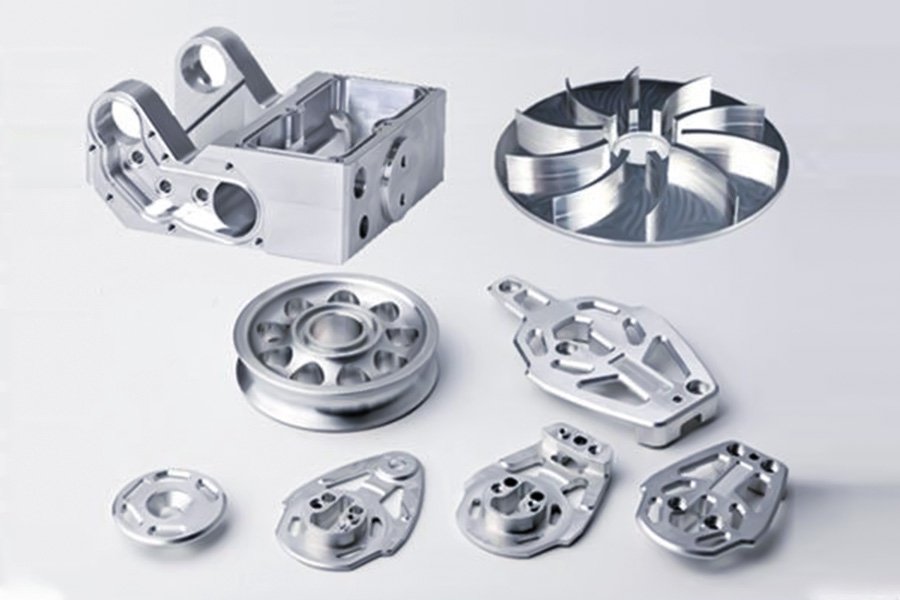
What are the disadvantages of milling aluminum blocks?
- Processing adhesion problem: Aluminum alloys are prone to adhesion during the milling process, that is, the friction at the cutting interface between the tool and the workpiece is large and the tool is prone to sticking. This will affect processing efficiency and processing accuracy, and appropriate measures need to be taken to reduce adhesion.
- Risk of machining deformation: Aluminum alloy has relatively low rigidity and is easily deformed by cutting forces during milling.
- High equipment cost: Milling processing requires the use of high-precision machine tools and CNC systems, and the cost of these equipment is high.
- Tools wear quickly: During the cutting process of aluminum alloys, tools are susceptible to wear. Especially when inappropriate tools or cutting parameters are used, the tools will wear faster.
HOW to Choose the Perfect Aluminum Block for Milling?
▲Clarify application requirements
Understand the environment in which the aluminum block will be used, such as high temperature, high humidity, strong corrosion, etc., so that you can choose an aluminum block with corresponding resistance.According to the mechanical requirements such as pressure, tension, impact force, etc., the appropriate strength and hardness aluminum block is selected. Identify the required size and shape of the aluminum block to ensure that the selected aluminum block can meet the processing or assembly requirements.
▲Evaluate the aluminum block material
Different aluminum alloys have different chemical compositions and physical properties. Choose the appropriate alloy type according to actual needs.High-purity aluminum blocks generally have better processing properties and a more uniform organizational structure. Pay attention to check the impurity content in the aluminum block to ensure that it is within the acceptable range.
▲Consider processing performance
Choosing an aluminum block that is easy to cut can reduce processing difficulty and cost. Some alloys such as aluminum-silicon alloys generally have better machinability. If welding is required, aluminum blocks with good weldability should be selected. Certain alloys such as aluminum-magnesium alloys may produce cracks or pores during welding, so special attention is required. Consider whether the aluminum block requires surface treatment (such as anodizing, spraying, etc.) after processing.
▲Evaluate cost-effectiveness
The prices of different types and specifications of aluminum blocks vary greatly. On the premise of meeting performance requirements, choosing cost-effective aluminum blocks can reduce material costs. Consider the impact of the processing difficulty and processing time of the aluminum block on the overall cost. Easy-to-machine aluminum blocks can reduce processing costs and time costs.
▲Suppliers and Quality Assurance
Make sure the aluminum block you choose comes from a qualified and reputable supplier. Regular suppliers can usually provide stable quality and complete after-sales service. Suppliers are required to provide quality certification documents for aluminum blocks (such as material certificates, test reports, etc.) to verify whether their material and performance meet the requirements. Before bulk purchasing, suppliers can be asked to provide samples for testing and verification. Evaluate the processing performance and quality stability of aluminum blocks through actual tests.
What are the processes for milling aluminum blocks?
Milling is an excellent method for producing precision and complex aluminum parts. Below is a breakdown of the main steps in aluminum processing.
Processes | Describe |
Material Selection | Different aluminum alloys have different properties that make them suitable for specific applications. Choose an aluminum alloy that meets the processing, strength, and weight requirements of your project. |
Design | Make a 3D CAD model of the part. This model will be used to create toolpaths for the milling machine. |
CAM Software | To create tool paths from a 3D model, use CAM (Computer Aided Manufacturing) software. The CAM software will use the geometry of the model to define the motion of the milling machine’s cutting tool. |
Machine Setup | Use a clamp or vise to securely hold the aluminum billet to the table of your milling machine. |
Tool Selection | Choose the right milling cutter or end mill for your project. Carbide end mills are commonly used for aluminum machining because of their durability and ability to handle higher cutting speeds. |
Feeds and Speeds | For optimal cutting performance, adjust feed rate (material movement) and spindle speed (cutting tool rotation). Refer to the manufacturer’s recommendations for your specific aluminum alloy and cutting tool. |
Machining Process | The CNC machine will follow a programmed tool path to remove material from the aluminum block to produce the desired part. Depending on the complexity of the part, multiple passes using different cutting tools may be required. |
Coolant | aluminum blocks machining is best done with a coolant such as flood coolant or mist coolant. It lubricates cutting tools, prevents chip welding , and improves surface finish. |
Deburring | After processing, parts may have sharp edges or burrs. To remove these burrs safely and cleanly, use a deburring tool or a hand file. |
Sanding/Polishing | For a smoother surface, hand sand or polish aluminum parts to achieve your desired aesthetic. |
What aluminum blocks are commonly used for milling?
1.Aluminum 6061-T6
6061-T6 is the most popular aluminum alloy and is used by most rapid manufacturing companies as the standard grade for CNC machining. 6061-T6 is an excellent general-purpose material that is easy to CNC machine and can be processed with different heat treatments. Common applications include bicycle frames, valves, automotive parts, and more.
2.Aluminum 7075-T6
7075-T6 is known for its excellent strength-to-weight ratio and its hardness can rival even some softer steels. 7075-T6 is widely used in the aerospace and military defense industries. Common applications include aircraft parts, tanks, high-performance bicycles, etc. 7075-T6 aluminum is significantly more expensive than 6061 T6.
3.Aluminum 2024-T4
2024-T4 aluminum is a medium to high strength alloy with good fatigue resistance and fracture toughness. 2024-T4 aluminum is not as strong as 7075-T6, but is still suitable for aerospace applications. Common applications include aircraft fuselages, transport vehicle components and wings. 2024-T4 has poor corrosion resistance and is highly sensitive to thermal shock.
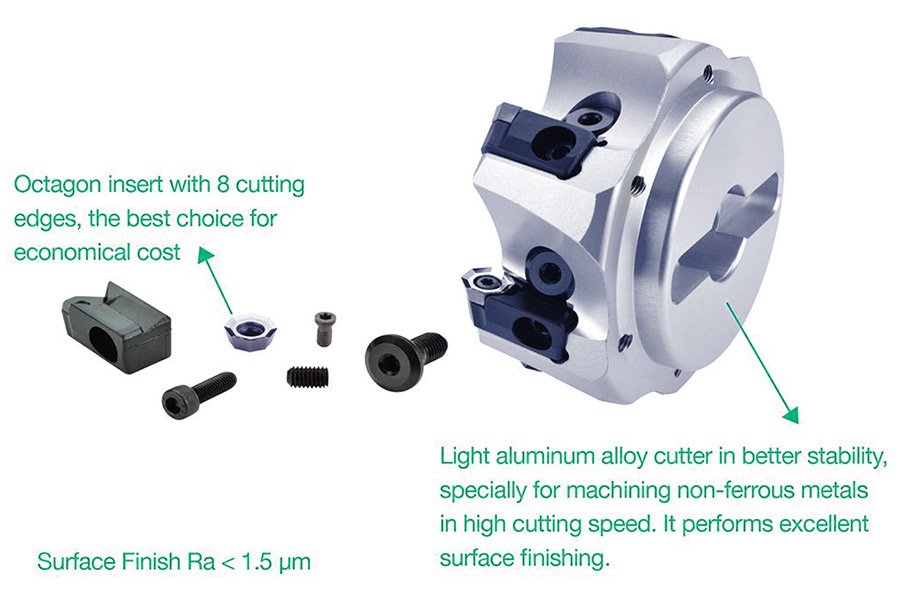
4.Aluminum MIC 6
MIC 6 aluminum has been developed specifically for the production of stable, highly resistant sheets with excellent stress relief properties, outstanding precision and high machinability. MIC 6 aluminum is also non-polluting and non-porous and is commonly used in electronics. The downside is that MIC 6 threads are not as strong as 6061 threads.
5.6082 aluminum
6082 aluminum has similar properties to 6061 aluminum but is stronger, the strongest of all 6000 series alloys, and offers excellent corrosion resistance. 6082 aluminum is well suited to the construction industry and is used in many bridges, towers and trusses. It is worth noting that 6082 aluminum is difficult to manufacture thin-walled parts.
6.Aluminum 5083-T6
5083-T6 aluminum is known for its excellent performance in extreme conditions. This aluminum grade is extremely corrosion-resistant in marine and chemical environments. The 5083 is not suitable for use above 65°C. 5083 has a wide range of applications in the cryogenic market. It is also ideal for marine applications, chemical applications, transportation vehicle components, pressure equipment and more.
What are the commonly used milling tools for aluminum block milling?
Tool Type | Specification | Size | Cutting Speed (m/min) | Feed Speed (mm/min) | Cutting Depth (mm/tooth) | Cutting Width (mm) |
---|---|---|---|---|---|---|
Solid Carbide End Mill | 2 Flutes, Straight Shank | Φ6×Φ6×50×100 | 200-400 | 800-1500 | 0.05-0.15 | 1-3 |
PCD/PCBN End Mill | 4 Flutes, Straight Shank | Φ8×Φ8×60×120 | 300-600 | 1000-2000 | 0.05-0.25 | 1-5 |
High-Speed Steel End Mill | 2 Flutes, Straight Shank | Φ10×Φ10×75×150 | 60-150 | 200-500 | 0.05-0.2 | 1-3 |
How to choose aluminum milling tools?
Choosing the right tool for milling aluminum is critical to achieving accuracy and efficiency. Several factors should be considered when choosing a tool:
- Material Compatibility: Make sure your tools are specifically designed for aluminum processing. Using tools designed for other materials may result in premature wear and reduced performance.
- Tool materials: Carbide and high-speed steel are common tool materials for milling aluminum. Carbide cutting tools are favored for their hardness and wear resistance, making them suitable for high-speed milling.
- Tool geometry: Pay attention to the geometry of the tool, including the number of flutes, flute design and rake angle. Proper geometry affects chip evacuation, surface finish and tool life.
- Cutting speed and feed rate: Match the cutting speed and feed rate of the tool to the aluminum alloy being processed. Knife manufacturers provide charts and recommendations to guide your choice.
- Tool size: Choose the tool diameter that suits your job. Larger tools can remove material quickly but may require more spindle power, while smaller tools are better for delicate jobs.
- Coatings: Consider using coated tools to reduce friction and heat build-up, thereby extending tool life. Coated tools also aid in chip evacuation, especially during high-speed machining.
- Tool stiffness: Ensure that the tool holder and machine tool spindle can withstand the selected tool size and cutting force. Stiffness prevents vibration and tool deflection, ensuring accuracy.
- Coolant or lubrication: Depending on the application, decide whether to use coolant or lubricant. These help dissipate heat and extend tool life. There are several methods available including flood cooling and air/oil mist.
- Tool life expectancy: Estimate the tool life required for your application. Longer tool life may justify the use of higher quality or coated tools.
- Tool Maintenance: Regularly inspect and maintain your tools to ensure consistent results. Replace tools as needed to maintain optimal performance.
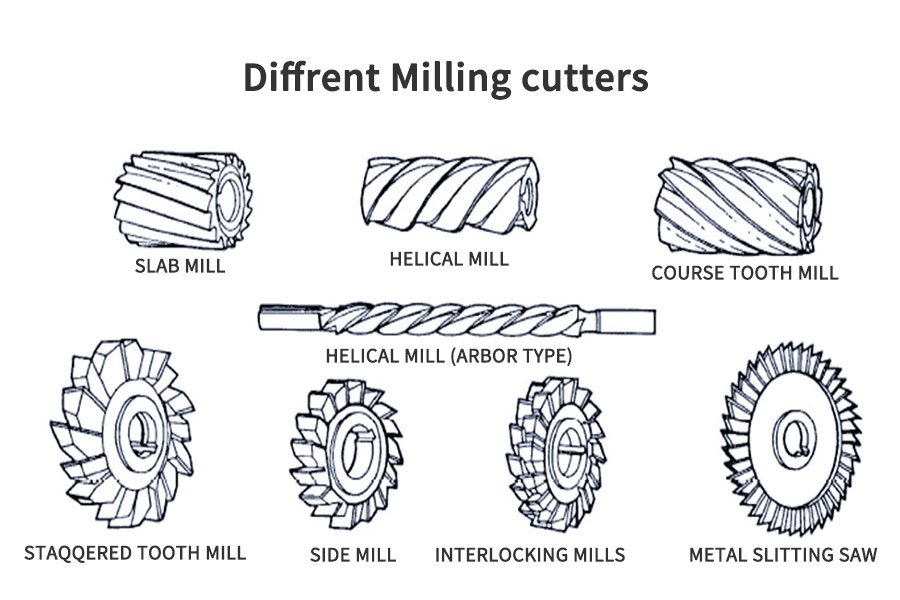
What are the factors that affect the feed and speed of aluminum block milling?
★Aluminum Alloys: Various aluminum alloys have unique properties that impact the milling process. Therefore, appropriate process parameters should be selected during actual processing to obtain the best surface quality. Taking 6061-T6 aluminum as an example, its tensile strength exceeds that of 2024-T3 aluminum, which may have an impact on recommended cutting rates and feed rates.
★Cutting tool geometry: This geometry affects chip generation and heat generation during milling. In order to improve productivity and reduce energy consumption, when processing aluminum alloys, reasonable cutting amounts should be selected as much as possible, that is, parameters such as feed amount, feed amount per tooth, and power per revolution/minute should be appropriate. This situation has an indirect impact on the recommended speeds and feed rates for aluminum milling.
★Cutting tool coatings: These coatings help extend tool life and reduce friction, allowing for higher cutting speeds and feeds. Aluminum is a good metal matrix material. When processing aluminum alloys, ceramic coatings such as alumina or silicon oxide are usually used as pretreatment methods. However, different coatings are recommended for different materials, so choosing a coating suitable for the aluminum milling process is particularly critical.
★Depth of cut: The amount of material removed by a cutting tool during a single cut. When the cutting amount is greater than a certain range, the cutting depth has little effect on the quality of the workpiece. The deeper the cut, the more efficient the material removal, but this may also lead to the risk of tool deflection and reduced surface finish.
★Coolant/Lubricant: The use of coolant or lubricant reduces heat generation during milling, thereby helping to avoid tool wear and improve surface smoothness. Therefore, it is important to select the appropriate coolant/lubricant when machining. However, the type of coolant and lubricant and how they are applied will have an impact on the recommended flow and feed rates.
★Machine Stiffness: The stiffness of a milling machine affects recommended speeds and feeds, as stiffer machines can handle higher speeds and feeds without sacrificing accuracy.
How to feed and speed aluminum block milling?
※Determine the Proper Cutting Speed: CNC milling speeds for aluminum typically range from 400 to 1200 SFM (surface feet per minute), depending on the type of aluminum alloy and the tool used. Cutting speed should be set within this range to ensure efficient material removal while avoiding excessive tool wear.
※Choose the right tool: For aluminum milling, it is recommended to use high-speed steel or carbide tools as they are designed to withstand high cutting speeds and reduce tool wear.
※Choose the right feed rate: The feed rate is the distance the tool travels in one revolution of the spindle. Typically, feed rates for aluminum milling range from 0.001 to 0.02 inches per tooth, depending on tool diameter, tool geometry, and cutting conditions.
※Optimize depth of cut: Depth of cut is the amount of material removed in one cut. For aluminum, the recommended depth of cut typically ranges from 0.05 to 0.25 inches, depending on the stiffness of the machine, the cutting tool, and the specific application.
※Use coolant: When milling aluminum, cooling is essential to prevent chip buildup and keep the tool cool, extending its life. Use a water-soluble cutting fluid designed for non-ferrous materials.
※Experiment and adjust the parameters: After selecting the initial settings, adjust the parameters based on the capabilities of the machine and the specific aluminum material used. Be sure to monitor tool wear and surface finish to ensure parameters are producing the desired results.
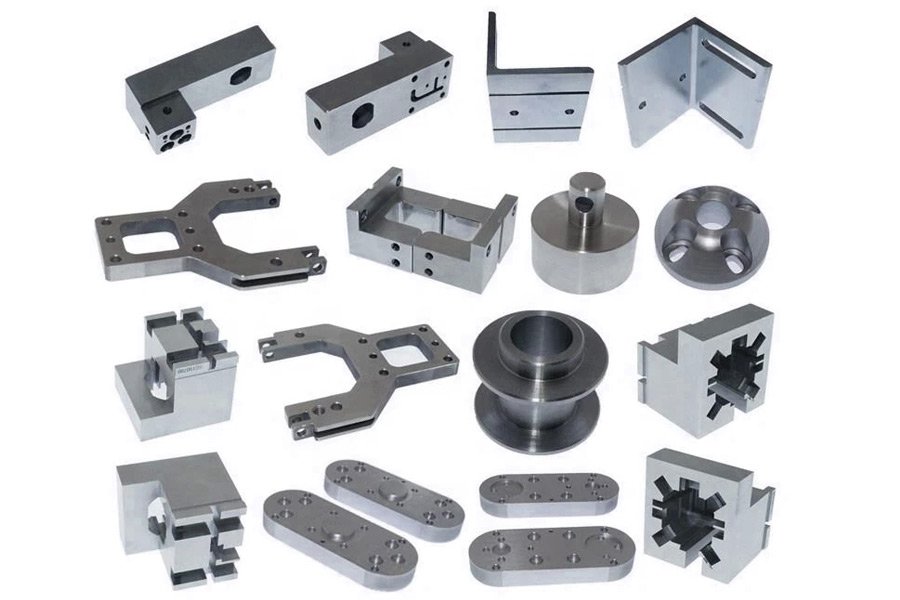
What are the application fields of aluminum block milling?
- Aerospace: Aluminum block milling plays an important role in the aerospace field and is used to manufacture various parts and structural parts for aircraft, rockets and other aircraft.
- Automobile manufacturing: In automobile manufacturing, aluminum block milling is widely used in the manufacture of engines, bodies, chassis and other components, helping to reduce vehicle weight, improve fuel economy and reduce emissions.
- Mold Making: Mold making is another important application area for aluminum block milling. Through milling processing, molds with high precision and high wear resistance can be manufactured to meet the production needs of various industrial products.
- Electronics: In electronics manufacturing, aluminum block milling also plays an important role. For example, it is used to manufacture mobile phone casings, tablet back covers and other components to improve the aesthetics and durability of the product.
What are the tips for milling aluminum blocks?
Reasonable selection of tool materials
The material of the tool has an important impact on cutting force and cutting heat. Tool materials with good wear resistance and high thermal stability should be selected, such as carbide or coated tools, to meet the cutting needs of aluminum.
Optimize the tool geometric parameters
choose a larger rake angle to grind a sharp edge, reduce cutting deformation, and reduce cutting force and cutting temperature. During rough milling, the relief angle should be smaller to improve heat dissipation; during fine milling, the relief angle should be larger to reduce the friction between the flank surface and the machined surface and reduce elastic deformation. In order to make milling smooth and reduce milling force, the helix angle should be as large as possible. Properly reducing the main deflection angle can improve heat dissipation conditions and reduce the average temperature of the processing area.
Improve the tool structure
reduce the number of milling cutter teeth and increase the chip space to adapt to the characteristics of large cutting deformation in aluminum processing.Precision grinding of cutter teeth reduces the roughness value of the cutting edge to reduce cutting heat and cutting deformation. Strictly control the wear standards of cutting tools to ensure that the cutting tools work in good condition and avoid the generation of built-up edge and increased cutting temperature.
Cutting parameter adjustment
Select the appropriate cutting speed according to the hardness of the aluminum material and the performance of the cutting tool to ensure processing efficiency and processing quality. Adjust the feed speed to control cutting load and cutting heat to avoid excessive cutting force or overheating caused by too fast speed.Choose the appropriate cutting depth according to the processing requirements and machine tool performance to avoid excessive cutting force and workpiece deformation caused by cutting too deep at one time.
Alternate milling
In order to avoid excessive heat accumulation, the alternating milling method can be used, that is, the tool is moved back and forth to exchange heat and cool down to ensure processing quality.
Layered multiple processing
For plate parts with multiple cavities, the method of layered multiple processing should be used. Each layer should be processed to all cavities at the same time, and then the next layer should be processed to make the parts uniform. Bear force and reduce deformation.
Symmetrical processing
For parts with large machining allowances, in order to have better heat dissipation conditions during processing and avoid heat concentration, symmetrical processing should be used.
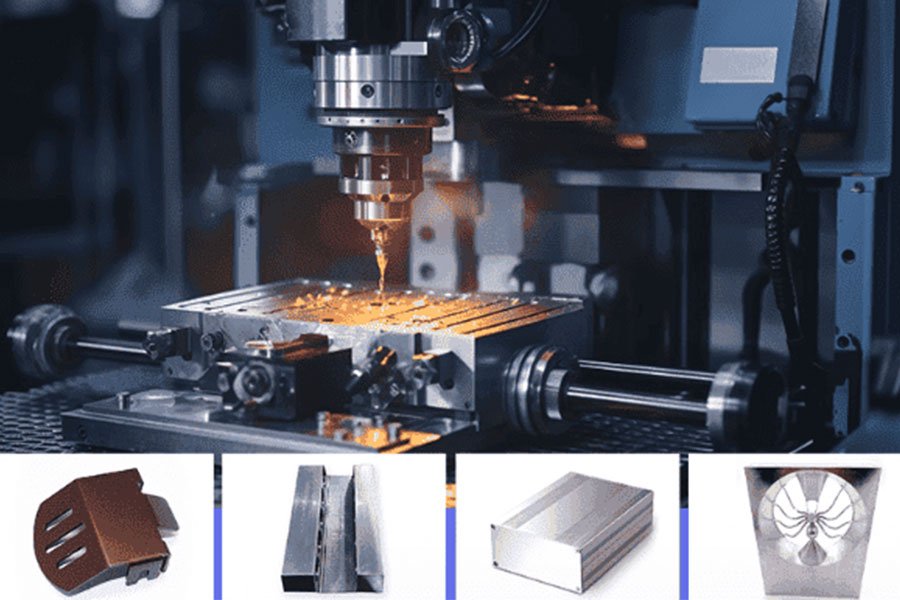
What factors should you consider when choosing an aluminum block milling manufacturer?
Choosing the right aluminum block milling manufacturer is critical to project success.
1.Ability performance
Production equipment: Check whether the manufacturer has advanced milling equipment, such as CNC end milling machines, etc. These equipment usually have the advantages of easy operation, stable performance, and high production efficiency.
Technical strength: Evaluate whether the manufacturer’s technical team has extensive experience in aluminum block milling, can solve complex processing problems, and has the ability to carry out technological innovation and improvement.
2.Quality control
√Inspection Procedures: Understand their quality control procedures. They should have a system of record to inspect parts at all stages of production to ensure dimensional accuracy, surface finish and overall quality meet your requirements.
√Quality Certifications: Look for manufacturers with relevant industry certifications (such as ISO 9001), which demonstrate their commitment to a quality management system.
3.Delivery time
√Productivity: Assess their current workload and ability to complete projects within your specified time frame. Consider the quantity of parts required and their typical production volumes.
√Communication and Transparency: Make sure they clearly communicate delivery times and possible delays. Transparent communication throughout the process helps manage expectations and avoid project bottlenecks.
4.Cost
√Competitive Quotes: Get quotes from multiple manufacturers. While cost is important, choose quality and features over the cheapest option.
√Cost Breakdown: Ask for a detailed cost breakdown including machining, materials, finishing and any additional charges. This transparency allows you to accurately compare quotes.
√Value for money: Consider the overall value proposition. If the required quality, capability or on-time delivery cannot be guaranteed, the most expensive quote may not always be the best option.
5.Credibility and reputation
√Industry reputation: Understand the reputation and status of the manufacturer in the industry, and choose a manufacturer with a good reputation and wide recognition.
√Customer reviews: Refer to other customers’ reviews and feedback to understand whether the manufacturer’s service quality and product quality meet customer needs.
Longsheng:Your best partner for milling
Longsheng is a company specializing in providing milling services, with many years of industry experience and advanced equipment. We are familiar with a variety of processing materials and processes and can provide customized solutions according to customer needs. Whether it is small batch production or large-scale production, we can guarantee product quality and delivery time to satisfy customers, please feel free to contact us. We look forward to assisting you and becoming your partner of choice.

Summary
Choosing the perfect aluminum block requires clarifying application requirements, evaluating the material of the aluminum block, considering processing performance, evaluating cost performance, suppliers and quality assurance and other factors. With the continuous development of metal processing technology, more new aluminum block materials will emerge in the future, providing more options for milling processing. At the same time, with the popularization of intelligent manufacturing and automation technology, aluminum block milling will become more efficient, precise and intelligent.Visit our Instant Quote Engine to get a free, no-obligation quote in minutes.
Disclaimer
The content appearing on this webpage is for informational purposes only. LongSheng makes no representation or warranty of any kind, be it expressed or implied, as to the accuracy, completeness, or validity of the information. Any performance parameters, geometric tolerances, specific design features, quality and types of materials, or processes should not be inferred to represent what will be delivered by third-party suppliers or manufacturers through LongSheng’s network. Buyers seeking quotes for parts are responsible for defining the specific requirements for those parts. Please contact to our for more information.
Team LongSheng
This article was written by various LongSheng contributors. LongSheng is a leading resource on manufacturing with CNC machining, sheet metal fabrication, 3D printing, injection molding,metal stamping and more.
FAQs
Why choose aluminum block milling?
Aluminum blocks have a series of advantages such as light weight, high strength, corrosion resistance, good thermal conductivity, and excellent machining performance. They are suitable for the needs of various industries. They have obvious advantages in lightweight product manufacturing, outdoor equipment, high temperature environments, etc., and are ideal s Choice.
What should I do if oxidation, stains, and scratches appear during the milling process of aluminum blocks?
Use professional cleaning agents and tools to clean the aluminum block to ensure the surface is completely clean. Use chemical oxidation, electrochemical oxidation or anodizing methods to improve the quality of the oxide layer on the surface of the aluminum block and enhance its corrosion resistance and decorative properties. Polishing treatment, using a polishing machine or manual grinding tools, to improve the finish and flatness of the aluminum surface.
What should we do if the aluminum block breaks, bends, deforms, etc. during the aluminum processing process?
Choose the appropriate aluminum block and select the model and specifications according to the processing technology and requirements. Carry out pre-processing treatment, such as heat treatment or cooling treatment, to improve the processing performance of the aluminum block. Optimize processing technology, refine operations, rationalize materials, and reduce operating errors. Post-processing treatments, such as annealing, internal stress elimination, surface polishing, etc., improve the stability and surface quality of the aluminum block.
What are the factors to consider when choosing aluminum blocks?
Select an aluminum block that meets the final part size requirements and allow for additional material for machining allowance. Alloys are selected based on the mechanical and physical properties required for the application. Factors such as strength, weldability, corrosion resistance, and weight should guide your choice. Evaluate the strength required for part functionality. High stress applications may require a stronger alloy such as 7075, while 6061 may be sufficient for less demanding uses. Some alloys are easier to machine than others, which affects tool wear and machining time. For parts that will be subject to high temperatures or need to dissipate heat, consider the thermal conductivity of the alloy. If finish or aesthetics is important, choose an alloy that can achieve the desired finish, such as anodizing or painting. Balance material costs with project budget. Higher performance alloys generally cost more.