Plastic injection molding is a popular manufacturing process used today for a wide range of products. It’s critical to understand the stages involved in this process to ensure that the final product is of high quality and meets your expectations. In this article, we’ll delve into the different stages involved in plastic injection molding, the technologies used, and some tips for ensuring success.
Introduction
Plastic injection molding is the process of shaping plastic materials into different forms and shapes. The process is used to manufacture various industrial and commercial products, including toys, automotive parts, electronic parts, and household appliances. This process is highly efficient, and its high precision and accuracy make it popular in the manufacturing industry.
Plastic Injection Mould Types

1.Low / High Cavitation
Single cavity molds are designed to produce one part per cycle. They are a cost-effective approach when part volumes are low as they are less expensive to build. They also have a shorter lead time. The disadvantage is a higher piece part cost in molding production.
Multi-cavity molds produce more parts per cycle. The major advantages are increased capacity and lower piece part costs as more parts can be produced within a comparable cycle time.
2.Family Mold
A family mold has a single mold base but two or more different cavities, allowing for the production of two or more different parts. All the parts can either be produced simultaneously or shut-offs can be used to isolate production to selected cavities. For best results in molding, the parts should be similar in size, shape, resin, and anticipated volumes, especially if the intention is to run all parts at the same time. Automation may be necessary to separate the pieces during or after production.
3.Unscrewing Molds
Unscrewing molds are the most common method of creating threaded holes within a plastic part. These molds are automated with small drive systems (rack & pinion, electric, or hydraulic motors) that are tied into the process and rotate threaded features to extract undercut features. Threads can be internal or external, and the extraction is tied into the press cycle.
Multi-shot / multi-component tooling allows a product designer to use two or more dissimilar materials on the same part within the same cycle. There may be a variety of reasons why differing materials would be desired, including different physical properties or simply appearance. These molds often utilize multiple manifolds within one tool. Multi-shot tooling can be an elegant solution for complicated products, and can be used for color changes within a product line.
Specialized presses and molds are necessary to run multi-shot tooling. Multiple machine nozzles, hot runner systems and mold rotation may become necessary. While Matrix currently does not have any multi-shot molding presses on our floor, we are particularly adept at designing and building these complicated tools and have been doing so for decades.
4.Hot Runner Molds
Hot runner tools use a temperature-controlled manifold to greatly reduce or eliminate runner scrap from the cycle. Injection points can be outside the part or directly into the part. This can greatly improve cycle times, as a sprue or runner system is often a determining factor on the mold cycle. And, eliminating the runner saves expensive wasted material.
Hot runner molds require a temperature controller for the press they run in, with the controller being sized to match the manifold in the mold. Some mold maintenance costs are higher on a hot runner tool, but they often pay for themselves in the long run through material and cycle time savings. This is particularly true of applications that require expensive engineering grade resins or high annual volumes.
5.Cold Runner Molds
Cold runner molds are good examples of more traditional tooling in that they utilize sprues and runners to gate into the part. This is typically the least complicated form, however may result in larger amounts of wasted material and slower running cycles. Depending on the application, a percentage of wasted material may be re-ground and re-processed for future use, though this could affect the physical properties of the resin.
Dealing with more advanced, high-cost materials such as engineering and medical grade resins or the inability to use regrind in your application may lend itself to using a more efficient hot runner mold for your project.
What are the Uses of Plastic Injection Molding?
Plastic injection molding is used in all industries for applications from static-dissipating electronics housings to self-lubricating parts in the oil and gas industry. Some of the most common applications include:

- Consumer products: commonly utilizing inexpensive, mechanically strong plastics like PVC, this industry uses injection molding for handheld items, storage containers, and IoT containers.
- Aerospace:companies use products like turbine housings and blades, pump gears, and valve seats, made from engineering plastics such as PEEK and PAI, both of which can handle wide ranges of temperatures seen by aircraft.
- Electronics: in this field injection molded parts include many over molded components like wire cables and connectors. Materials used commonly include static dissipation plastics like ABS and ABS blends.
- Medical manufacturers:use injection molding for product parts found in medical tools, light or monitor support arms, infusion pumps, EKG machines, and tomographic imaging machines. Medical companies will utilize plastics that don’t absorb moisture and that can be sterilized via steam, radiation, or gas. Some plastics needed will also have clarity requirements for transparent parts. Commonly used plastics include PEEK, polycarbonate, and polystyrene, though not Nylon, as it absorbs moisture.
- Energy and oil:companies utilize high temperature resistant plastics with little to no moisture absorption. This includes PEEK, which is neutral with high temperature resistance, PTFE, which has high heat deflection properties. They also commonly use nylons, which are self-lubricating and can withstand a wide range of temperatures. These companies require products like insert molded valves, electrical connectors, seals, pipe protection and liners, and other parts.
- Automotive: since vehicles can end up in an array of climates and operating conditions, automotive companies will use materials with a wide range of chemical and temperature resistance. Parts, including door panels and engine components, will often be manufactured with glass-filled nylon, as the glass adds stiffness for products like bumpers. Other popular materials include PBT, PPE-PS, and polyether imide, which has high chemical resistance.
What are Plastic Injection Molding Prototypes?
Injection molding prototypes are cheaply produced, relatively short run groups of dozens of injection molded products created in design, testing, and development stages for testing and promotion. More specifically, a company will want to create prototypes to:
- Prove a part design will work using this method specifically
- Ensure the final part that will be injection molded will come out without material or tooling-based design problems
- Use in consumer research or for promotion
- Test the parts, including figuring out cosmetics
- Demonstrate the part to potential distributors
- Getting a specific material or finish that isn’t achievable using other ways, such as creating polystyrene parts (which can’t be printed)
However, some part types are best prototyped first. Companies creating small products like contact lens cases that will have many holes in a multicavity mold later will find prototyping more helpful before investing in molds with dozens of cavities. Additionally, companies with large amounts of regulation when creating parts at scale (such as those in the medical sector) use injection mold prototyping to create parts for research without having to go through the regulations and certifications processes required for products to be used on consumers. This allows them to avoid costly mistakes after having gone through the approval processes.
Generally prototyped parts will be made from commodity plastics, like polycarbonate, nylon, polypropylene, and ABS , as well as elastomers like TPE, TPU, and SAN. Some resins require specialty molds as well. PEEK, for example, requires a heated mold instead of the more standard cooling mold, which only dissipates heat from liquid plastic instead of adding heat at first to keep it liquid.
Stages in plastic injection molding
The injection molding process mainly includes six stages: mold closing, filling, pressure holding, cooling, mold opening, and demolding.
These six stages directly determine the molding quality of the product, and these six stages are a complete continuous process. This chapter focuses on the four stages of filling, pressure holding, cooling, and demolding.

1.filling
Filling is the first step in the entire injection molding cycle. The time starts from the mold closing and injection molding until the mold cavity is filled to about 95%. In theory, the shorter the filling time, the higher the molding efficiency; but in actual production, the molding time (or injection speed) is subject to many conditions.
- High-speed filling When the shear rate is high during high-speed filling, the plastic has a decrease in viscosity due to the shear thinning effect, which reduces the overall flow resistance; the local viscous heating effect will also make the solidified layer thinner. Therefore, in the flow control stage, the filling behavior often depends on the volume to be filled. That is, in the flow control stage, due to high-speed filling, the shear thinning effect of the melt is often large, and the cooling effect of the thin wall is not obvious, so the rate effect prevails.
- Low-speed filling When heat conduction controls low-speed filling, the shear rate is low, the local viscosity is high, and the flow resistance is large. Since the hot plastic replenishment rate is slow and the flow is slow, the heat conduction effect is more obvious, and the heat is quickly taken away by the cold mold wall. In addition, due to the small amount of viscous heating phenomenon, the thickness of the solidified layer is thicker, which further increases the flow resistance at the thinner wall.
2.Holding pressure
The function of the holding pressure stage is to continuously apply pressure, compact the melt, increase the density of the plastic (densification), and compensate for the shrinkage behavior of the plastic. During the holding pressure process, the back pressure is high because the mold cavity is already filled with plastic. During the holding pressure compaction process, the injection molding machine screw can only move forward slowly and slightly, and the flow speed of the plastic is also relatively slow. The flow at this time is called holding pressure flow. Because in the holding pressure stage, the plastic is cooled and solidified faster by the mold wall, and the melt viscosity increases rapidly, so the resistance in the mold cavity is very large. In the later stage of holding pressure, the material density continues to increase, and the plastic part is gradually formed. The holding pressure stage should continue until the gate is solidified and sealed. At this time, the mold cavity pressure in the holding pressure stage reaches the highest value.
During the pressure holding stage, due to the high pressure, the plastic exhibits partial compressibility. In areas with high pressure, plastic is denser and has a higher density; In areas with lower pressure, plastic is looser and has lower density, so the density distribution varies with position and time. During the pressure holding process, the plastic flow rate is extremely low, and the flow no longer plays a dominant role; Pressure is the main factor affecting the pressure holding process. During the pressure holding process, the plastic has filled the mold cavity, and the gradually solidified melt serves as the medium for transmitting pressure. The pressure inside the mold cavity is transmitted to the mold wall through plastic, which has a tendency to open the mold. Therefore, appropriate locking force is needed for mold locking. Under normal circumstances, the expanding force will slightly open the mold, which is beneficial for the exhaust of the mold; But if the expansion force is too large, it is easy to cause burrs, overflow, and even mold opening in the formed product. Therefore, when choosing an injection molding machine, it is important to choose one with sufficient locking force to prevent mold expansion and effective pressure retention.
3.Cooling
In the injection molding mold, the design of the cooling system is very important. This is because the molded plastic products can only avoid deformation due to external forces after cooling and solidification to a certain rigidity and demolding. Since the cooling time accounts for about 70% to 80% of the entire molding cycle, a well-designed cooling system can greatly shorten the molding time, improve injection molding productivity, and reduce costs. An improperly designed cooling system will prolong the molding time and increase costs; uneven cooling will further cause warping and deformation of plastic products.
According to experiments, the heat entering the mold from the melt is generally dissipated in two parts, 5% of which is transferred to the atmosphere through radiation and convection, and the remaining 95% is conducted from the melt to the mold. Due to the effect of the cooling water pipe in the mold, the heat of the plastic product is transferred from the plastic in the mold cavity to the cooling water pipe through the mold frame through heat conduction, and then carried away by the coolant through heat convection. A small amount of heat that is not carried away by the cooling water continues to be conducted in the mold, and dissipates into the air after contacting the outside world.
Factors affecting the cooling rate of products are:
Plastic product design | Mainly the wall thickness of plastic products. The thicker the product, the longer the cooling time |
Mold materials and their cooling methods | Mold materials, including mold core, cavity materials and mold frame materials, have a great influence on the cooling rate. The higher the thermal conductivity coefficient of the mold material, the better the effect of transferring heat from the plastic per unit time, and the shorter the cooling time |
Cooling water pipe configuration method | The closer the cooling water pipe is to the mold cavity, the larger the pipe diameter and quantity, the better the cooling effect and the shorter the cooling time |
Coolant flow rate | The greater the cooling water flow (generally, turbulence is the best), the better the cooling water will take away heat by convection |
Coolant properties | The viscosity and thermal conductivity of the coolant will also affect the heat conduction effect of the mold. The lower the viscosity of the coolant, the higher the thermal conductivity, the lower the temperature, and the better the cooling effect |
Plastic selection | Plastic refers to the measurement of the speed at which the plastic conducts heat from a hot place to a cold place. The higher the thermal conductivity of the plastic, the better the heat conduction effect, or the plastic has a low specific heat and the temperature is easy to change, so the heat is easy to dissipate, the heat conduction effect is better, and the required cooling time is shorter |
Processing parameter setting | The higher the material temperature, the higher the mold temperature, the lower the ejection temperature, and the longer the required cooling time. |
Cooling system design rules:
The designed cooling channel must ensure uniform and rapid cooling.
The purpose of designing a cooling system is to maintain proper and efficient cooling of the mold. Cooling holes should use standard sizes to facilitate processing and assembly.
When designing the cooling system, the mold designer must determine the following design parameters based on the wall thickness and volume of the plastic part – the location and size of the cooling hole, the length of the hole, the type of hole, the configuration and connection of the hole, and the flow rate and heat transfer properties of the coolant.
4.Demolding
Demolding is the last step in an injection molding cycle. Although the product has been cold-formed, demolding still has a great impact on the quality of the product. Improper demolding methods may cause uneven force on the product during demolding, deformation of the product during ejection, and other defects. There are two main ways of demolding: ejector demolding and stripper demolding. When designing a mold, it is necessary to select a suitable demolding method according to the structural characteristics of the product to ensure product quality.
For molds that use ejector demolding, the ejector should be set as evenly as possible, and the position should be selected where the demolding resistance is the largest and the strength and rigidity of the plastic part are the largest, so as to avoid deformation and damage to the plastic part.
The stripper plate is generally used for the demolding of deep-cavity thin-walled containers and transparent products that do not allow push rod marks. The characteristics of this mechanism are large and uniform demolding force, smooth movement, and no obvious residual marks.
parameters of plastic injecting molding stage
temperature
The temperature to be controlled in the injection molding process is mainly barrel temperature, nozzle temperature, and mold temperature.
Barrel temperature | Nozzle temperature | Mold temperature |
---|---|---|
The choice of barrel temperature is related to the variety and characteristics of plastic materials. If the barrel temperature is too low, the plasticization will not be sufficient; if the barrel temperature is too high, the plastic may be overheated and decomposed. The temperature distribution of the material is generally based on the principle of high front and low back, i.e., the temperature at the back end of the barrel is low and the temperature at the front end near the nozzle is high to prevent degradation of the plastic due to sheer friction heat. | Nozzle temperature is generally slightly lower than the maximum temperature of the barrel, to prevent the temperature from being too high to melt in the nozzle salivation phenomenon. | Mold temperature has a great influence on the flow of the melt, cooling rate, and the performance of the molded part. The temperature of the mold depends on the crystallinity of the plastic, the size of the molded part, and the performance of the molded part. Structure and performance requirements and other process conditions (such as melt temperature, injection speed, and injection pressure). |
pressure
The injection pressure is provided by the hydraulic system of the injection molding system. The pressure of the hydraulic cylinder is transmitted to the plastic melt through the screw of the injection molding machine. Under the pressure, the plastic melt enters the vertical flow channel (also the main flow channel for some molds), the main flow channel, the branch flow channel of the mold through the nozzle of the injection molding machine, and enters the mold cavity through the gate. This process is the injection molding process, or the filling process. The existence of pressure is to overcome the resistance in the flow process of the melt, or conversely, the resistance in the flow process needs to be offset by the pressure of the injection molding machine to ensure the smooth progress of the filling process.
There are many factors that affect the melt filling pressure, which can be summarized into three categories:
Material factor | Structual factor | Forming process elements |
---|---|---|
type of plastic | type,number and position of gating system | / |
viscosity of plastic | shape of the mold cavity | / |
thickness of the product | / |
time
The time required to complete an injection molding process is called the molding cycle. It includes mold filling time, holding time, in-mold cooling time, other times, etc. Other times include mold opening, mold release, mold release agent application, insert placement and mold closing, etc.
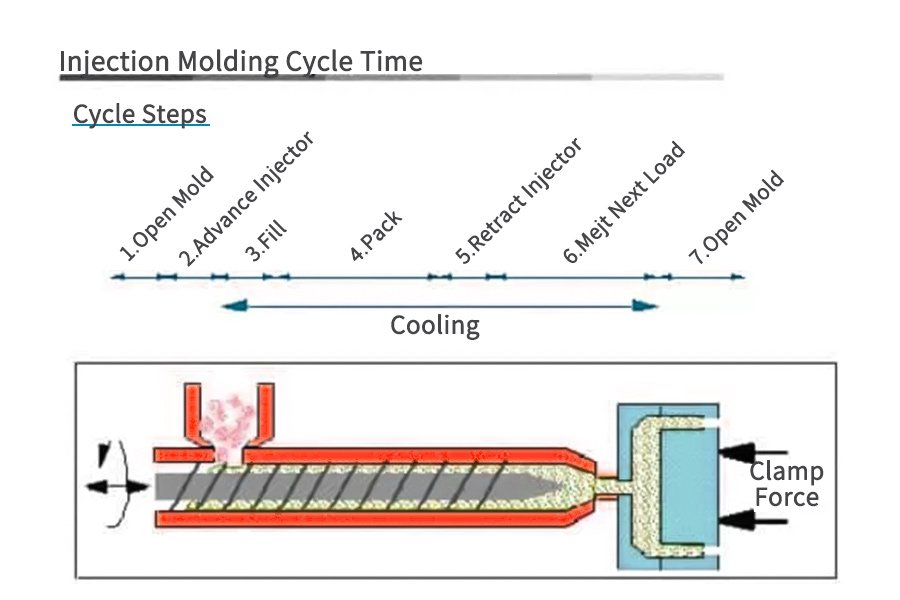
power
The power required for this process of injection moulding depends on many things and varies between materials used. Manufacturing Processes Reference Guide states that the power requirements depend on “a material’s specific gravity, melting point, thermal conductivity, part size, and molding rate.” Below is a table from page 243 of the same reference as previously mentioned that best illustrates the characteristics relevant to the power required for the most commonly used materials.
Material | Specific gravity | Melting point(°F) | Melting point(°C) |
---|---|---|---|
Epoxy | 1.12 to 1.24 | 248 | 120 |
Phenolic | 1.34 to 1.95 | 248 | 120 |
Nylon | 1.01 to 1.15 | 381 to 509 | 194 to 265 |
Polyethylene | 0.91 to 0.965 | 230 to 243 | 110 to 117 |
Polystyrene | 1.04 to 1.07 | 338 | 170 |
Process troubleshooting
Like all industrial processes, injection molding can produce flawed parts, even in toys. In the field of injection moulding, troubleshooting is often performed by examining defective parts for specific defects and addressing these defects with the design of the mould or the characteristics of the process itself. Trials are often performed before full production runs in an effort to predict defects and determine the appropriate specifications to use in the injection process.

When filling a new or unfamiliar mould for the first time, where shot size for that mould is unknown, a technician/tool setter may perform a trial run before a full production run. They start with a small shot weight and fills gradually until the mould is 95 to 99% full. Once they achieve this, they apply a small amount of holding pressure and increase holding time until gate freeze off (solidification time) has occurred. Gate freeze off time can be determined by increasing the hold time, and then weighing the part. When the weight of the part does not change, the gate has frozen and no more material is injected into the part. Gate solidification time is important, as this determines cycle time and the quality and consistency of the product, which itself is an important issue in the economics of the production process. Holding pressure is increased until the parts are free of sinks and part weight has been achieved.
Conclusion
Plastic injection molding is a complicated process that requires proper planning and execution. This process involves the preparation of the material, designing, and preparing the mold, injecting the material, waiting for the material to cool, ejecting the part, and finishing. By following best practices and choosing the right technology, you’ll easily get high-quality products with thermoplastic injection molding.
FAQs
Is 3D Printing the Same as Plastic Injection Molding?
No, 3D printing is a separate set of processes from injection molding. With 3D printing, the material is deposited in a layer-by-layer process guided by a 3D model of the desired part. With injection molding, molten plastic is injected into a mold cavity under high pressure, creating a part all at once. Both processes are considered to be “Additive Manufacturing”.
In Plastic Injection Molding, plastic injection molds come out with suitable surface quality and are essentially ready for application (with only sprues, runners, gates, and minor defects to manage). Thermoplastics are generally the preferred material used in injection molding, though newer injection molding processes can accept thermosets, impregnated materials, some metal powders, and some types of ceramics.
What Is the Difference Between 3D Printing and Injection Molding?
Below is a list of comparisons between 3D Printing and Injection molding using key metrics:
Parameter | Injection Molding | 3D printing |
---|---|---|
Materials | Thermoplastics, some specialty materials in newer machines | Thermoplastics, thermosets, metals, ceramic, impregnated materials |
Cost | High initial investment cost, low cost per-part | Medium to high initial investment cost, medium to high cost per part |
Part size | Highly variable (both very small and large parts possible) | Restricted by build space, parts are generally no bigger than a cubic meter |
Waste | Low/no waste, and waste can be reground back into stock | High waste output |
Design changes | Difficult, changes are slow | Very easy, rapid changes possible |