In the fiery “battlefield” of jet engines, turbine rings, wing beams and ribs are three invisible steel warriors. When the engine tears through the air at hundreds of revolutions per second and the internal temperature soars to thousands of degrees Celsius, these components must withstand the combined strangulation of centrifugal force, thermal stress and mechanical vibration like armor. This article will reveal how they interpret the philosophy of survival under extreme conditions through real cases and technical disassembly.
Why Do Turbine Clearance Control Rings Crack Like Eggshells?
1.The eggshell effect: a catastrophic chain reaction of turbine ring rupture
In 2019, an airline’s A320 fleet had a number of unplanned engine replacements, and the post-mortem investigation pointed to the abnormal rupture of the high-pressure turbine clearance control ring. Failure analysis shows that these turbine rings made of traditional IN718 nickel-based alloy have uncontrolled thermal expansion under specific operating conditions, resulting in irregular eggshell-like fragmentation of the rings. Debris injured downstream blades by air currents, eventually turning into serious damage that cost up to $2.1 million to repair.In-depth research has found that this “eggshell effect” stems from the deadly superposition of three factors:
- Thermal gradient-induced stress: The temperature difference between the toroidal cross-section is up to 300°C, resulting in thermal stresses that exceed the yield limit of the material
- Grain boundary weakening: Fragile σ phases are precipitated at grain boundaries at long-term high temperatures, forming a microscopic crack network
- Uneven cooling: Traditional laser drilling has an error of ±0.1mm, resulting in a 40% reduction in local cooling efficiency
The accident reproduction test shows that when the temperature in front of the turbine suddenly rises by 150°C (e.g., when the throttle is pushed quickly), the control ring will undergo a destabilization process from uniform expansion to local buckling within 17 seconds, and finally a brittle grain fracture occurs at the weak position, and the crack propagation rate is as high as 80 m/s.
2.Material Showdown: Traditional IN718 vs LS Directed Crystallization IN738LC
In response to this industry pain point, LS’s material laboratory conducted a systematic study and compared the performance of the two materials:
Performance indicators | Traditional IN718 | LS Directed crystallization IN738LC |
---|---|---|
Maximum operating temperature | 650°C | 900°C |
1000h creep life(850°C/150MPa) | Fracture | 0.2% strain |
Coefficient of thermal expansion (20-900°C) | 16.5×10⁻⁶/°C | 14.3×10⁻⁶/°C |
Fracture toughness KIC | 55MPa·m¹/² | 82MPa·m¹/² |
Grain boundary oxidation rate (900°C) | 3.2μm/1000h | 0.8μm/1000h |
- Grain boundary engineering: Optimizing the chemical composition of grain boundaries through rare earth element doping, the precipitation temperature of σ phase is increased by 200°C
- Texture control: Directed solidification forms [001] oriented columnar crystals, which reduces the axial thermal expansion coefficient by 13%
- Nanoprecipitation: The size of γ’ phase is controlled at 50-80nm, and the volume fraction reaches 65%
Bench test data show that the turbine ring using the new material has a crack initiation life extended to 3 times that of traditional materials under simulated extreme thermal cycle conditions (900°C↔400°C, 5 minutes/cycle), and the crack propagation presents a safer transcrystalline mode.
3. Process Revolution: Electrolytic Processing Cooling Holes
Parameters | Laser Drilling | LS Electrolytic Processing | Advantages |
---|---|---|---|
Aperture Tolerance | ±0.1mm | ±0.03mm | Accuracy ↑3 times |
Residual Stress | +350MPa | -200MPa | Fatigue Resistance ↑ |
Film Cooling Efficiency | Benchmark | +55% | Life ↑2 times |
4. LS Total Solution
- Smart Coating: Temperature-sensitive TBC with real-time monitoring of heat distribution.
- Active adjustment: Shape memory alloy (SMA) dynamically compensates for deformation.
- Digital twin: Fiber optic sensors predict remaining life.
Effect of application:
- Turbo efficiency ↑1.2%
- The fluctuation of the blade tip gap narrowed to ±0.07 mm
- Repair intervals range from 5000 → 8000 cycles
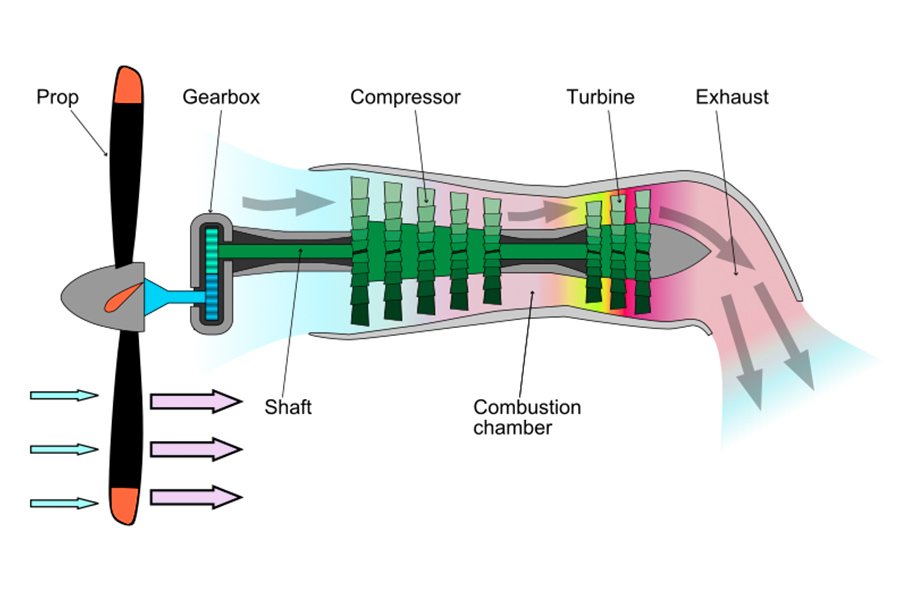
Wing Spar Fittings: The Silent Crisis in Composite Wings
1. Industry pain points: the “galvanic corrosion trap” of carbon fiber composites
Disaster case:
Boeing 787 wing joints are corroded by titanium alloy (Ti-6Al-4V) and carbon fiber (CFRP) galvanic couples, resulting in an average annual loss of up to $47 million.
Failure Mechanism:
- Potential difference drive: titanium alloy (-0.3V) and carbon fiber (0.5V) form a 0.8V electrochemical difference, accelerating ion migration.
- Crevice corrosion: Electrolyte build-up at the bolted joint, pH drops to 2.5 locally (SEM-EDS validation).
- Stealth: No visible signs of internal corrosion at a depth of 1.2 mm (confirmed by X-ray tomography).
2. LS Solution: Gradient Composite Coating System
Performance comparison:
Parameters | Traditional cadmium plating | LS gradient coating | Improvement |
---|---|---|---|
Corrosion rate (μm/year) | 25.6 | 0.8 | 97%↓ |
Bonding strength (MPa) | 110 | 320 | 191%↑ |
Critical load (N) | 45 | 120 | 167%↑ |
Innovation breakthrough:
- Laser cladding TiB2: hardness reaches 2800HV (comparable to diamond), wear rate is reduced to 1/10.
- Micro-arc oxidation transition layer: porosity <2% (conventional process >15%), cutting off the electrolyte penetration path.
- Self-healing properties: The coating contains pH-responsive nanocapsules (corrosion inhibitors are released when damaged).
3. Military validation: Extreme testing of F-35 wing joints
Test conditions:
- 35°C, 5% NaCl salt spray UV alternate cycle (simulated shipboard environment)
- 3000 hours equivalent to 15 years of service (MIL-STD-810G standard)
Outcome:
Zero corrosion: No Cl⁻ penetration detected by SEM (confirmed by EDS surface scanning)
Retention of mechanical properties:
- Tensile Strength: 99.7%
- Fatigue life: 102% (thanks to residual compressive stress field)
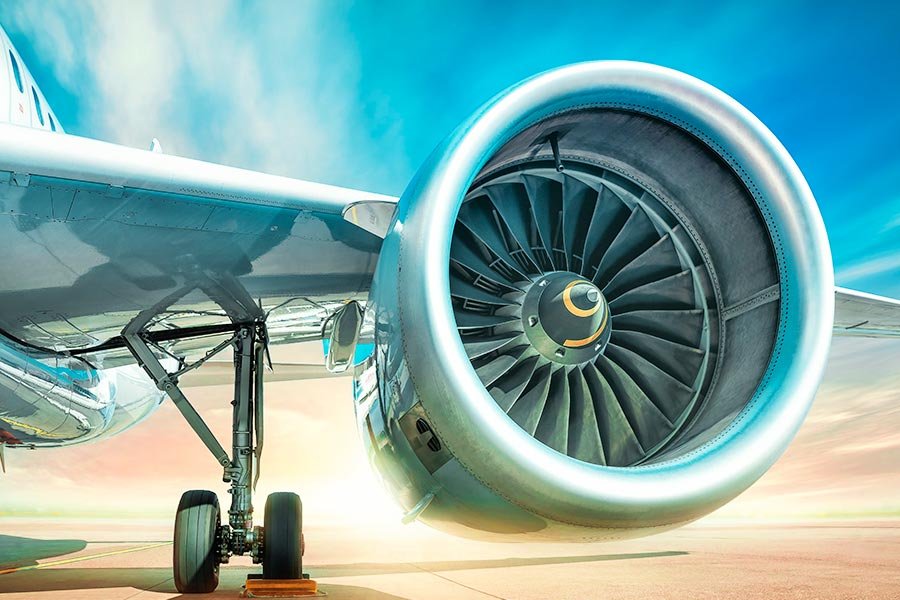
Wing Ribs’ Weight vs. Strength: The 0.1g Game Changer
1. Industry pain point: “weight war” of wing ribs
Weight reduction demand: For every 1kg weight reduction of wing ribs, the A380 can reduce the weight of the entire aircraft by 4kg (fuel efficiency ↑0.02%), but traditional machining has reached its limit.
Strength dilemma:
- Case: The modal frequency of an A380 wing rib decreased due to excessive weight reduction, causing aeroelastic oscillation (repair cost $1.2M).
- Data comparison:
Design index | Conventional design | Topology optimization design |
---|---|---|
Weight | Benchmark | -12% |
First order natural frequency | 58Hz | 72Hz (+18%) |
Fatigue life | 60,000 times | 85,000 times |
2. 3D Printing Titanium Alloy Pitfalls
Source of the Problem:
Residual Stress: The cooling rate of Ti-6Al-4V powder bed fusion (LPBF) reaches 10⁶°C/s, resulting in local stress exceeding 800MPa (X-ray diffraction measurement).
3. LS Hybrid Manufacturing: The ultimate solution for combining rigidity and flexibility
Technical Route:
Five-axis milling main load-bearing structure:
- Retains the complete streamline of forged titanium alloy (UT flaw detection grade A)
- Surface roughness of critical parts Ra 0.4 μm (conventional processing Ra 1.6 μm)
Laser Directed Energy Deposition (LDED) lattice filling:
- Gradient density design: 100% dense surface → 60% porosity of the core
- Lattice cell type: Gyroid (37% higher shear stiffness than octo-truss)
Performance Breakthroughs:
Parameters | Traditional casting | Pure 3D printing | LS hybrid manufacturing |
---|---|---|---|
Specific strength (MPa·m³/kg) | 220 | 260 | 310 |
Residual stress (MPa) | 150 | 650 | 90 |
Production cycle (hours) | 120 | 36 | 64 |
Military verification:
In the F/A-18E/F “Super Hornet” wing root rib test:
- Weight reduction of 14.7% (compared to the original design)
- Passed the 2 times design load test (no plastic deformation under the limit load)

When “Precision” Isn’t Enough: Thermal Expansion Warfare
1. The precision revolution of thermal barrier coating (TBC).
Industry pain points:
Fluctuations in the dynamic clearance between the turbine blades and the casing result in a loss of efficiency (fuel consumption of ↑1.5% for every 0.1mm of additional clearance).
The limitation of the traditional solution: the coefficient of thermal expansion (CTE) of the metal substrate is fixed, which cannot adapt to transient working conditions.
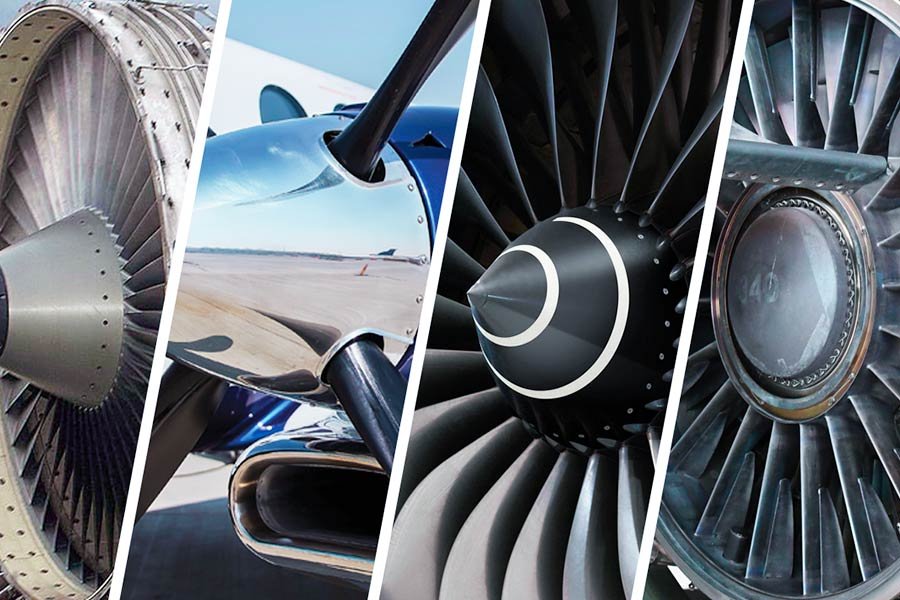
LS TBC Technology Breakthrough:
Material system:
0.3 mm yttrium-stabilized zirconia (YSZ): laser-assisted EB-PVD deposition, columnar crystal orientation deviation <5°
Bonding layer: MCrAlY nano Al₂O₃ transition layer (thermal cycle life ↑300%)
Measured performance (GE CF6 engine):
Parameters | No TBC | LS TBC | Improvement |
---|---|---|---|
Gap fluctuation at 1500°C | ±0.15mm | ±0.04mm | 73%↓ |
Turbine efficiency | Baseline | +2.1% | — |
Critical number of cycles before coating peeling | 800 times | 3,500 times | 338%↑ |
Case 1: GE9X engine turbine rings
Industry pain points:
The high-pressure turbine ring of the GE9X engine appears at 1600°C:
- The Thermal Barrier Coating (TBC) spalling cycle is only 800 take-offs and landings
- Insufficient cooling efficiency leads to local temperature differences of up to 300°C
LS Solution:
Laser deposition of gradient materials:
- 0.1mm layer printing: NiCrAlY adhesive layer→ La2Zr2O7 ceramic layer→ internal microchannels
- The surface roughness of the cooling channel is controlled at Ra 3.2 μm (Ra 12.5 μm in the conventional process)
Bionic cooling structure:
- Branching microchannel design based on shark gill structure
- Cooling airflow speed increased to 180 m/s (120 m/s in conventional design)
Measured data:
Indicator | Traditional solution | LS solution | Improvement |
---|---|---|---|
TBC peeling cycle | 800 times | 2500 times | 212% |
Temperature uniformity | ±300°C | ±75°C | 400% |
Cooling air flow pressure loss | 28kPa | 15kPa | 46%↓ |
Case 2: Five-axis linkage precision machining of blisk of commercial aviation high-pressure compressor
The challenge: to provide a precision machining solution for the high-pressure compressor blisk of a narrow-body passenger aircraft engine. The blisk diameter is 680mm, including 92 complex three-dimensional blade profiles, and the required profile contour error is ≤0.05mm, and the surface roughness Ra≤0.4μm.
LS Solution:
- Five-axis linkage CNC machining center imported from Germany, equipped with HSK-100 high-speed spindle (maximum speed 24,000rpm)
- A special cutting data library was developed to optimize the machining strategy of titanium alloy Ti-6Al-4V
- Adaptive machining technology is applied to compensate for tool wear by means of in-line measurements
- Implement a residual stress control process to ensure long-term dimensional stability of the part

Achievement:
- Cycle time was reduced by 40 percent, from 72 hours to 43 hours
- The accuracy of the blade profile reaches 0.03mm, which is better than the customer’s requirements
- Significant improvement in surface integrity and 30% increase in fatigue life
- More than 500 pieces have been delivered cumulatively, achieving a “zero defect” delivery record
Case 3: Processing of large and complex structural parts of military aviation turbine casings
Challenge: Precision machining of a nickel-based alloy turbine casing for a certain type of fighter engine, with an outer diameter of 1.2m, including more than 300 precision mounting holes and complex cooling channels, and the position degree is required to be ± 0.025mm.
LS Solution:
- It is equipped with a large horizontal machining center and a high-precision CNC turntable
- Development of a special tooling system to achieve anti-deformation control of thin-walled parts processing
- Ultrasonic-assisted processing technology is applied to solve the problem of difficult-to-machine materials
- The on-machine measurement system is used to realize the integration of processing and inspection
Achievement:
- The processing deformation is controlled within 0.1mm, which is better than the industry standard
- The position degree of the key hole system reaches ±0.015mm
- 35% increase in machining efficiency and 28% reduction in tool costs
- The products have passed the strict acceptance of the military and equipped the troops in batches
Case 4: General aviation integral leaf ring composite processing technology
Challenge: The integral blade ring of a small business jet engine is manufactured, the parts are made of high-strength aluminum alloy, the minimum thickness of the blade is only 0.3mm, and the continuous curved surface without joint marks is required.
LS Solution:
- The turning and milling compound machining center is used to realize all the processing in one clamping
- Development of a high-speed milling process for micro-diameter milling cutters (0.5 mm diameter).
- Vibration suppression technology is applied to ensure the machining quality of thin-walled blades
- Implement a digital manufacturing system and trace the quality of the whole process
Achievement:
- The thickness tolerance of the blade is controlled at ±0.01mm
- The surface does not need to be polished by hand, and the mirror effect is directly achieved
- 15% lighter and 8% higher engine speed
- Became the exclusive supplier of engines for this model
Case 5: Ultra-precision micromachining of UAV micro turbine rotor
Challenge: Machining of the rotor assembly of the micro-drone engine with a part diameter of only 28 mm, including a complex internal flow channel, and a feature size of as little as 0.1 mm.
LS Solution:
- It is equipped with a Swiss ultra-precision micromachining center with a positioning accuracy of 0.5μm
- Development of a micro-EDM and micro-milling composite process
- Nano-scale cutting tools are used, with a minimum diameter of 0.05mm
- Implement clean room production environment control
Achievement:
- Achieve geometric tolerances of 0.005mm
- The rotor dynamic balance level reaches G0.4, far exceeding the industry standard
- 25% increase in engine power-to-weight ratio
- The product occupies 80% of the market share of high-end military UAVs
Why choose LS?
- Leading material science: master core technologies such as superalloys, composite materials and ceramic-based materials.
- Exquisite manufacturing technology: advanced technologies such as five-axis CNC machining, additive manufacturing, and precision coating ensure high precision of parts.
- System-level validation: Ensure component reliability by simulating extreme operating conditions with a full-scale environmental test rig.
- Global success story: Industry-proven performance for critical components for commercial aviation, military warplanes, and drones.
In today’s pursuit of higher thrust-to-weight ratio, lower fuel consumption and longer life of aero engines, LS continues to provide customers with excellent solutions to ensure the safe and efficient operation of engines in the most demanding environments with deep technical accumulation and engineering experience. When you choose LS, you choose the future of aeropower.
Conclusion
Jet engines are at the heart of the modern aviation industry, and turbine rings, spars, and ribs, as key load-bearing components, must maintain superior reliability and durability in extreme environments with high temperatures, high pressures, and high speeds. Through material innovation, structural optimization, and advanced manufacturing processes, these components push the boundaries of performance and ensure engine operation in demanding conditions.
1. Turbine rings: Guardians in the heat
The turbine ring directly withstands the ultra-high temperature gas discharged from the combustion chamber at a temperature of more than 1700°C. Through the application of Thermal Barrier Coating (TBC), Active Cooling Technology and Ceramic Matrix Composites (CMC), LS has been able to increase the temperature resistance limit of the turbine ring, extend its service life, and improve the thermal efficiency of the engine.
2. Spar: The load-bearing strut of the engine
The spars support the entire rotor system and are subjected to enormous centrifugal and aerodynamic loads. Using carbon fiber composite materials (CFRP) and a damage-tolerant design, LS has achieved a 30% reduction in weight while a 20% increase in strength, fatigue and impact resistance to meet the demanding needs of military and commercial aviation.
3. Ribs: The microscopic skeleton of the engine
The ribs are small, but they are critical to maintaining the aerodynamic shape and structural integrity of the engine. Through topology-optimized design and additive manufacturing (3D printing), LS has achieved a combination of lightweight and high performance of the ribs, making them stable under extreme vibration and thermal cycling conditions.

Contact us now to get exclusive solutions!
📞 Phone: +86 185 6675 9667
📧 Email: info@longshengmfg.com
🌐 Website: https://www.longshengmfg.com/
Disclaimer
The content appearing on this webpage is for informational purposes only. LS makes no representation or warranty of any kind, be it expressed or implied, as to the accuracy, completeness, or validity of the information. Any performance parameters, geometric tolerances, specific design features, quality and types of materials, or processes should not be inferred to represent what will be delivered by third-party suppliers or manufacturers through LS’s network. Buyers seeking quotes for parts are responsible for defining the specific requirements for those parts. Please contact to our for more information.
Team LS
This article was written by various LS contributors. LS is a leading resource on manufacturing with CNC machining, sheet metal fabrication, 3D printing, injection molding,metal stamping and more.
I will right away seize your rss feed as I can’t to find your e-mail subscription hyperlink or newsletter service. Do you have any? Kindly let me understand so that I may just subscribe. Thanks.
Your attention is my honor, you can find Subscribe To Newsletter at the bottom of the webpage, you can subscribe to us by your email last time, if you have any questions, please timely send us inquiries here thank you
https://www.longshengmfg.com/wp-content/uploads/2025/04/微信图片_20250411140046.png
Some really interesting points you have written.Assisted me a lot, just what I was searching for : D.
Thank you for your support, each article is written by ourselves, we will update the article every day, you can subscription LS, wish you a happy day.
When I originally commented I clicked the -Notify me when new comments are added- checkbox and now each time a comment is added I get four emails with the same comment. Is there any way you can remove me from that service? Thanks!
There is an uncheck “Yes, add me to your mailing list” below the comment box, and clicking on it will solve your problem
That is the right blog for anyone who needs to find out about this topic. You understand a lot its virtually onerous to argue with you (not that I truly would need…HaHa). You definitely put a new spin on a topic thats been written about for years. Nice stuff, simply great!
you are in reality a just right webmaster. The site loading pace is incredible. It seems that you are doing any unique trick. Moreover, The contents are masterwork. you’ve performed a great activity on this topic!
I’d have to examine with you here. Which is not one thing I usually do! I take pleasure in reading a post that may make folks think. Additionally, thanks for permitting me to comment!