Milling is a type of subtractive manufacturing that involves cutting fixed flat surfaces using rotating tools. climb milling and conventional milling are the two main methods machinists use to mill parts. However, choosing between them is often difficult as both have advantages and disadvantages.
In this guide, we look at what conventional milling and climb milling are and their characteristics, the differences between conventional milling and climb milling, and we also provide factors to consider when choosing between them in the milling process to help you make the right decision.
What is climb milling?
Climb milling, also referred to as down milling, is a machining process in which the cutter and the workpiece move in the same direction during cutting. This results in the chip starting thick and thinning out. This technique aligns the cutter rotation with the feed direction which can improve surface finish and extend tool life due to the reduced heat from thinner chips. However, it requires a stable setup to handle the pulling forces that might otherwise displace the workpiece.
Features of climb milling
In climb milling, the chip thickness starts at zero and gradually increases as the tooth rotates until the end of the cut. The tooth does not immediately engage the workpiece; instead, it slips on the machined surface. This slipping hardens the surface, reducing its quality and accelerating tooth wear.
What Is Conventional Milling?
As its name suggests, the conventional milling process is the traditional approach where the cutting tool rotation is against the movement of the workpiece. In this case, the cut is in the upwards direction, that’s why this milling technique is also called up milling.The conventional milling process is entirely the opposite of climb milling. In this case, the chip width starts from virtually zero and gradually increases. Furthermore, the chips evacuate in the path of the cutter because of its rotation, and the workpiece experiences an uplifting force because of the cutting action.
Features of conventional milling
In conventional milling, the chip thickness gradually decreases from the beginning of the cut until it reaches zero at the end of the cut. This frictionless characteristic prevents the cutting edge from scraping and rubbing against the part surface before the actual cut begins. Additionally, since the chips go from thick to thin during conventional milling, burrs are less likely to form when machining ductile materials.
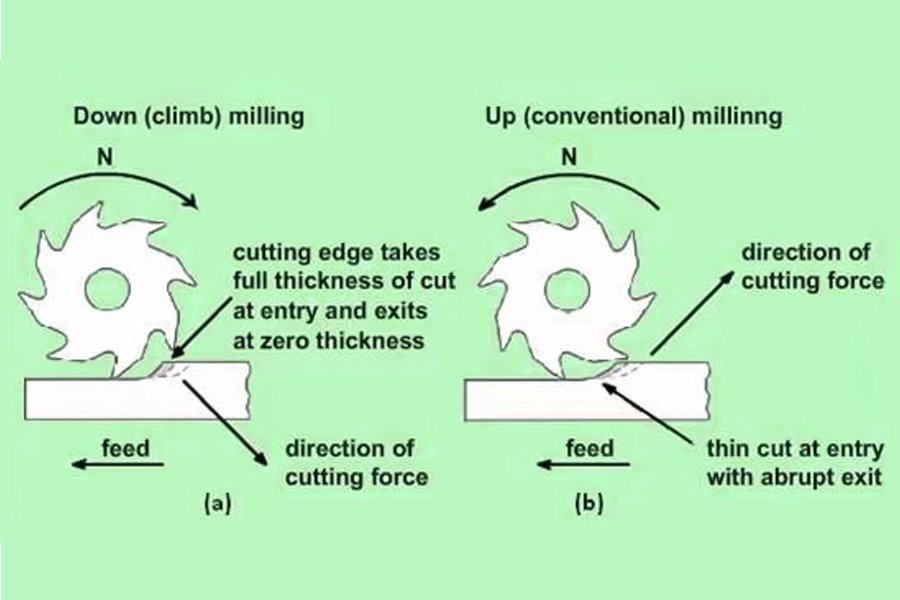
Advantages and disadvantages of climb milling
Advantages
Climb milling offers several notable advantages in machining, such as:
- Small cutting load: During climb milling, the component of the force exerted by the milling cutter on the workpiece in the feed direction is the same as the feed direction of the workpiece, which makes the cutting load relatively small, reduces the wear of the machine tool and the tool, and also reduces the load on the entire operating system.
- Good surface quality: Since the cutting force of climb milling is small and the damage to the surface of the workpiece is also very slight, it can process a higher-precision surface and is suitable for processing tasks that require high surface quality.
- High machine tool utilization: During climb milling, the milling direction is consistent with the milling cutter axis, which can maximize the effective working range of the milling machine table and improve the machine tool utilization.
- Low power consumption: Under the same cutting conditions, the power consumption of climb milling is smaller than that of conventional milling, usually 5% to 15% lower, which makes the processing process more energy-saving.
- Slow tool wear: During climb milling, the cutting changes from thick to thin, and the cutter teeth cut into the unmachined surface, which is beneficial to reducing tool wear and improving tool durability.
disadvantages
Climb milling, despite its advantages, also has several disadvantages that need to be considered, including:
- Limited processing depth: Due to the different locations where cutting forces act, the processing depth of climb milling is generally limited, making it difficult to complete ultra-deep processing.
- Relatively low processing efficiency: Since the load of climb milling is small during milling, its processing efficiency is also relatively low, and it is not suitable for processing tasks that require high processing efficiency.
- Possible tearing and burrs: Due to uneven extrusion processing, the process of climb milling sometimes results in more tears and burrs in the cutting area, affecting the processing quality.
- High requirements on the shape and structure of the workpiece: In climb milling, cutting is performed on the workpiece, so more tools and equipment are required to ensure that the shape and structure of the workpiece are not destroyed.

Advantages and disadvantages of conventional milling
Advantages
Conventional milling offers several advantages that make it suitable for specific machining contexts, such as:
- The width of the chip starts from zero and increases as the cutting tool finishes slicing with conventional milling.
- The cutting edge meets the workpiece at the bottom of the cut when conventional milling.
- Upward forces tend to lift the workpiece during conventional milling.
- Conventional milling requires more power than climb milling.
- Surface finish is worse because chips are carried upward by teeth and dropped in front of cutting tool. There’s a lot of chip recutting with conventional milling. Flood cooling can help!
- Conventional milling is preferred for rough surfaces.
- Tool deflection during conventional milling will tend to be parallel to the cut.
disadvantages
Conventional milling, or up milling, has several disadvantages that may affect its efficiency and effectiveness in certain machining applications, including:
- Unsmooth Finish:The upward cutting used in this process makes achieving a smooth finish difficult. This is due to the number of deflections experienced by the workpiece and cutting tool, resulting in a rougher surface.However, this deflection rate also makes conventional milling ideal for machining harder materials such as steel and cast iron.
- Process Generates Excessive Heat:Another downside to conventional milling is the heat generated during the process. This heat generated is because chip formation here is gradual, often resulting in cutting tool overheating. A consequence of cutting tool overheating is a reduction in its life span.
- Tool Damage:Frictional and upward forces generated during conventional milling often produce excessive heat. Also, with excessive heat, the tool suffers damage, reducing its lifespan, precision, and accuracy of the workpiece.
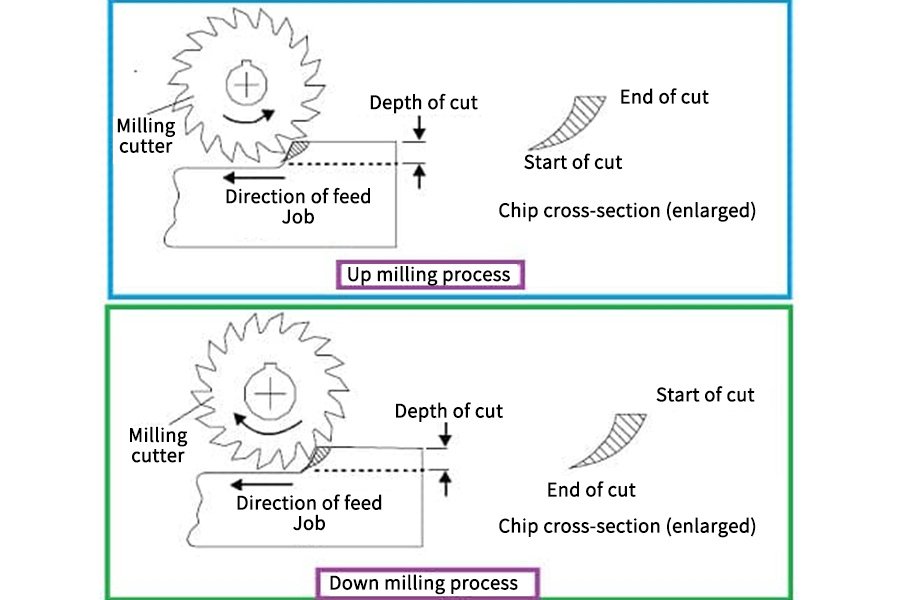
What are the applications of climb milling and conventional milling?
- Climb milling is mainly used for rough machining, including material removal, shape processing and surface burr removal. Due to its fast milling speed, it is suitable for high-volume processing, such as cutting machine tools, lathes and other common processing methods in the metal processing industry.
- conventional milling is mainly used for fine processing and is suitable for industrial parts that require high precision, such as optical instruments, precision molds and other fields. Due to its slow milling speed, it is suitable for precision machining of small batches.
What is the difference between climb milling and conventional milling
Climb milling and conventional milling are two types of milling that differ in the direction of the cutting tool’s rotation relative to the direction of the workpiece’s movement.
In climb milling, the cutting tool rotates in the same direction as the workpiece’s movement, which allows the chips to be lifted away from the workpiece and results in a smoother surface finish. Climb milling also generates less heat and results in longer tool life. However, climb milling can result in more cutting forces and has a higher tendency for tool deflection.
In conventional milling, the cutting tool rotates in the opposite direction of the workpiece’s movement, resulting in a tendency for the chips to be pushed into the workpiece and resulting in a rougher surface finish. Conventional milling generates more heat and results in shorter tool life, but it has a lower tendency for tool deflection and produces fewer cutting forces.
Comparison of Climb Milling and conventional milling
Let’s compare the conventional and climb milling processes in different aspects, such as their capacity, cutting tool, surface finish, and many more.
Criteria for Comparison | Description |
Cutting force | In Conventional milling, cutting force gradually increases from the initial contact of the Cutter and workpiece to the exit point. While it gradually decreases in the case of climb milling. In addition, Climb milling requires less cutting force than conventional. |
Chip thickness | Conventional milling involves a progressive rise in chip thickness from the initial contact between the Cutter and the workpiece to the exit point. While in the case of climb milling, it gradually decreases. |
Chip-direction | Conventional milling involves leaving the chip in front of the tool. Climb milling leaves in the cutter path. |
Drag | In climb milling, the workpiece is dragged in the cutter direction due to feeding in the same order. On the other hand, conventional milling pushes the workpiece away. |
Friction & Heat | Conventional milling produces greater friction due to its high cutting force than climb milling. Heat generation occurs similarly because friction and heat generation are proportional. |
Tool life | Excessive heat, vibration, and high cutting force of conventional milling cause more wear and tear on the Cutter than climb milling. Therefore, the tool has more life with climb milling. |
Tool deflection | Tool deflects parallel with cut in conventional milling & perpendicular in climb mill. The parallel deflection implies a low risk of undesirable cuts. |
Surface finish | Climb milling offers smoother as-machine surface finishing. The re-cutting of chips and high cutting force results in a poor finish with conventional milling. |
How to distinguish between Conventional Milling and Climb Milling?
Be the truth that most people had mistaken climbing milling as the Spindle forward and reverse rotation on CNC milling machine panel, that is, the spindle rotates forward to realize climbing milling, and rotates backward to complete conventional milling. In fact, the forward and reverse rotation of the spindle is affected by the rotation of the tool (not directly related to conventional milling and climb milling). To fully understand conventional milling and climb milling, it is necessary to understand the direction of rotation and the direction of feed.
① The rotation direction of the milling cutter. On the CNC milling machine, the forward and reverse rotation of the spindle can be realized through commands or buttons. The forward and reverse rotation of the spindle is limited by the rotation direction of the milling cutter. Instead of the forward rotation of the spindle, it is climb milling, and vice versa. For example, for general end mills, since most of them are right-handed, the spindle can only rotate forward; as for left-handed thread cutters and right-handed thread cutters, the spindle rotates in reverse and forward directions.
② Feed direction. Since the milling cutter is rotating, the feed direction must be defined clockwise and counterclockwise. Looking along the feed direction of the tool, the tool is on the left side of the workpiece, then the feed direction is called clockwise. Conversely, when the tool is on the right side of the workpiece, the feed direction is defined as counterclockwise.
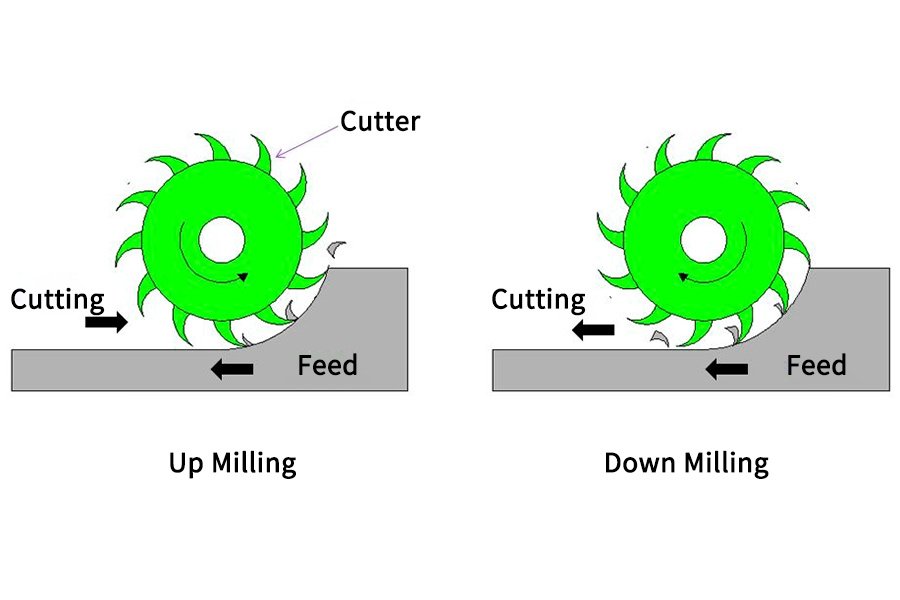
How to Choose the Right Milling Approach?
Selecting one milling approach from conventional & Climb is a complicated phenomenon. It needs to consider various factors, such as material type, required specification, accuracy, etc.
Facing:The facing demands a burr-free, smooth surface finish. Therefore, it is recommended to utilize climb milling. Climb milling includes forcing the chips onto the center.
High accuracy:Conventional milling is suitable for accurate milling. The deflection occurs parallel to the feed, which causes the minimum impact on accuracy. In addition, it also gives more control over possible errors.
Smooth finish:Climb milling is preferable. It prevents the re-cutting, and the lower cutting force offers a more smooth finish.
Hard material:Conventional milling is an accurate option for hard material, and climb milling can affect the tool while working with hard material.
Size of workpiece:Large workpieces, blocks, and bars are better suited for conventional milling. At the same time, climb milling is the best option for small parts that require a high-quality finish.

Longsheng’s custom CNC milling services
One way to ensure consistent CNC machining results is to combine the right tools with the right experience. That’s why it’s important to outsource your upper and lower milling projects to a reputable manufacturing company.Longsheng is an ISO 9001 certified manufacturing company with an experienced team of engineers providing custom CNC milling services for a variety of materials including metals, plastics and other composites.
Equipped with 3, 4 and 5-axis CNC milling capabilities, we are able to produce a wide range of parts with high precision, regardless of geometric complexity. From single products to low-volume part production, we are committed to providing cost-effective milling solutions. At Longsheng, we also provide part finishing services for your CNC machining projects, ensuring high quality parts.Simply upload your CAD file and we will analyze your design and send you a quote within 24 hours. sounds good. So contact us today for your CNC milling project.

conclusion
Climb milling vs. conventional milling is a long-standing debate between experienced and novice machinists. However, both processes have their outstanding advantages and disadvantages.In this article, we discuss the differences between these technologies as well as the advantages and disadvantages so that you can make an informed decision about which one is best for your project.
FAQs
When should you use milling?
Milling should be used when high precision, high efficiency and complex shape processing are required. At the same time, milling processing has broad application prospects in machinery manufacturing, automobile industry, aerospace and other fields.
Why is down milling also called climb milling?
Climb milling is called climb milling because when milling with this technique, the milling cutter teeth move down the surface of the workpiece. This way, chips are deposited behind the mill while reducing the incidence of recuts.
What are the applicable scenarios for conventional milling?
Conventional milling is mainly suitable for situations where the machining roughness is acceptable, chips are easy to clean, the tool has a high endurance, rough machining and rough milling operations, and specific high-precision machining requirements. In practical applications, the appropriate processing method should be selected based on the specific characteristics and processing requirements of the workpiece.
Which one has better surface finish between climb milling and conventional milling?
Climb milling usually results in a better surface finish. This is because the workpiece is under pressure during climb milling, the cutting method is conducive to reducing vibration and damage, the tool wear is small, and the table feed clearance has a relatively small impact on the surface finish.However, this does not mean that conventional milling cannot achieve a good surface finish in all cases. In some specific cases, such as when machining soft materials, conventional milling may result in a better finish than climb milling due to differences in cutting force distribution.Therefore, in practical applications, the choice of climb milling or conventional milling should be comprehensively considered based on factors such as workpiece material, processing requirements, and machine tool characteristics.