In modern manufacturing industry, CNC machining technology has become a common production process, CNC technology makes the error caused by parts production become more stable and accurate. However, it is important to have a detailed understanding of the tolerances of CNC parts, because they are of great importance to the assembly and other aspects of the parts. Tolerances are the acceptable range of dimensions determined by cnc machining manufacturers based on the shape, fit and function of the parts. Understanding how the tolerances of CNC machining affect cost, manufacturing process selection, inspection options, and materials can help you better determine product design.
What are the tolerances of CNC parts?
First of all, we need to figure out what the tolerance of CNC parts is. Tolerance refers to the allowable error range of machining, which is calculated by comparing the measured value of the workpiece with the design value. Process tolerance is the error range that can be reached by the process, which is the problem that must be considered in the formulation of process specification. Design tolerance is the problem that engineers need to consider when designing products, that is, the range of dimensional error specified in the design drawing. Machining tolerance is determined according to machine accuracy and process requirements, which is the sum of machine accuracy and process accuracy.
In CNC machining, tolerances are calculated by comparing the actual size of the workpiece to its design size. The tolerance can be expressed as a positive or negative deviation value, such as +/-0.02 mm. This means that during the machining process, the part size may deviate from the design size by 0.02 mm, and the direction of this deviation may be positive or negative. In the working process, the accuracy of tolerance is also affected by machining temperature, machining speed, tool wear, machining materials and other factors. If the tolerance is beyond the design range, it will affect the normal use and performance of parts. Therefore, special attention should be paid to the control and management of tolerance in the machining process.

CNC part tolerance terms
Here are some terms surrounding CNC parts tolerances that will help improve your understanding and knowledge of CNC manufacturing:
Tolerance zone
The tolerance zone is the range of dimensions that a part should maintain. This range specifies the minimum and maximum allowable deviations, so the dimensions must be controlled within this range.
Surface quality
Surface quality refers to the requirements of surface smoothness and evenness of parts. It generally includes surface roughness, flatness and unevenness and other indicators.
Poisson distribution
Poisson distribution is a probability distribution that describes random processes. Poisson distribution is widely used in CNC manufacturing to describe the relationship between part number and tolerance.
Tolerance value
The tolerance value refers to the difference between the design size and the actual size of the part. This difference can affect the importance and reliability of the parts.
Modified tolerance
A modified tolerance is a tolerance that is usually used to provide a part with higher accuracy within a given tolerance zone. This is determined by the relationship between the actual size of the part and the design size.
Matching level
Match level refers to the difference between a part and other parts. Some parts must fit very closely, while others need enough clearance so that other parts can move within the space.
Tolerance deviation
Tolerance deviation refers to the difference between the actual size of a part and its design size. The tolerance deviation is usually positive or negative, such as +0.5 or -0.5.
Dimensional tolerance
Dimensional tolerance refers to the allowable range of dimensional deviation of a part, usually expressed as tolerance class. Tolerance grade refers to the allowable degree of dimensional deviation, which is generally divided into IT grade and CT grade. The IT rating is for important, high precision parts, while the CT rating is for ordinary, general requirements parts.
clarity
Articulation is a tolerance that describes the ability of an optical or visual device to clearly display the object under test. For CNC manufacturing, articulation is usually used to describe the surface quality or finish of a part.
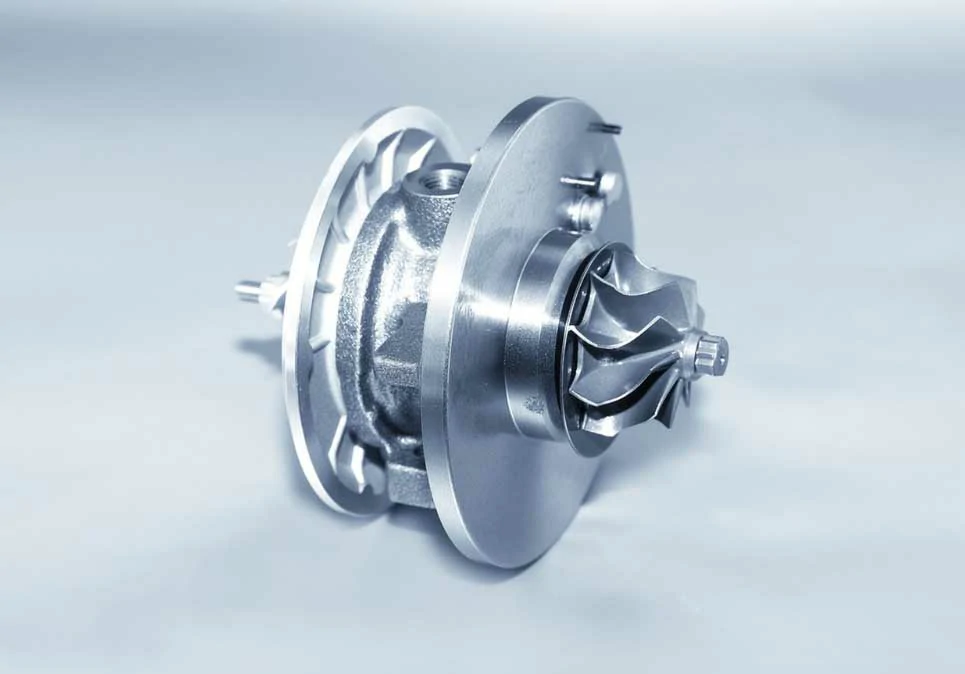
Tolerance of form and position
Form and position tolerance refers to the allowable deviation range of part geometry. It is defined by symbols, where symbols represent geometric requirements, and dimensions/distances, where dimensions/distances represent acceptable deviations.
Rate of qualified products
Qualified product rate refers to the success probability of CNC machining parts reaching the specified tolerance zone in the manufacturing process. This is usually calculated on the basis of the defect rate in the production process.
Strength tolerance
Strength tolerance refers to the allowable deviation range of a part’s strength. It is suitable for high strength, heavy load parts, the tolerance Settings will be based on the part use, design requirements and material characteristics and other factors.
Machining tolerance
Machining tolerance refers to the influence of errors, deviations and other factors on the size and shape of parts during the process of machining from raw materials to final parts. Machining tolerance is unavoidable, but its influence can be reduced by optimizing machining technology and equipment and improving machining accuracy.
Methods for controlling tolerance of CNC parts
Tolerance control of CNC parts is the key to accuracy. Here are some ways to control the tolerance of CNC parts:
Rational design
In the process of parts design, we must consider the machining characteristics of CNC machine tool, reasonable design of the size and shape of the parts. If the design is not reasonable, it is easy to lead to the parts machining accuracy is not high, the tolerance is not stable.
Tighter tolerances can change inspection requirements
Keep in mind that when adding tolerances to parts, consider how features are checked. If features are difficult to process, they are likely to be difficult to measure. Some functions require specialized inspection equipment, which may increase the cost of parts
Correct CNC process parameters
Selecting the correct CNC machining process parameters is very important to control the tolerance of parts. Different materials and tools require different cutting rates, cutting depths and feed rates. Correct parameters will ensure the quality of the parts
Tolerance depends on the material
The difficulty of manufacturing parts to specific tolerances can be very material dependent. In general, the softer the material, the more difficult it is to maintain the specified tolerances because the material bends when cut. Plastics such as nylon, HDPE, and PEEK may not have the same strict tolerances as steel or aluminum without special tool considerations.

Reasonable arrangement of manufacturing sequence
In the process of CNC machining, reasonable manufacturing sequence is also very important to control the tolerance of parts. A proper process sequence will reduce friction between tools and components and reduce the number of tool cleanouts and replacements.
Improve equipment accuracy
In CNC manufacturing, improving the accuracy of equipment can improve the machining accuracy. Check the precision of machining equipment and control the tolerance by adjusting the precision of machining equipment.
Fine measurement
In the process of machining, it is necessary to constantly check the tolerance of the parts and ensure that the tolerance of the parts is within the controllable range through fine measurement. The selection of appropriate measuring tools and methods can ensure that there will be no additional interference and error in the measurement process, so as to obtain reliable measurement results.
How to choose the tolerance value of CNC parts
“When I design CNC parts, how should I choose the tolerance value?” This is a reasonable question, because for accurate CNC engineering, tolerance value is very important, tolerance value is an important parameter to be considered, because if unreasonable selection of tolerance value will lead to the following problems:
1.Reduce the accuracy of mechanical assembly.
2.Reduce the spacing tolerance of geometric features.
3.Raise the cost.
4.It affects the whole system.
Why do you need to consider tolerance values?
The tolerance value refers to the difference between the minimum and maximum allowable values of a part. In other words, the tolerance value is an important index to measure the machining accuracy of a part. In the machining process of CNC parts, the choice of tolerance value directly affects the machining quality and cost of parts. If the tolerance value is too small, it will increase the difficulty and cost of parts machining . If the tolerance value is too large, it will reduce the machining accuracy and service life of parts.
Principle of choice of tolerance value
In the machining process of CNC parts, certain principles are required to select the appropriate tolerance value:
(1) Select tolerances according to the use of parts
Different part types and uses have different requirements on tolerance values, so it is necessary to combine the use of the part to select the tolerance. Such as machine tool parts, automobile parts, aircraft parts, instrument parts and other parts that need high precision, the tolerance value should be relatively small, in order to achieve higher machining accuracy and service life.
(2) Select tolerance according to machining capacity
Different machining equipment and processes have different requirements for tolerance values. Therefore, the precision of machining equipment and the capability of machining process should be considered when choosing the tolerance. For example, in the process of CNC lathe machining , equipment accuracy, machining speed, tool selection, etc., will affect the selection of parts machining quality and tolerance.
(3) Consider tolerance according to cost
The selection of tolerance value also needs to take into account the CNC machining cost of the part. In general, the smaller the tolerance value, the more difficult the machining , the higher the machining cost. Therefore, it is necessary to consider the machining difficulty and cost comprehensively when choosing the tolerance, and select the optimal tolerance value.

How to select tolerance values?
In the process of CNC machining, how to choose the right tolerance value is a complicated problem. Different parts type, machining equipment and technology, machining requirements and so on will affect the choice of tolerance value. The following are some common methods:
(1) Professional software calculates tolerance values
Now there are many professional CNC machining software on the market, according to the shape of the parts, machining requirements and other aspects of the tolerance value calculation. These software can be used for calculation reference when choosing tolerances.
(2) Actual machining experience and test method
In the machining process of CNC parts, practical machining experience and test method are also of great help to the selection of tolerance. Through many times of actual machining and test, the appropriate tolerance value can be determined according to the experience and test results.
(3) Use tolerance values of similar parts for reference
In CNC parts machining , the tolerance value of similar parts is also a good reference. By referring to the tolerance values of similar parts, you can have a general reference when choosing tolerances.
Longsheng Technology hopes that the experience and knowledge provided in this article can help you choose tolerances more reasonably in CNC machining, so as to achieve more accurate and reliable cnc parts online.