CNC machining is an incredible manufacturing process that utilizes computer-controlled machines to fabricate a wide range of products. From industrial components to consumer goods and medical devices, CNC machining can create high-quality, precise components for various industries. The process involves using a computer-aided design (CAD) software to generate a design, which is then converted into a code that the CNC machine can read. The machine then removes material from a workpiece to create the desired shape and size.
One of the most significant advantages of CNC machining is its versatility in cutting a variety of materials. Here are some of the materials that CNC machining can cut:

1. Metals
CNC machining can cut a variety of metals, including aluminum, brass, copper, stainless steel, and titanium. These materials are widely used in various industries like aerospace, automotive, and medical industries. The precision and high quality of the cuts make them perfect for manufacturing complex components for these industries.
Aluminum 6061
This is the most common general purpose aluminum used for CNC machining. The main alloying elements are magnesium, silicon, and iron. Like all aluminum alloys it has a good strength-to-weight ratio and is naturally resistant to atmospheric corrosion. Other advantages of this material are that it has good workability and CNC machinability, can be welded and anodized, and its wide availability means that it’s economical.
When heat-treated to a T6 temper, 6061 has a considerably higher yield strength than annealed 6061, although the price is slightly higher. One of the drawbacks to 6061 is poor corrosion resistance when exposed to salt water or other chemicals. It’s also not as strong as other aluminum alloys for more demanding applications.
Aluminum 7075
7075 is a higher grade of aluminum, alloyed mainly with zinc. It’s one of the strongest aluminum alloys used in machining, with excellent strength-to-weight characteristics.
Because of the strength of this material it has average workability which means it tends to spring back to its original shape when being cold-formed. 7075 is also machinable and can be anodized.
brass
Brass is an alloy of copper and zinc. It’s a very soft metal, and can often be machined without lubrication. It’s a material that’s also highly workable at room temperature, so it often finds applications that doesn’t require great strength. There are many kinds of brass, largely depending on the percentage of zinc. As this percentage increases, corrosion resistance decreases.

Brass mallets are dense, non-sparking and soft.
Brass takes a high polish that looks much like gold. This is the reason it’s often found in cosmetic applications. Brass is electrically conductive but non-magnetic, and can be easily recycled.
Brass can be welded but is most often joined with low-temperature processes like brazing or soldering. Another feature of brass is that it doesn’t spark when struck with another metal, so it finds use for tools in potentially explosive environments. Interestingly, brass has natural anti-bacterial and anti-microbial properties, and its use in this regard is still being studied.
Brass is common in plumbing fittings, home decorative hardware, zippers, naval hardware, and musical instruments.
Magnesium AZ31
The body of this camera was pressure die cast with magnesium.
Magnesium is a material that’s easy to machine but it’s very flammable especially in powder form, so it must be machined with a liquid lubricant. Magnesium can be anodized to improve its corrosion resistance. It’s also highly stable as a structural material and is an excellent choice for pressure die casting.
Magnesium AZ31 is often used for aircraft components in which light weight and high strength are most desirable, and can also be found in the housings for power tools, laptop cases and camera bodies.
Stainless Steel 303

There are many varieties of stainless steel, so called because of the addition of chromium that helps to deter oxidation (rust). Because all stainless steels look alike, great care must be taken to test incoming raw material with modern metrology equipment like OES detectors to confirm the characteristics of the steel you’re using for machining.
In the case of 303, sulfur is also added. This sulfur helps to make 303 the most readily machined stainless steel, but it also tends to reduce its corrosion protection somewhat.
303 isn’t a good choice for cold forming (bending), nor can it be heat treated. The presence of sulfur also means it’s not a good candidate for welding. It does have excellent machining properties but care must be taken with speeds/feeds and the sharpness of cutting tools.
303 is often used for stainless nuts and bolts, fitting, shafts, and gears. It should not, however, be used for marine grade fittings.
Stainless Steel 304

This is the most common form of stainless steel found in a wide variety of consumer and industrial products. Often called 18/8, this refers to the addition of 18% chromium and 8% nickel to the alloy. These two elements also make this machining material especially tough and non-magnetic.
304 is a material that is readily machineable, yet unlike 303 it can be welded. It’s also more corrosion resistant in most normal (non-chemical) environments. For machinists, it should be processed with very sharp cutting tools, and not contaminated with other metals.
Screws, nuts and other attachment hardware is often made from 304 stainless.
Stainless Steel 304 is an excellent material choice for kitchen accessories and cutlery, tanks, and pipes used in industry, architecture, and automotive trim.
Stainless Steel 316
The addition of molybdenum makes 316 even more corrosion resistant, so it’s often considered a marine-grade stainless steel. It’s also tough, and easy to weld.
316 stainless was used to make this shackle for a boat.
316 is used in architectural and marine fittings, for industrial pipes and tanks, automotive trim, and kitchen cutlery.
Carbon Steel 1045
This is a common grade of mild steel, i.e., not stainless. It’s typically less expensive than stainless steels, but considerably stronger and tougher. It’s easy to machine and to weld, and it can be work hardened and heat treated for various hardnesses.
Carbon steel can stand up to repeated hammer blows
1045 steel (in the European standard, C45) is used in many industrial applications for nuts and bolts, gears, shafts, connecting rods, and other mechanical parts requiring a higher degree of toughness and strength than stainless. It’s also used in architecture, but if exposed to the environment it will usually be surface treated to prevent rust.
Titanium
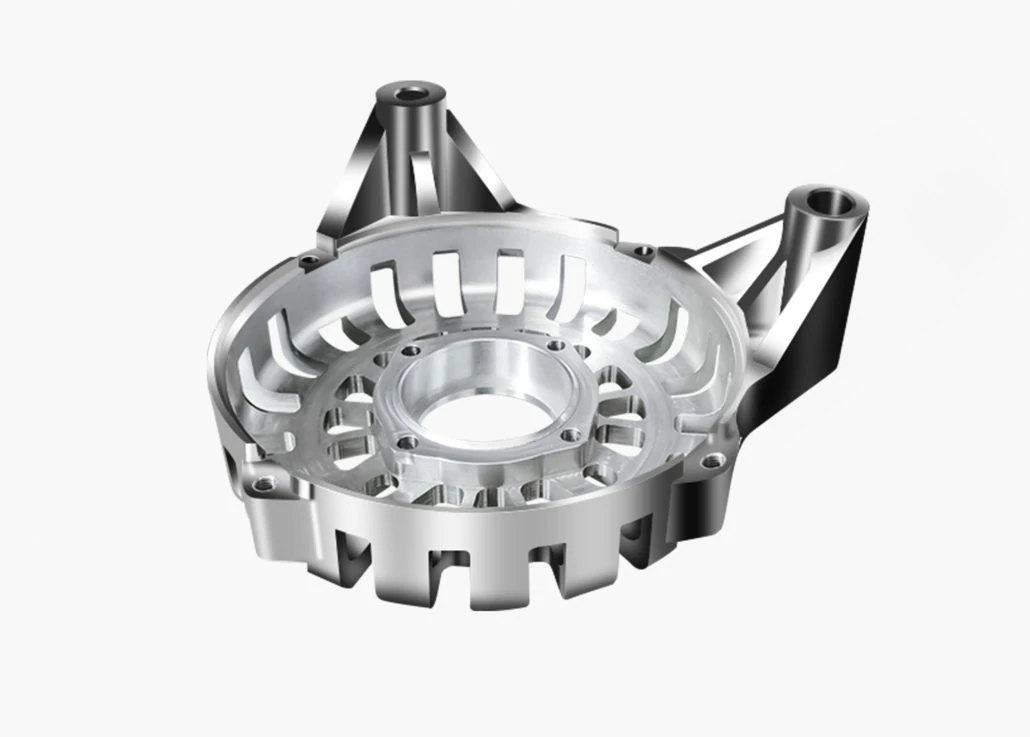
Titanium is well-known for possessing high strength, light weight, toughness, and corrosion resistance. It can be welded, passivated and anodized for increased protection and to improve its appearance. Titanium doesn’t polish especially well, is a poor conductor of electricity but a good conductor of heat. It’s a tough material to machine and only specialty cutters should be used.
Titanium is generally bio-compatible, and has a very high melting point. Although more expensive than other metals in commercial form, it’s a material used in machining that’s actually very abundant in the Earth’s crust but is more difficult to refine.
Titanium works well for powder bed 3D metal printing. It finds applications in the most demanding aerospace, military, bio-medical, and industrial fields, where it stands up well against heat and corrosive acids.
other Metal CNC Machining Materials
Type | Material | Type | Material |
---|---|---|---|
Aluminum | Aluminum AlSi10Mg | Low Carbon Steel | Steel CR 1018 |
Aluminum | Aluminum 5052-H32 | Low Carbon Steel | Low Carbon Steel CR 1008 |
Brass | Brass C260 | Low Carbon Steel | CR Galvanized |
Brass | Brass C360 | Low Carbon Steel | CR Galvannealed |
Cobalt Chrome | Cobalt Chrome | Stainless Steel | Stainless Steel 17-4 PH |
Copper | Copper C101 | Steel Alloy | Steel Alloy 4140 |
Copper | Copper C110 | ||
Copper | Copper CuNi2SiCr | ||
Inconel | Inconel 718 |
2. Plastics
CNC machining can cut plastics like ABS, acrylic, nylon, polycarbonate, and PVC. These materials are commonly used in a variety of products, including toys, electronic components, and medical devices. CNC machining can create intricate designs and shapes that are difficult to achieve with traditional machining methods.
ABS
ABS is an excellent choice for CNC machining. ABS is a tough, impact-resistant plastic that’s also resistant to chemicals and electrical current.
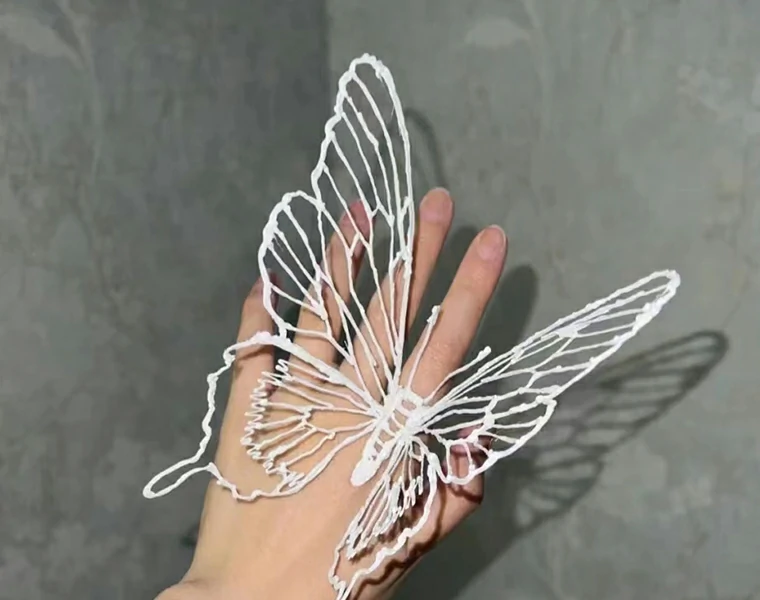
ABS is easy to color so it produces good cosmetic results. Because of its versatility and strength, it’s the most common plastic that we use for rapid prototyping. You’ll find it in automotive components, power tools, toys and sporting goods, among many other applications. ABS is less expensive than other engineering plastics like PEEK or Ultem but it doesn’t withstand high temperatures for long periods of time.
Nylon

Nylon has many of the same desirable characteristics as ABS. It has greater tensile strength which is why we use it for fabric and rope. Nylon and ABS resins are often mixed together, along with glass fibers, to enhance their desirable properties. Nylon can replace many mechanical parts, and because it has good surface lubrication it’s used for moving gears and sliding components. One drawback to nylon is that it does absorb moisture over time so it’s not suitable for marine applications. And it can be tough on cutting tools during machining.
PMMA Acrylic
PMMA is a rigid, transparent resin used as a substitute for glass or when making other clear optical parts. It resists scratching but is less impact resistant than polycarbonate. One advantage of PMMA is that it doesn’t contain Bisphenol-A, so it can be used for food storage. After machining, acrylic shows a hazy, matte surface. The surface can be treated with vapor polishing, which we do at Star Rapid, to make it optically clear. One thing to be aware of about acrylic is that it’s susceptible to heat deformation, so it should be stress-relieved before machining. PMMA is used for display screens, light pipes, lenses, clear enclosures, food storage, and to replace glass if strength is not an issue.
PEEK
PEEK is a true high-strength and stable engineering plastic. It can be used as a substitute for metal in many applications and it can withstand prolonged exposure to high temperatures. PEEK is used for advanced medical, aerospace, and electronic components. It’s also a great choice for lightweight fixtures because it doesn’t tend to creep, or deform, over time like other resins. PEEK is much more expensive than many other plastics so it tends to be used only when nothing else will do. In many cases, it’s necessary to anneal it during the machining process, or else it will form stress fractures.
UHMWPE
This long name means “ultra high molecular weight polyethylene”. There are in fact several different kinds of PE, with different mechanical and chemical properties. UHMWPE is especially hard and strong, very resistant to chemicals, and has a naturally slippery surface. All of these traits make UHMWPE the standard of care for joint replacements. This material is also used in marine environments, food and chemical processing, and for gear trains and conveyor belts.
other Plastic CNC Machining Materials
Type | Material | Type | Material |
---|---|---|---|
ABS | ABS Flame Retardant | POM (Acetal/Delrin) | Acetal Homopolymer (Delrin 150) |
CPVC | CPVC | POM (Acetal/Delrin) | Acetal 20% GF (Delrin 570) |
HDPE | HDPE | POM (Acetal/Delrin) | Acetal Copolymer |
LDPE | LDPE | POM (Acetal/Delrin) | Acetal Static Dissipative (Tecaform SD) |
PA (Nylon) | Nylon 6 Light Blue | PP | PP (Polypropylene Homopolymer) |
PA (Nylon) | Nylon 6/6 | PP | PP (Polypropylene Copolymer) |
PA (Nylon) | Nylon 6/6 (30% GF)_Natural | PPE/PS | PPE/PS |
PA (Nylon) | Nylon 6 Black | PPE/PS | Noryl 265 |
Polycarbonate (PC) | Polycarbonate – Black | PPSU | PPSU |
Polycarbonate (PC) | Polycarbonate – Clear | PPSU | Radel R 5500 |
Polycarbonate (PC) | Polycarbonate – Translucent | UHMW | UHMW |
PEI | Ultem 1000 | UHMW | Quadrant EPP Tivar 1000 |
PEI | Ultem 2300 (30% GF) |
3. Wood
A CNC router machine can work with a variety of wood. Certain types of wood can be considered composite materials with resins, lignin cellulose and other materials included within its structure. A well-designed router can efficiently cut through all wood and wood derivatives, such as plywood and medium-density fiberboard (MDF).
Manufacturers use this machine to produce MDF and plywood furniture, signs, plywood industrial pieces, molds for thermoforming and other wooden articles. Wood has a low-level hardness, perfect for automated manufacturing processes using a CNC router.
However, the low ductility of this material causes chipping as you work on different wood pieces. This feature allows you to vacuum the excess wooden components in your work area easily.
4. Composites
CNC machining can cut composite materials, such as fiberglass and carbon fiber. These materials are commonly used in the aerospace, automotive, and sporting goods industries. CNC machining can fabricate complex shapes and designs with high precision, making it an ideal manufacturing process for these industries.
5. Ceramics
CNC machining can also cut ceramics, such as alumina and zirconia. These materials are commonly used in the medical and dental industries. CNC machining can create precise and intricate designs that are necessary for manufacturing high-quality dental and medical components.
In conclusion, CNC machining is a versatile manufacturing process that can cut a wide range of materials. The precision and high quality of the cuts make CNC machining an ideal process for manufacturing complex components for various industries. If you’re looking for a reliable CNC machining service, consider working with a reputable company that specializes in precision engineering.
6.Plexiglass and Acrylic
CNC machine can also engrave and cut on plastic materials such as plexiglass and acrylic. Some of its most common applications include:
- The manufacturing of industrial parts.
- The development of parts for LED lighting.
- The creation of advertising materials.
- The manufacturing of signages and souvenirs.
CNC routers have a better depth capacity compared to other tools. It can create engravings more than 25 mm or 1-inch thick. The hardness of plexiglass and other similar material is also not an issue for this tool since it can cut through them quickly and efficiently.
How to choose the right cNC machining material
Prioritizing Your Part’s Requirements
The first step is to determine the priority order of your needs. Start with the necessary conditions and gradually determine the identifiable and optional conditions. This process is likely to reduce your material options to a feasible quantity and help you make wiser material choices. At Long Sheng, we use complex software to evaluate your CAD design and generate a quote, but we are unable to understand your application. Do you know under what conditions your component will function and/or how it intends to fit into the component. This is the key information that needs to be understood when developing components. Therefore, some factors that may appear in your priority list include:
- Environmental: For many, this will be an absolute top-of-the-list requirement. Environmental factors can include heat and cold resistance, flame retardance, or UV and chemical tolerance. Depending on the application, your materials may have to be food grade or medical grade. Consider the full scope of a part’s application. For example, parts for a medical device may have to tolerate the extreme high heat of an autoclave or harsh chemical sterilization between uses.
- Electrical: This can cover a range of application-dependent factors. A part may need to conduct or insulate. It may need to dissipate static. In any of those cases, choosing the right metal or plastic resin will be critical.
- Mechanical: Strength comes in many forms. A part may need to fall anywhere on a continuum from rigid to flexible. It may require tensile strength or compressive strength, or be able to resist impact. It may have to resist wear or provide lubricity in order to function as a bearing. There are materials that meet these requirements, some more effectively than others.
- Cosmetic: In many cases, cosmetics are a secondary consideration; in others they can be essential. The right materials can produce a transparent or translucent part. Some materials—typically plastics—can be supplied in a variety of colors, while metals can be colored using secondary processes. Similarly, an application may dictate (or simply benefit from) a specific surface texture from non-slip to high polish.
- Size: While machining can produce parts in a range of sizes, part size can be limited by the maximum available size of a particular stock material.
- Cost: Cost can be an important factor that will typically fall somewhere after the must-haves and among the nice-to-haves.
Identifying Commonly Used Machining Materials
Over the years, our engineers have identified selected materials that work well for machining processes and that have been popular choices among our customers. For metals, these include aluminum, brass, copper, stainless steel, and steel. Among plastics, designers frequently choose polyether ether ketone (PEEK), ABS, Acetal, nylon, polycarbonate, polyvinyl chloride (PVC), high- and low-density polyethylene, and more.
Some important characteristics of the most popular machining materials include:
ABS vs. Acetal | PEEK vs. Ultem | Aluminum 6061 vs 7075 |
---|---|---|
ABS offers high impact strength, low heat conductivity, and low coefficient of friction. | PEEK offers high abrasion and wear resistance, low moisture absorption, and low coefficient of friction | 6061 offers excellent machinability, low cost, and versatility |
Acetal offers high mechanical strength, good dimensional stability, and low moisture absorption. | Ultem (PEI) offers extreme strength, and stiffness, and chemical resistance, and high dielectric strength | 7075 offers high strength, hardness, low weight, and heat tolerance |
Finishing Options and Process Selection
Beyond material choices, there are related secondary processes to consider as well. If, for example, the material of choice is one of the available aluminum alloys—6061 and 7075—there are a couple of available and relevant surface treatments to consider. Anodizing would be preferable for durability, while chromate plating is a better choice if the priority is cosmetics.
If your design includes threads, you have several options to consider. If the stress and wear on the thread will be minimal, a simple machined-in thread will be sufficient and economical. If stress or wear will be more significant, a replaceable insert—a coil insert or key insert—can extend the life of the part. The key insert will be the choice for the most highly stressed threads.
The final choice to be determined is the actual production process—3-axis machining, 5-axis machining, or turning—which is typically informed by the part design.
General Tips on CNC Machining Certain Materials
The decision of which of the CNC machining materials to use for your part ultimately depends on what you’re looking to create, but here are some general tips to use as a brief CNC materials guide:
- Consider non-metallic materials: Don’t assume metals are your best option. Non-metallic materials have become popular because they are lightweight yet durable — like foam you can mold into various shapes. Non-metals also retain small details during cutting. If your project seems like one that may benefit from the use of non-metals, plenty of options can benefit your final product.
- Know the difference between foams: Remember that rigid foam and carving foam serve different purposes. While both are lightweight, yet durable, rigid foam is best for parts with a focus on structural integrity and stability, while carving foam is often used as insulation and prototypes for molds.
- Consider phenolics: Phenolics are great options, especially when you need to adhere to specific regulations or specifications for military-related projects.
- Learn about different plastics: You can choose from a wide variety of diverse plastics. Acetal is often used for bushing and bearing replacements. Polyvinylidene fluoride polymer, or PVDF, is used in insulation for electrical wiring. You can employ UHMW in medical biomaterial, such as knee, hip and spine replacement devices. These are just a few examples of the endless possibilities offered by plastics.
Conclusion
Choosing the right material for CNC machining can be daunting due to the many options available. Aluminum is an excellent choice for its light weight, strength, and machinability, while stainless steel is ideal for parts that need to be durable and resistant to corrosion. Other materials, such as titanium, brass, and bronze, are also viable options for specific applications. The best material for CNC machining will depend on the requirements of a given project. When selecting a material for CNC machining, consider the properties and performance of the material, as well as its cost.
Choosing the right material is the first step. But using the right CNC machining services is also a critical decision. Long sheng is the best available solution in this regard. As a leading CNC machining service provider, Long sheng can handle any project requirements and offers every possible material you might need.

fAQs
WHAT IS CNC MACHINING?
In CNC machining, pre-programmed software and codes will control how the tools and production equipment are operated. It handles some of the most complex machinery, such as drills, lathes, mills, grinders, and 3D printers.
The tools carry out different dimensional tasks, such as cutting, drilling, and removing material from a workpiece to create a predetermined design. The CNC process is highly precise and accurate, offering consistency that surpasses manual production methods.
What can you cut with a CNC?
Trespa, Plexiglass, Plywood, Vermiculite Sheet, Rubber Sheet, Maple Wood. Birch Ply Wood, High Pressure Laminate (HPL), Xanita Fibre Board, Walnut Wood, Laminated Wood, Redwood. OSB Board, Tufnol Sheet, Polycarbonate, Melamine, HDPE Sheet, Cedar Wood, Galvanised Steel Composite Sheet.
Which CNC machining material has the highest machinability?
Free-machining steel is a material that has the highest machinability. Materials like plastics and composites are easier to cut but can react badly to high temperatures generated during the cutting process.
Which is the most durable material that can be CNC machined?
Maraging steel is the most durable material for CNC machining.