As an important part of modern machinery manufacturing industry, metal CNC machining plays an important role, because metal materials usually have high strength, corrosion resistance and high temperature resistance, can undertake a variety of heavy load and high load work environment, and CNC machining technology can produce a variety of precision details and complex shape of mechanical parts.
If you’re looking for a metal CNC machining services, you probably already know the many benefits it can provide, but do you know how it actually works? This blog will discuss the principles, advantages, industrial applications, available technologies and others that can help you build precision machine parts for your project.
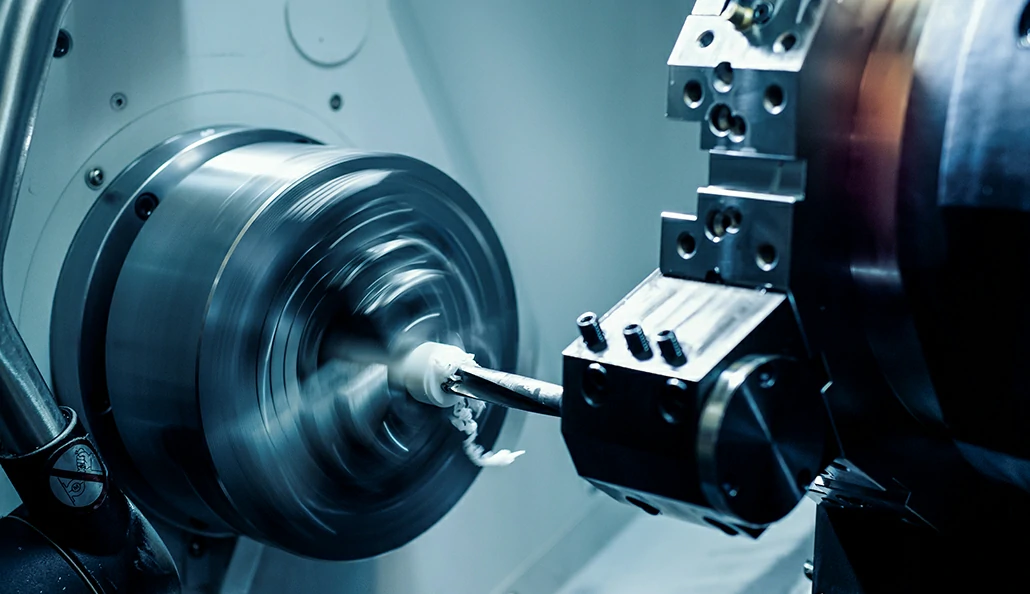
What is CNC machining of metal?
CNC machining refers to the automatic machining through the computer to control the machine, and the metal CNC machining is on this basis, for metal materials of a kind of processing. The principle of CNC machining of metal is to adjust and improve the quality of metal processing in time by computer control machine. This unique process can determine the machining route of metal materials according to the relationship between unique things. Metal CNC machining can bring some important advantages: high efficiency, high efficiency, higher precision, higher precision.
The development of CNC machining technology
CNC (Computer Numerical Control) machining technology is a technology of machining workpiece by using computer program to control the machine tool. The technology is not only widely used in metal machining , but also in laser cutting, automobile manufacturing and other fields. The development of CNC machining technology can be traced back to the 1950s. With the continuous development of computer and control technology, CNC machining technology has been rapid development, has become one of the main machining technology in manufacturing industry.
The basic principle of CNC machining of metal
CNC is short for digital control, which means that in CNC machining of metals, a computer controls a machine to cut and shape metal parts. The following is the basic principle of CNC machining of metal.
- CAD design Computer aided design software (CAD) is needed to create 3D models before the machining can begin. CAD models allow you to see the apparent size, shape, and position of the part. CAD can also generate three-dimensional entity files (.stl files) for uploading designs to computer-controlled machine tools.
- Write G code After creating the CAD file, you need to use the G code to indicate its operation process. G code is a special code recognized by CNC machine tools, which will guide the CNC machine to perform tasks in the process.
- CAM software CAM software is needed in order to write and manage G code in CNC machining of metal. CAM software can translate 3D designs into executable G code files and includes tool path, layer-by-layer material removal speed and other machining parameters while saving time and labor costs. In addition, CAM software also needs to be used to check the machining results to ensure the quality and accuracy of the final parts.
- Machining shaft and tool In CNC machining of metal, tool and machining shaft are the key components. Normally, the machining shaft moves in three directions (X, Y, Z), and the tool is driven by the spindle. Different types of tools include drill, reamer, drilling, grinding and engraving tools, etc.
- machining process Once the machine tool is set up, the computer control system on the machine tool will initiate the G code in the CAM program. The machine will drill, mill, and cut the parts until they reach the desired precision and size for the design.
- Accuracy verification After machining, the parts need to be measured to ensure that they meet the design requirements. Machine tool operators use precision measuring instruments to measure parameters such as size, Angle and profile of parts. If the part does not meet the requirements, the machine operator will readjust the machine for remanufacturing.
How to operate CNC machine?
CNC machines can perform many different machining tasks through numerical control programs. They can cut, shape and finish metals by heating or pressure. The CNC control system can control various operations through G code and M code, which can be generated by CAD or CAM software. Here’s how this process works:
First, the CAD or CAM software will develop a blueprint or model. It includes various machining parameters, such as cutting depth and speed. The controller then reads the data and turns it into a processor. During the machining process, the controller will monitor the machining parameters in real time and control the machine to ensure the best machining quality and finished product accuracy.

What Types Of CNC Machine AT-Machining Can Machine Metals?
Below are the metal CNC machines we utilize for CNC machining.
CNC Lathe
This stationary cutting tool is ideal for shaping metal and plastic. It has the lowest cost per part relative to other CNC machining operations and very high production parts capabilities.
3 Axis CNC Milling
This CNC milling machines produce parts with excellent accuracy, at a low cost, and with relatively simple geometries.
Milling-Turning CNC Center
This machine utilize the advantages of both CNC milling and turning in a single system to produce complex parts more affordably than 5-axis machining. It offers a high degree of design freedom and manufacturing capabilities.
Indexed 5-Axis
This machine produces parts that do not align with one or the main axis with high accuracy. However, using it for machining is quite expensive.
Continuous 5-Axis
This is the most expensive machine we use for machining. However, it produces complex parts with high accuracy that require minimal machining mark.
Metal CNC Machining Methods
Metal CNC machining , refers to the use of computer control in CNC machining center, through cutting and other machining methods for metal parts manufacturing, specific machining methods are as follows:
milling
Milling is a CNC machining technique in which materials are cut by rotating tools. The technology is used to make a wide range of metal products, including aircraft parts, auto parts and machine parts. With milling, you can cut the workpiece from different angles, providing greater cutting accuracy for your project.
turning
Unlike milling, turning is a CNC machining technique in which materials are cut by rotating the workpiece instead of the cutting tool. In turning, you can produce a variety of accurate metal products with very high precision by rotating the workpiece, cutting tools and cutting fluid. In addition, turning can process a variety of metal products, including titanium alloy, aluminum, steel and copper.
Laser cutting
Laser cutting is a fast, high precision and efficient CNC machining technology. The technique uses a beam of light to cut the material without leaving any marks on the surface. Laser cutting can be used for the machining of various metal materials, including steel, stainless steel, copper and aluminum.
EDM
Electric discharge machining (EDM) is a CNC machining technology for cutting metal by discharge. During this machining, an electrical discharge passes through the workpiece and dissolves and cuts the workpiece as it passes through, forming the desired shape. Edm can be used to manufacture stainless steel, copper, aluminum and other metal products, and is well suited for making complex and fine shapes.
CNC machining for metal
Many of the metals used in CNC machining can be adapted to make parts and products manufactured in multiple industries. Their use depends on their properties. Some machinable metals, such as aluminum alloys, have excellent mechanical properties, allowing them to replace many other machinable materials. The following are the most common metal for custom metalworking:
aluminum
Aluminum alloy has excellent mechanical properties, low density, good heat resistance, wear resistance and conductivity. It is one of the main materials used in aerospace, automobile, construction and electronic products. Aluminum alloy is easy to process and can be processed by drilling, milling, cutting, punching and other machining methods.

Advantages | Disadvantages |
---|---|
Light: Aluminum is a very light metal, lighter than many other metals such as steel and copper. | Greater softness: Compared to other common metals, aluminum hardness is low, easy to scratch and damage. |
Corrosion resistance: Because of its excellent corrosion resistance, aluminum is widely used in the manufacture of light aircraft and automobile casings and structures. | Expensive: Aluminum is expensive relative to common metals like steel |
Recyclability: Aluminum can be recycled, making it an environmentally friendly option. |
Industrial application:
Construction: Aluminum alloy materials are widely used in the manufacture of building doors, Windows and curtain walls.
Aerospace: Aluminum is widely used to make aircraft casings and components because of its lightweight, corrosion resistance and other properties.
Mild steel
Mild steel is a very tough metal material that can withstand high pressures and temperatures and is suitable for many important machine parts and even building structures. Steel is widely used because of its lower cost compared with other metals.

Advantages | Disadvantages |
---|---|
Good plasticity: Mild steel is easier to bend and form than hard steel, making it ideal for many CNC machining tasks. | Easy to rust: Mild steel is less resistant to corrosion than many other metals. |
Great plasticity: When mild steel is heated, it can be transformed into objects of various shapes, making it ideal for many custom metal parts. | Must cool: Mild steel must be cooled by coolant after machining. Because if they didn’t lose heat, their surfaces would be weak. |
Low cost: Mild steel is relatively inexpensive and readily available compared to other advanced alloys and steel sources. |
Industrial application:
Automotive industry: Mild steel is widely used in the manufacture of automobile chassis, frame and other structural components.
Medical equipment: Mild steel is used in consumables such as disposable needles and surgical instruments.
304 stainless steel
Stainless steel is a widely used metal that is ideal for CNC machining due to its high corrosion resistance, strength and good weldability. It is easier to obtain precise size and shape than other metallic materials, and because it is less prone to contamination, it is widely used in food packaging and medical devices.

Advantages | Disadvantages |
---|---|
High temperature resistance: Stainless steel has good high temperature resistance characteristics, so it is suitable for CNC machining tasks for manufacturing high temperature equipment. | Harder: Stainless steel hardness is larger, so it needs more power and tools, in order to process the desired shape. |
Corrosion resistance: Stainless steel has very good corrosion resistance, so it is widely used in the manufacturing of kitchenware, medical instruments and other industries. | Expensive: Stainless steel relative to other common metals, such as aluminum, mild steel, etc., the price is more expensive. |
Good appearance: Stainless steel is easy to produce a smooth, glossy surface, so it is also widely used in some industries that require a good appearance. |
Industrial application:
Kitchen industry: Stainless steel is widely used in the manufacture of kitchen appliances, cookware, sinks and other kitchen equipment.
Medical equipment: surgical instruments, dental equipment and medical instruments made of stainless steel are more durable, especially suitable for disinfection and cleaning of medical equipment
Food machining industry, petrochemical industry, energy industry, etc
Titanium alloy
Titanium alloy is a very light metal material, but high strength. It can be used in hot working, can withstand extremely low or extremely high temperatures and is suitable for aerospace, military and medical applications.

Advantages | Disadvantages |
---|---|
high strength and specific strength | high price |
good heat resistance | difficult machining |
good stability | cutting edge easy to wear |
corrosion resistance |
brass
Brass is an alloy of copper and zinc. It has good wear and corrosion resistance and is suitable for products requiring a beautiful appearance. It is a relatively soft metal, making it ideal for applications that require less twisting and stretching.

Advantages | Disadvantages |
---|---|
High strength: Under high load conditions, metal parts need to withstand great pressure and stress. Therefore, metals should have sufficient strength to ensure their stability and reliability. | Easy to be affected by heat: CNC machining may require high speed movement and high temperature cutting and other conditions, which may lead to metal deformation, crack and brittleness by heat. |
Corrosion resistance: Metal parts in CNC machining may be exposed to moisture, corrosion or chemical corrosion. Choosing a metal with good corrosion resistance ensures that the product maintains its function and performance over its useful life. | Environmental pollution: Some metals may cause environmental pollution. Therefore, strict environmental and waste management procedures should be taken into account when selecting metals. |
Machinability: The metal used for CNC machining should be easy to cut, drill, mill, turn, etc. They should have good machinability to ensure high quality production efficiency and product quality. |
Industrial application:
Aerospace: high-strength, lightweight brass material, one of the most commonly used materials in the aerospace industry. They are widely used in aircraft structure, engine parts, axle and tools.
Machinery: Mechanical engineers often use them to construct complex mechanical parts and devices. These metals have high strength, good wear resistance and low friction coefficient.
Automotive Industry: The automotive industry requires the use of a large number of different types of brass. These metals are widely used in parts and components such as engines, chassis and interiors.
Magnesium material
Magnesium material is a kind of light metal material, is one of the best choices in CNC machining. It is widely used in medical equipment, automobile manufacturing and electronic equipment. Compared with other metal materials, magnesium materials have better thermal and electrical conductivity.

Advantages | Disadvantages |
---|---|
Very light, the weight of aluminum material 1/3 | Difficult to process |
The heat conduction and electrical conductivity are very good | expensive |
The heat conduction and electrical conductivity are very good |
Industrial application:
The manufacture of medical devices
Automobile manufacturing
The manufacture of internal components of electronic devices
Advantages of CNC machining technology for metal
Compared with traditional machining means, metal CNC machining has the following advantages:
1.High efficiency and precision
One of the biggest benefits of CNC machining of metals is its accuracy. Using 3D computer-aided design (CAD) software, metal CNC technology can accurately create almost any shape in the designer’s geometry, avoiding the pitfalls of traditional cutting methods, such as “manual error” and repeatability problems. In addition, metal CNC technology enables the process to automatically generate the necessary tool paths and tool movements, resulting in higher production and product rates. Metal CNC technology is in 3D CAD modeling and computer control under the precise guidance of high speed, it starts from scratch to process the required model, so that the production time is greatly shortened.
2.High stability
Metal CNC machining manual operation is susceptible to human error, machine operation will not exist such a situation. Automatic machining can avoid repeated operations, reduce machine wear and maintenance, but also can reduce the failure rate, improve production efficiency and stability.
3.Automated production process
CNC machining technology uses computer programs to operate and control on the basis of complete automation, thus greatly reducing manual intervention and improving production efficiency. CNC machines are durable and can be processed continuously for a long time without human intervention to complete high quality parts processing and reduce labor costs. In the case of large-scale and high volume production, the use of CNC machining technology can better meet the production needs of enterprises.
4.machining of various metal materials
CNC machining technology allows all kinds of metals and alloy materials to be perfectly processed, including aluminum, steel, titanium and so on. Using different tools and processing strategies, different shapes of products can be easily created. CNC machining technology is not limited by shape, through the curve and circular cutting, more flexible than the traditional processing, more able to achieve high precision parts machining .
5.Low production cost
Metal CNC technology may have a higher starting cost than other methods of manufacturing the same product. However, given the multiple advantages of the technology, every part of the CNC machine is reducing the cost of production. To help you better understand these cost savings, we’ve broken them down into the following sections:
Automation: CNC technology allows a machine to work continuously for hours without human intervention. This means that you can increase your business by running machines for multiple customers without intervention and maximizing your workload.
Waste Reduction: Metal CNC technology allows trimming and machining on materials while using less material to create complex parts. Therefore, this technology can not only produce high quality products, but also help reduce waste, which will make an important contribution to the economy and ecological environment of many companies.
6.High repeatability
Another significant advantage of CNC machining of metals is high repeatability. Due to the use of computer numerical control equipment, the process can be programmed control, and record all machining parameters. In this way, when machining large quantities of parts, the equipment can repeat the same machining steps and produce parts in an efficient manner.
CNC machining of metal also has its disadvantages. These include:
High equipment cost: metal CNC machining technology production equipment is expensive. The purchase of CNC machining equipment requires high capital investment, which requires enterprises to have enough financial resources for investment.
High technical requirements: to be able to correctly operate and set up CNC machining equipment, need certain technical knowledge and operational experience, so before using CNC machining equipment, need to accept training and learning, which takes time and cost. If you are going to use CNC machining equipment, you need to be very careful, or you may waste materials, or you may cause damage to the equipment.
Take time to set up: In order for CNC machining equipment to work best, you need to set up programming and other parameters. This can take a long time, especially for those who are new to CNC machining. In addition to the set time, if something goes wrong, you will need to spend some time maintaining and repairing the equipment.
The application field of CNC machining of metal
Metal CNC machining method reduces the production cycle, ensures the accuracy of the work, reduces the labor force of workers, and can be customized precision parts, some common application areas are as follows:
1.Automobile parts manufacturing
One of the challenges in car manufacturing is producing large numbers of sophisticated components. These parts have to meet a very strict set of quality standards, and these standards have increased as the car has evolved. These parts can be easily produced using metal CNC machining technology, ensuring accuracy and quality, and improving production efficiency.
2.Electronic and electrical industries
The electronics and appliances industry requires many high-precision, high-quality components and components. CNC machining of metals can be responsible for handling many of the most precise components in electronic devices, such as high-quality motors and generators. In addition, it is also used to produce electronic components such as mobile phones, computers and other components.
3.Space engineering
The precision and quality of the parts of the aviation industry is also very high, expensive, and metal CNC machining can also meet these requirements. The use of CNC machining can produce precise parts that must meet the strict requirements of extreme environments such as high speed, high temperature and high pressure.
4.3D printing
The progress of 3D printing technology has also improved the CNC machining technology of metal. Using 3D printing technology, a single layer of template can be created on a metal surface, which can then be CNC processed to produce multiple parts simultaneously, reducing manufacturing time and costs.

5.Aviation industry
Strength and precision are very important elements in the aviation industry. The manufacture of aircraft components is a highly technical and complex process. CNC machining of metal can effectively provide high precision cutting and positioning through CNC machine tools to manufacture a variety of aerospace components such as engine gearboxes, elevators, wings, fuselages, seats and cabins.
6.Medical equipment
Medical device manufacturing requires high precision, high quality and reliability. Therefore, for medical equipment manufacturers, metal CNC machining technology is very necessary. With CNC machining technology, medical equipment, parts and models can be rapidly produced so that doctors can diagnose and treat patients more accurately.
7.Manufacture custom parts
CNC machining of metal can produce a variety of customized parts. It provides manufacturers and customers with an option to customize production to meet customer needs for personalization, quality and performance.
Metal CNC machining alternative scheme
In addition to CNC machining of metal parts, other rapid prototyping processes can be used as alternatives. Common ones include:
Injection molding
Injection molding is a manufacturing process in which molten material is injected into a mold to form the desired shape. Compared with CNC machining of metal, injection molding has the following advantages:
Suitable for mass production, higher production efficiency.
It can quickly produce complex and high-precision products in a short time.
The materials used are more abundant and can adapt to a wider range of production needs.
milling
Milling is a classic machining method, its advantages are obvious: low cost, strong controllability. By hand milling, workers can control the feed rate of the cutter and the depth of each time as needed, resulting in more detailed machining. Of course, milling machining also has disadvantages, such as the need to have a certain technical foundation, and efficiency is not high. However, in some special cases, such as the need to process some irregular shape or machining some small parts, milling machining still has its irreplaceable status.
stamping
Stamping is a high yield and low cost metal machining method. In stamping, metal parts are processed using a CAM or hydraulic press for several minor deformations. This process is suitable for most metal types and can be used in a variety of industries.
EDM
Edm is a machining technique that creates extremely fine cuts in metal. It is often used to make complex metal parts and molds. The technology works with many types of metals, including steel, copper, aluminum and titanium. It is most widely used in the manufacture of parts such as chamfer, cavity, internal hole and plane.
Laser cutting
Laser cutting technology is widely used in cutting all kinds of materials and parts manufacturing. Compared with the traditional cutting method, laser cutting technology is not only more efficient, but also can improve the machining accuracy to a great extent. Especially in the machining of some high hardness metal materials, laser cutting technology can better ensure the machining quality and stability. Of course, laser cutting technology is not suitable for all machining situations, some of the precision requirements of the very high parts also need to use CNC machine tool processing.
How to choose metal CNC machining manufacturer

When to choose CNC machining of metal
Choosing from many of the metal manufacturing processes discussed above can be challenging. So here are some considerations to help you decide if CNC machining of metal is right for your project:
Need high precision machining
CNC machining can precisely control the position and action of each tool. This makes it possible to achieve high precision machining. If you need to manufacture parts with high precision, then CNC machining may be your best choice.
Large quantities of manufactured goods need to be produced
CNC machining of metal can automatically produce a large number of manufactured goods according to your needs. This process combines mold manufacturing with production, which allows you to produce large quantities of manufactured goods in a relatively short time.
Precision is required for production
CNC machining of metal can complete very complex work in a very short time. This is very advantageous for situations where precise machining is required. For example, if you need to process parts in a variety of shapes and sizes, CNC machining of metals may be your best choice.
Less human intervention is required
CNC machining of metal uses computer control. This means that you can produce high quality manufactured goods at higher speeds and with much less labor intervention costs. This can make you more efficient throughout the production process.
Need to produce manufactured goods quickly
CNC machining of metal can produce a large number of manufactured goods in a very short time. This means that you can produce manufactured goods quickly and with guaranteed delivery times.
What Factors Should Be Considered When Choosing A Metal For CNC Machining?
Choosing the right material goes a long way to determining the cost and function of the final product. With the right material, it becomes possible to balance, use, cost, and machinability. Here are some factors to consider when choosing a material for CNC machining;
CNC Machining Time
The type of metal chosen often determines the time spent machining it. Selecting a metal with low machinability would extend the CNC machining time considerably, as opposed to selecting a metal like aluminum with its high precision machinability. Furthermore, the longer the time spent machining, the more expensive the manufacturing process becomes.
Another factor that determines machining time is the complexity of the parts. A CNC machine would spend more time machining a complex part than a simple part, which also increases CNC machining costs.
Strength and Environment Requirements for the CNC Machined Parts
The proposed use of CNC machined parts is another factor that would determine the choice of metal. For instance, when making parts that would experience heavy stress and loading, a metal with high strength, like steel alloy, is better than copper.
On the other hand, where the final product should have strength similar to steel but without its weight, like in the manufacturing of aircraft, then titanium might be ideal.
Additionally, the environment in which the part would operate is another factor that should determine the metal used for making the part.
Finishes and Post-Processing for CNC Machined Metals
The type of metal selected also determines the finishing and post-processing of the machined parts. For instance, soft metals or hard metals with low machinability often have tooling marks and burs, which finishing and post-processing help remove.
Although finishing and post-processing improve the appearance of a metal part, it also raises the cost of machining significantly. However, knowing the finishing and post-processing required makes it easier to choose the right metal for part metal fabrication. In most cases, it will be a metal with high manufacturability if a high-quality surface finish is important.
FAQs
How much does metal CNC machining cost?
The cost of metal CNC machining depends on the complexity and size of the part and the type of metal that is used. These variables will affect the type of machine that is required, the time it takes to produce the part, and the cost of the raw material.
We use machine learning algorithms to calculate the exact cost of any machinable part directly from a CAD file, based on millions of CNC machining orders we’ve previously processed. Simply upload a CAD file to generate a quote: get an instant CNC machining quote.
What is metal machining?
Metal machining is a manufacturing process that involves cutting a piece of raw metal until a final desired shape or object remains. With CNC metal machining, unwanted geometry is cut from a raw block of metal, bit by bit with a computer numerically controlled (CNC) milling or turning cutting tool, very precisely and allows complex parts to be produced with great accuracy.
What can you make with a metal CNC machine?
With a CNC machine, you can create almost any component that can be represented with a 3D CAD file. The more complex the machine (eg: 5-axis CNC milling machines) the more complex the geometry that can be milled.