According to the basic fabrication methods of sheet metal parts, such as material cutting, bending, stretching, forming, welding. This article discusses the process requirements that need to be paid attention to for each fabrication method.
What is Sheet Metal Fabrication
Sheet metal fabrication is a process that is used to shape and form thin, flat metal sheets by cutting, bending, punching, and welding them into various shapes. Different metals, such as brass, steel, copper, tin, titanium, and aluminum, are formed and configured using sheet metal fabrication. Platinum, gold, and silver are useful for decorative purposes. Sheet metal is used to construct numerous objects with varying thicknesses from extremely thin sheets, also known as foil or leaf, to thicker sheets > 6 mm, also known as plate. Metal sheet thickness is referred to as gauge and ranges from 30 gauge to 8 gauge with the metal gauge being inversely proportional to the thickness of the metal.

In essence, sheet metal fabrication entails turning or processing sheet metal into functional parts by cutting, bending, or stretching. The process can create holes and 2D geometric cut out shapes while other deformation processes bend sheets into different angles or yield complex contours from stretching.
The raw material used by fabricators for sheet metal fabrication comes from rolling processes where sheet metal is sold as standardized flat and rectangular sheets. In instances where these sheets are thin and long, they come in the form of rolls. Thus, the first step in sheet metal fabrication is to cut out a ‘blank’ in the desired shape and size of a sheet from the larger sheet.
Parts formed from sheet metal fabrication can be used in a wide range of industries, namely construction, automotive, aircraft, consumer products, furniture, and HVAC.
Sheet metal fabricationmethod
Non-mold fabrication: through the number of punching, laser cutting, shearing machine, folding machine, riveting machine and other equipment for sheet metal fabrication process, generally used for sample production or small batch production, the cost is high.
Mold fabrication: Through a fixed mold, sheet metal fabrication, generally have blanking die, forming die, mainly used for mass production, low cost.
Applications of Sheet Metal Fabrication
Whether for structural purposes, decorative elements, or functional components within other products, many different industries rely on sheet metal fabrication.
Let’s take a closer look at its variety of common use cases.
Kiosks, vending machines & enclosures
Vending machines and kiosks bring in significant revenue for many customer-facing companies – for example, gyms and leisure centres. This is why care needs to be taken in their construction.
There are a large number of individual components needed to go into building these types of machines, which is why they require the application of sheet metal fabrication.
Construction & Security
The construction and security sectors use the application of sheet metal fabrication for products such as security doors, guard rails, security grills and bespoke security enclosures.
Retail
Creating appealing visual merchandise, as well as product displays, in the retail sector requires sheet metal fabrication.
Sheet metal fabrication can help create a wide range of retail display units for different retail clients, retail spaces and shop displays. For example, bar displays, retail display cubes, portable displays and point-of-sale stands. These products need to be eye-catching and highly functional.
Science, medical & food
Particularly the scientific, medical and food industries utilise sheet metal fabrication to create products found in commercial and industrial kitchens such as worktop surfaces, storage units, and sinks.
Stainless steel tends to be the material of choice for many applications in the food production and preparation industries.
Transportation
The transportation sector uses thousands of different products made using metal fabrication. For example, emergency vehicles rely on sheet metal fabrication for the construction of products such as glove-box enclosures, side steps, door-handle mounts, and steel surrounds for tail-lift doors.
Sheet metal fabrication is an excellent method for creating parts both large and small that can go into vehicle construction. On top of that, safety rails on building sites, ladder hatch trap doors, and stair-safe products are constructed through sheet metal fabrication.
Sheet metal fabrication process
Sheet metal forming involves a number of manufacturing processes. The following list contains some of the primary sheet metal forming operations:
1. Curling
Curling is a process that adds a circular, hollow roll to the edge of sheet metal. This is done to deburr the edges, but also to add strength and make the sheets safer to handle. Metal sheets are usually fed into specialized machines that gradually roll or bend the edges to form a smooth, rounded profile.
Curling is commonly used in HVAC, appliance manufacturing, and architectural applications to create edges on panels, trim, or housings. Most metals can undergo curling, depending on their ductility and thickness, including: steel, aluminum, and brass.
Curling adds strength to the edges of parts and improves rigidity and safety. Complex shapes or tight rolls can be challenging to achieve through curling. Specialized tooling and machinery may also be required to perform curling, depending on the application.
2.Bending
A bent part has a minimum bending radius. When the material is bent, the outer layer is stretched in the rounded area and the inner layer is compressed. When the material thickness is constant, the smaller the internal bending radius, the more severe the stretching and compression of the material; When the tensile force of the outer layer exceeds the limit of the material, fracture and fracture occur.

3.welding
Mainly electric arc welding and gas welding Arc welding is flexible, mobile, and widely applicable, allowing for full position welding; The equipment used has the advantages of simplicity, good durability, and low maintenance costs. But the labor intensity is high and the quality is not stable enough, depending on the operator’s level. Suitable for welding carbon steel, low alloy steel, and non ferrous alloys such as copper and aluminum with a thickness of 3mm or more.
The temperature and properties of the gas welding flame can be adjusted. Compared to the heat source of electric arc welding, the heat affected zone is wider, and the heat is not as concentrated as the arc. The productivity is low, and it is applied to the welding of thin-walled structures and small parts. It can weld steel, cast iron, aluminum, copper and its alloys, hard alloys, etc.

4. Ironing
Ironing is a process used to improve the surface finish of sheet metal parts and achieve uniform thickness. A metal part is pressed through a die or series of dies which incrementally reduces clearance. By passing through the die, the walls of the part are thinned and elongated, without altering the shape significantly.
Ironing is used for producing aluminum cans, but also for other applications in which a consistent thickness and a good surface finish are required. Metals with high ductility are suitable candidates for ironing, including steel and aluminum.
Ironing improves dimensional accuracy, surface finish, and thickness uniformity in metal parts, but requires specialized tooling and machinery. It is also unsuited for parts that require significant shape changes.
5. Hydroforming
Hydroforming is a process of shaping metals into complex forms by using high-pressure fluid. A metal blank is placed within a die cavity, whereafter high-pressure fluid is pumped onto the blank, forcing it into the shape of the die.
Hydroforming is commonly used in the automotive, medical, and aerospace industries, for which complex shapes are often required. Metals with high ductility are suitable for hydroforming, like: aluminum, stainless steel, and brass.
Hydroforming can create complex shapes with uniform wall thickness, with reduced waste and relatively low cost compared to other forming methods. Disadvantages of hydroforming include the specialized equipment that is needed, which requires a high initial investment, as well as the specialized expertise needed to perform hydroforming.
6. Deep Drawing
Deep drawing is a process used to create hollow cylindrical shapes. It works by placing sheet metal over a die and pressing the metal blank into the die cavity using a punch, resulting in a hollow cylindrical shape with no reduction in the thickness of the sheet metal.
Deep drawing is used for creating containers, beverage cans, and automotive parts such as door panels. The process can be suitable with any metals with high ductility and malleability. Aluminum, stainless steel, copper, and brass are commonly used in deep drawing.
Deep drawing allows for the creation of complex hollow shapes with consistent wall thickness and precise dimensions. It requires minimal labor and is cost-effective at high production volumes.
7. Shearing
Shearing is a cutting process used to cut sheet metal along a straight line. The sheet metal blank is positioned on a shearing machine, which has two blades that slide past each other to cut the metal. The blank is clamped in place, and the upper blade of the shearing machine is lowered onto the blank to make the cut.
Shearing is used to cut metal sheets into smaller pieces or to trim edges. It is widely used in the manufacturing, construction, and automotive industries. Steel, aluminum, and stainless steel, along with most other metals can be sheared. The thickness of the metal and the capability of the shearing machine are the limiting factors as to what can be sheared.
Shearing is a rapid process, produces minimal waste, and is cost-effective at high volumes, but can cause edge deformation and burrs, especially in thicker materials. Shearing only cuts along a straight line, and must be combined with other processes to produce complex shapes.
8. Punching
Punching is the process of removing material from sheet metal to create holes, slots, or specific shapes. Sheet metal is placed between a punch and a die. The die supports the sheet metal, while the punch is forced through the sheet metal into the die to create the hole or shape.
Punching is also used for creating enclosures, brackets, and panels. Most metals can be used for punching, with the thickness of the sheet and the capabilities of the punching machine being the limiting factor.
Punching is an automated, rapid process. It has good repeatability and is a highly efficient process, especially for high-volume production. On the other hand, tooling costs can be high, especially for custom shapes. Some post-processing may also be required, especially for intricate designs.
Material selection
The materials commonly used in sheet metal fabrication include cold-rolled sheet metal (SPCC), hot-rolled sheet metal (SHCC), galvanized sheet metal (SECC, SGCC), copper (CU), brass, red copper, beryllium copper, aluminum sheet metal (6061, 6063, hard aluminum, etc.), aluminum profiles, and stainless steel (mirror, brushed, and misted). Depending on the product’s purpose and material selection, it is generally necessary to consider the product’s purpose and cost.

Material | Thickness/mm | Material Surface | Describe |
---|---|---|---|
Cold rolled sheet SPCC | 0.8/1.0/1.5/20/ 2.5/3 0/40/5.0/6.0 | Smooth surface | It is generally used for cold-rolled carbon steel sheet and steel strip, mainly used for electroplating and painting parts, low cost, easy to form. |
Hot rolled plate Q235 | 0.8/1.0/1.5/20/ 2.5/3 0/40/5.0/6.0 | Smooth surface | Also with electroplating, paint parts, low cost, but difficult to form, mainly with flat parts. |
Galvanized sheet SGCC | 0.8/1.0/1.5/20/ 2.5/3 0/40/5.0/6.0 | Smooth surface | The base material is a general cold-rolled steel coil, which becomes a electroplating product after degreasing, pickling, electroplating and various post-treatment processes in the continuous electrogalvanizing production line. |
Stainless steel 201 | 0.8/1.0/1.5/2.0/ 2.5/3.0/4.0/5.0/6.0 | Mist 2B/Brushed/Mirror | Low cost, containing high component manganese to increase ductility, commonly used in industrial use of industrial grade stainless steel, such as iron Windows, iron doors and so on |
Stainless steel 304 | 0.8/1.0/1.5/2.0/2.5/3.0/4.0/5.0/6.0 | Mist 2B/Brushed/Mirror | One of the most widely used stainless steel, because it contains touch, it is richer than steel containing lattice corrosion resistance, heat resistance, with very good mechanical properties, no heat treatment hardening phenomenon, no elasticity. |
Stainless steel 316 | 0.8/1.0/1.5/2.0/2.5/3.0/4.0/5.0/6.0 | Mist 2B/Brushed/Mirror | The high content of the rub makes the corrosion resistance better, more resistant to corrosion, with chloride corrosion resistance, more robust. Mainly used in food industry and surgical equipment, high-priced POTS and pans. |
Aluminum plate 1060H24 | 1.0/1.2/1.5/2.0/2.5/3.0 | Smooth/brushed | It has excellent forming characteristics, high corrosion resistance, good weldability and electrical conductivity. |
Aluminum plate 3003 | 1.0/1.2/1.5/2.0/2.5/3.0 | Smooth/brushed | Formability, welding, corrosion resistance are good, for fabrication needs to have good formability, corrosion resistance and good weldability parts. |
Aluminum plate 5052 | 1.0/1.2/1.5/2.0/2.5/3.0 | Smooth/brushed | It has anti-fatigue strength, high plasticity and corrosion resistance, can not be strengthened by heat treatment, good plasticity when semi-cold hardening, low plasticity when cold hardening, good corrosion resistance, good weldability, poor machinability, and polishing. |
Aluminum plate 6061 | 1.0/1.2/1.5/2.0/2.5/3.0 | Smooth/brushed | Medium strength, good corrosion resistance, weldability, good oxidation effect. It is widely used in various industrial structural parts requiring certain strength, weldability and high corrosion resistance. |
Copper plate H62 | 1.0/1.2/1.5/2.0/2.5/3.0 | Smooth surface | It indicates that ordinary brass with an average copper content of 62% has good mechanical properties, easy plastic fabrication , easy electric control, painting, and can be used for a variety of stressed parts manufactured by deep drawing and bending. |
Challenges of Sheet Metal Cost Estimation
Estimating the cost of sheet metal components can be a complex and time-consuming endeavor with traditional methods involving manual data entry, searching for relevant information, and navigating between different sources to gather accurate data. This process not only consumes valuable time but also increases the risk of human errors that can impact the accuracy of cost estimates.
The manual estimation of production costs for sheet metal components often requires extensive hours. Spreadsheets and ERP systems result in frustration as they require significant time for manual component creation. Additionally, searching for precise data and the identification of hardware components is often the cause of inefficiency, which most often results in missed opportunities. Moreover, the scattered distribution of part details across models, prints, and emails creates confusion and introduces unnecessary risks within your shop’s sheet metal cost estimation process.
Sheet metal cost estimation
Sheet metal cost composition:
Material costs, fabrication costs, standard parts and accessories costs, packaging costs, transportation, tax rates, management fees, profits, etc.
Cost of materials
Net material cost + material loss 10%-20% according to drawing requirements
Material price reference
Material name | Price (Yuan /kg) |
---|---|
Q235 (SPCC) | 6 |
45# plate | 6 |
Stainless steel (304) | 30 |
201 stainless steel plate | 14 |
Mirror stainless steel plate | 25 |
SUS416 stainless steel plate | 40 |
2A11 aluminum sheet | 40 |
6061 aluminum sheet | 30 |
Bakelite (phenolic resin) | 25 |
White polyformaldehyde sheet (POM) | 30 |
Black polyformaldehyde sheet (POM) | 30 |
Polytetrafluoroethylene | 140 |
Process cost
Laser cutting:Calculated according to the actual cutting length of the parts.
Material thickness | Laser (yuan/m) | Punch (yuan/piece) |
---|---|---|
1 | 3 | 0.3 |
1.2-1.5 | 4 | 0.3 |
2 | 5 | 0.3 |
3 | 6 | 0.3 |
4 | 8 | 0.4 |
5 | 10 | 0.5 |
6 | 12 | 0.6 |
8 | 15 | 0.8 |
10 | 18 | 1 |
Numerical control punch
According to the calculation of 200 yuan per hour, the special mold needs to include the mold customization fee of about 1500 yuan -3000 yuan.
Bending
Calculated by hour: 150 yuan/hour. Calculated based on the number of bending blades, as shown in the table below:
Plate thickness | length | price |
---|---|---|
T≤3.0 | L≤600 | 1 |
T≤3.0 | 600<L≤2000 | 2 |
T≤3.0 | 1000<L≤2000 | 6 |
T≤3.0 | 2000<L≤3000 | 10 |
T≤3.0 | L≥3000 | 20 |
tongman
By hour: 50 yuan/hour.
Calculate 0.5 yuan per piece according to the number of sinking hole, pressing riveting, pulling riveting, tapping, reaming and drilling.

weld
By the hour: 80 yuan/hour.
Calculated by length: 25 yuan/meter.
Spray treatment
Indoor powder is calculated at 30 yuan/square meter;
Outdoor powder is calculated at 50 yuan/square meter;
Small parts spraying not less than 1 yuan/piece (less than 0.01 square meters);
Standard parts and accessories fees
For products and parts purchased directly by the company from suppliers, pay attention to adding a 5%-15% agency fee when calculating.
Packing and transportation charge
The packaging costs and transportation costs incurred during the delivery of the product to the customer are determined according to the actual needs of the customer.
Administrative expenses
Expenses incurred by administrative departments for organizing and managing production and business activities account for about 10% of the total price.
profit
The determination of profit rate, according to the difficulty of fabrication technology, batch size, etc., can refer to 15%-25%.
Strategies for Sheet Metal Fabrication Cost Reduction
Cost reduction in sheet metal fabrication is a continual pursuit for businesses aiming to enhance competitiveness and improve their bottom line. Making strategic design choices can indeed wield a positive impact on reducing the final cost of your sheet metal fabrication project. Here are a couple of key considerations:
Use Standard Metal Gauges
Standard sheet metal gauges are helpful since they are easily available and less expensive from manufacturers who normally have them in stock. Non-standard gauges, on the other hand, demand custom orders, thereby lengthening lead times and increasing material costs.
Limit the Use of Tight Tolerances
Tight tolerance sheet metal parts frequently cause fabrication issues, necessitating extra labor and time. This can add significantly to the entire project cost. To mitigate this, use tight tolerances sparingly, such as in holes, bends, and important surfaces. A careful examination of your design can identify possibilities to specify lower tolerances in non-critical areas, thus reducing manufacturing difficulties and cost implications.
Design Simplification
Because of the intricacy needed, such as several cuts, bends, and welds, complex designs tend to be more expensive. While customized design features may be visually appealing, their costs can quickly climb. It is generally best to simplify your design approach. Simple angle bends with inside radii equal to 1x the material thickness can help cut fabrication costs.
The use of tiny bends on large, thick components is less precise and should be avoided. Another technique for improving the cost-effectiveness of the fabrication process is to maintain consistency in bend radii. Furthermore, unless required, avoid integrating features such as blind holes, machined pockets, or chamfered edges, as they can expand lead times and increase manufacturing costs.
Lower-cost finishing option
Choosing the best sheet metal pricing requires taking into account elements such as the part’s application and aesthetic preferences. Pre-plated metals, such as galvanized ones, are appropriate in severe situations.
If you foresee the necessity for welded seams, pre-plated metals such as galvanized may not be the best choice. Finishes such as engraving and silk screening should be saved for the final stages of product creation.
Certain materials are naturally corrosion-resistant, eliminating the need for highly specialized treatments. Choosing such finishes may necessitate additional processes such as seeking external quotations from cost estimators, which may result in higher costs and longer lead times. On the other hand, several conventional finishes, such as chrome plating and powder coating, are both inexpensive and widely available, making them a viable option.
Collaborate with a seasoned professional fabricator
In the intricate world of sheet metal fabrication, collaboration with a seasoned professional fabricator emerges as a strategic avenue for effective cost reduction. Experienced fabricators like Long Sheng excel in process efficiency. They can streamline the fabrication process to reduce production time and fabrication labor costs. This collaborative approach contributes to overall cost-effectiveness. Choosing the right materials is pivotal in cost-effective fabrication. Professional fabricators, with their deep knowledge of material properties, can guide in selecting cost-efficient yet suitable materials for specific applications, ensuring a harmonious balance between performance and affordability.
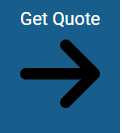
fAQs
How does sheet metal fabrication work?
There are several different ways to shape sheet metal, but they all boil down to two broad categories: sheet metal can either be cut or formed.
As there are many different ways of cutting and forming sheet metal, many specific tooling types are needed which can drive up costs. This is why developing a good understanding of the various sheet metal fabrication processes available is essential to producing the most efficient design for a particular application is essential.
The most basic form of sheet metal fabrication begins with a flat sheet of metal and a blueprint (usually a DXF or CAD file). This blueprint will serve as the instructions on how to cut, form, and finish the base material.
It could be as simple as a single bend to turn it into angle iron, or laser cut and bent at the edges to make computer enclosure panels. When these processes are combined, the material is first cut and later formed, followed by finishing and joining.
what are the Benefits of Metal Fabrication?
Sheet metal fabrication offers many benefits, but the three main benefits are:
- Strong & Durable: When looked after well, metal fabrications can last many years without needing to be replaced, making them great for projects that require long-term durability.
- Versatile: It can be used for a wide range of different-sized projects, making them a valuable asset for many businesses as well as for individuals.
- Easily maintained: Metal fabrications are not susceptible to rust or corrosion and are resistant to fire and heat, making the process great for industrial and commercial settings.
How do material choices impact sheet metal fabrication costs?
The choice of material has a large impact on fabrication costs. Metals differ in terms of cost, strength, and characteristics. Costs may be greater for high-strength alloys or corrosion-resistant metals. Strategic material selection is critical for cost-effectiveness since it balances performance and budget.
What role does design complexity play in fabrication costs?
Design complexity has a direct impact on fabrication costs. More complex designs necessitate expert labor and specialized technology, which contributes to higher labour costs and perhaps longer production timelines. The ability to strike a balance between design complexity and cost is critical for cost-effective fabrication.