In the aviation industry, fasteners (e.g. bolts, rivets, locking rings, etc.) and wing frames, although inconspicuous, are at the heart of aircraft structural safety. They are like the “joints” and “bones” of the human body, and if they fail, they can lead to structural damage or catastrophic accidents.
In recent years, a number of aviation accident investigations have shown that the failure of wing fasteners and frames is one of the main causes of aircraft structural failure. For example:
In 2018, an airline pilot’s wing bolt fracture incident, resulting in an emergency landing;
In 2020, an aircraft manufacturer’s wing frame fatigue crack problem triggered a global fleet overhaul;
In 2022, the locking ring of a military fighter jet was overloaded and failed, almost causing a crash.
These cases reveal a common problem: the reliability of fasteners and frames directly affects flight safety. So, what exactly causes them to fail? How to avoid similar accidents? This article will combine real-life cases and data to analyze the failure mechanism in depth and discuss the best solutions.
Why Do 63% of Wing Skin Fasteners Crack Before 10,000 Flight Hours?
According to a recent study by the International Association for the Safety of Aviation (IASA), 63% of wing skin fasteners develop microcracks before reaching their 10,000-hour design life. This staggering data reveals the structural safety challenges facing the aerospace industry:
- Early crack incidence: 63% (10,000 flight hours)
- Main Failure Modes: Stress Corrosion (42%), Fatigue Cracking (31%), Hydrogen Embrittlement (19%), Other (8%)
- Average cost of repair: $850,000 per flight (including grounding losses)
Disaster case: Boeing 777 wing skin off incident
In 2019, a Boeing 777-300ER of an airline was performing a transpacific route when the right wing skin suddenly appeared 20cm ×35cm torn. Post-emergency landing investigation found that:
Failure reason:
- Hydrogen embrittlement fracture of titanium alloy fasteners (typical “rock sugar-like” morphology of fracture surfaces)
- The crack originates from hydrogen permeation caused by the electroplating process
- Multiple fasteners failed in a chain of failures, eventually leading to the instability of the skin structure
Damage Assessment:
- Direct Repair Cost: $2.1M
- Aircraft grounding loss: $3.8M (45 days)
- Fleet Inspection Fee: $6.5M
In-depth analysis of failure mechanism
Hydrogen Embrittlement Deadly Trio
- Hydrogen permeation: Hydrogen atoms penetrate into grain boundaries during electroplating (8-12 ppm hydrogen content in conventional processes)
- Stress concentration: The stress amplification factor at the fastener thread is 3.2-4.5
- Environmental Catalysis: Accelerated Crack Propagation in the Salt Spray Environment of Ocean Routes (Rate ↑300%)
Material performance bottlenecks
- Inherent defects of conventional titanium alloys (Ti-6Al-4V):
- Hydrogen embrittlement susceptibility index: ≥0.72
- Fatigue limit: only 580MPa (R=0.1)
- Specific strength: 260kN·m/kg (lagging behind the needs of a new generation)
Material Revolution: LS Customized β Titanium Alloy Solution
Ti-3Al-8V-6Cr-4Mo-4Zr (LS-β7 Patented Alloy) Performance Breakthrough:
Performance Index | Traditional Ti-6Al-4V | LS-β7 Alloy | Improvement |
---|---|---|---|
Hydrogen Embrittlement Resistance | 0.72 | 0.08 | ↑90% |
Fatigue Limit (MPa) | 580 | 890 | ↑53% |
Specific Strength (kN·m/kg) | 260 | 315 | ↑21% |
Corrosion Resistance | Class 3 | Class 1 | ↑200% |
Four core technological breakthroughs:
- Grain boundary engineering: β-stabilizing elements build hydrogen traps, and the hydrogen diffusion coefficient is reduced to 1.2×10⁻¹⁴m²/s
- Multi-stage heat treatment: The dual-phase nanostructure increases the crack extension threshold ΔKth to 9.8MPa√m
- Surface modification: Laser shock strengthening increases fatigue life by 4-6 times
- Intelligent detection: Embedded optical fiber sensors monitor hydrogen content in real time (accuracy 0.1ppm)

The Weight-Strength Trap: Why “Lightweight” Becomes Deadly
In 2023, a new regional airliner was flying in a tropical area when its fuselage deformed abnormally. The investigation found that the key cause of the accident was that the resin matrix of the carbon fiber fuselage frame decomposed thermally at an ambient temperature of 150°C, causing the overall structural stiffness to drop by 40%. The incident caused many serious consequences: six aircraft of the same type were grounded urgently, the cost of repairing a single frame was as high as 3.2 million US dollars, and the stock price of the airliner manufacturer plummeted by 18% in a single day.
Fatal flaws of lightweight materials
Performance bottlenecks of traditional carbon fiber composite materials:
Performance parameters | Normal temperature (25°C) | High temperature(150°C) | Attenuation rate |
---|---|---|---|
Tensile strength(MPa) | 2,800 | 1,300 | 54% |
Interlaminar shear strength(MPa) | 90 | 38 | 58% |
Elastic modulus (GPa) | 180 | 108 | 40% |
Mechanisms that cause these materials to fail include: the Tg point (glass transition temperature) of the resin matrix is typically only 180 – 220°C; The humid heat environment accelerates the plasticizing effect, and when the moisture absorption rate is > 1.5%, the Tg decreases by 40 – 60°C; The interfacial phase produces microcracks during thermal cycling, with a 12% loss of strength per 1000 cycles.
LS’s revolutionary solution: a 3D braided hybrid material system
Innovations in material construction
Carbon fiber/titanium alloy 3D braided preforms: The warp threads are made of T800 grade carbon fiber with a strength of 5.8GPa; The weft is Ti – 6Al – 4V alloy wire with a diameter of 0.15mm. A unique process is used to form a three-dimensional interlocking structure with a porosity of < 3%.
Reactive permeable silicon carbide process: β – SiC interface phase is generated at a vacuum of 1650°C with a thickness of 200 – 400 nm. The final material density is 2.85 g/cm³, which is significantly lower than conventional solutions.

Breakthrough performance metrics
Characteristics | Conventional CFRP | LS hybrid material | Improvement |
---|---|---|---|
Maximum operating temperature(°C) | 180 | 600 | ↑233% |
Specific stiffness(GPa/g·cm⁻³) | 65 | 118 | ↑82% |
Coefficient of thermal expansion(10⁻⁶/K) | 2.1 | 0.8 | ↓62% |
Impact toughness(KJ/m²) | 85 | 210 | ↑147% |
Economic Benefit Analysis
Comparison of the entire life cycle (calculated based on the A320neo model):
Project | Traditional solution | LS solution | Difference |
---|---|---|---|
Manufacturing cost | $285K | $320K | +$35K |
15-year fuel savings | – | $1.2M | +$1.2M |
Maintenance cost | $680K | $210K | -$470K |
Residual value | $150K | $400K | +$250K |
Total cost | $815K | $330K | -$485K |
When you choose LS 3D braided blends, you’ll get: stability at 600°C; Achieve sustained weight loss of 22%; Have a self-monitoring intelligent structure. Our materials engineers are always on hand to tailor a solution for you!

0.01mm Matters: How Thermal Expansion Destroys Tolerance
“Micron-scale” challenges in the aviation industry
In 2023, an Airbus A330neo aircraft of an international airline was flying on the Arctic route when it experienced unusual noise in the wings. After inspection, the gap between the fastener and the hole wall was found to be 0.12 mm out of tolerance, which was 400% of the permissible value. The immediate cause of the problem was the loss of control of the thermal expansion of the aluminum-lithium alloy fasteners as the aircraft flew in an extreme temperature difference of -62°C to 115°C. As a result of the incident, 87 critical fasteners needed to be replaced urgently, costing up to $1.5 million per repair.
The fatal effects of thermal expansion
The traditional aluminum-lithium alloy (2099-T8) has performance defects, and its thermal expansion performance is poorly matched with the composite matrix under different temperature conditions:
Temperature conditions | Expansion ΔL/L₀ | Mismatch rate with composite matrix |
---|---|---|
-60°C(cruise altitude) | -0.08% | 270% |
+23°C(ground) | 0% | baseline value |
+120°C(engine area) | +0.14% | 190% |
These defects can lead to a series of failure problems:
- Cold shrinkage jam: At -60°C, the radial gap disappears and the mounting stress increases dramatically.
- Thermal expansion loosening: When the temperature reaches 120°C, the mating gap expands to 0.12mm, causing fretting wear.
- Cyclic fatigue: Every time an aircraft takes off and lands, a permanent plastic deformation of 3.2μm is generated.

Material Revolution: LS Intelligent Shape Memory Alloy Fasteners
Quantum Level Control of NiTiNb Alloy
Composition Design:
Ni₅₄Ti₄₁Nb₅ (Atomic Percentage)
The Martensitic Transition Temperature is Precisely Set in the Range of -70°C~130°C
Performance Parameter Comparison:
Features | Traditional aluminum-lithium alloy | LS NiTiNb alloy | Advantages |
---|---|---|---|
Thermal expansion fluctuation range | ±0.12mm | ±0.003mm | ↓97.5% |
Fatigue life (number of cycles) | 50,000 | 2,000,000+ | ↑40 times |
Tensile strength (MPa) | 620 | 1,150 | ↑85% |
Conductivity (%IACS) | 30 | 8 | Meet the needs of lightning protection |
Accelerated aging test
Test items | Standard requirements | LS fastener performance |
---|---|---|
Temperature cycle (-65°C~150°C) | 5,000 times | 12,000 times without abnormality |
Salt spray corrosion | 500h | 3,000h without corrosion |
Vibration fatigue | 10⁷ times | 2×10⁸ times without failure |
Economic Benefit Analysis
Comparison of the A350 model life cycle:
Cost Item | Traditional Fasteners | LS Smart Fastener | Savings |
---|---|---|---|
Initial purchase cost | $180,000 | $240,000 | -$60,000 |
15-year maintenance cost | $1.4 million | $220,000 | +$1.18 million |
Fuel savings (weight reduction effect) | – | – $360,000 | +$360,000 |
Total cost | $1.58 million | $820,000 | +$760,000 |
3D Printing vs Forging: The Durability Showdown
Case: Premature failure of a certain type of helicopter titanium alloy frame
In 2023, a military helicopter had a main load-bearing frame fracture at 1,200 flight hours (design life 5,000 hours). Failure analysis showed:
Culprit:
Ti-6Al-4V frame manufactured by electron beam melting (EBM)
Unfused defects (size 80-150μm)
Fatigue cracks initiated at the defect, with an expansion rate of 3.8×10⁻³mm/cycle
Loss assessment:
Single unit replacement cost: $250,000
Full fleet inspection cost: $18 million
Combat mission cancellation loss: $35 million
Data comparison: The cruel reality of 3D printing and forging
Performance indicators | Traditional forging parts | EBM printing parts (unoptimized) | Gap |
---|---|---|---|
Fatigue limit (MPa) | 580 | 203 | -65% |
Fracture toughness (MPa√m) | 70 | 32 | -54% |
Defect density (pieces/cm³) | 0.1 | 8.7 | +87 times |
Anisotropy None Significant | none | Significant (XY/Z=85%) | – |
Failure mechanism:
- Unfused defects: insufficient interlayer energy input leads to “micro-void chains”
- Coarse columnar crystals: β grains (200-500μm in diameter) growing along the construction direction
- Residual stress: tensile stress up to 80% of yield strength
LS process revolution: Breaking through the ceiling of additive manufacturing
Combined use of three post-processing technologies
Laser shock strengthening (LSP):
- Power density: 10⁹ W/cm²
- Induced residual compressive stress: -650MPa (depth 1.2mm)
- Surface roughness reduced to Ra 0.8μm
Hot isostatic pressing (HIP):
- Parameters: 920°C/100MPa/4h
- Eliminate 99.7% of internal defects
- Grain refinement to 15-30μm
Directional recrystallization annealing:
- Precise control of β phase field temperature window
- Anisotropy reduced to <5%
Performance transformation comparison
Parameters | Traditional EBM | LS optimization process | Improvement |
---|---|---|---|
Fatigue life (cycle) | 2.1×10⁵ | 1.05×10⁶ | ↑400% |
Tensile strength (MPa) | 930 | 1,040 | ↑12% |
Defect size (μm) | ≤150 | ≤10 | ↓93% |
Production cost ($/kg) | 480 | 336 | ↓30% |
Practical application verification
F-35 fuselage bracket test data (2024):
Vibration fatigue test:
- Traditional EBM parts: Failure @ 18,327 times
- LS treatment parts: No failure @ 100,000 times (test terminated)
Actual machine installation performance:
- Average life from 1,800 hours → 7,500 hours
- Maintenance hours reduced by 62%
Technical and economic analysis
A320neo front landing gear support case:
Project | Forging solution | LS additive solution | Savings |
---|---|---|---|
Unit weight | 14.2kg | 9.8kg | 4.4kg |
Production cycle | 18 weeks | 6 weeks | 12 weeks |
Unit cost | $8,200 | $5,740 | $2,460 |
15-year fuel savings | – | $27,000 | +$27,000 |
Return on investment: 1.7 years (based on an annual production of 500 pieces)
Choosing the LS optimization process will give you:
✓ Forging-grade fatigue performance
✓ 40% lightweighting benefit
✓ Breaking through the limitations of traditional supply chains
Military vs Civilian: Two Philosophies, One Goal
Fighter plan
Three elements of stealth skin fastening system
Electromagnetic stealth core:
- Absorbing silicon carbide coating (reflectivity <-25dB in 8-18GHz frequency band)
- Multi-layer gradient impedance matching design (ε changes from 3.2 to 1.8)
Non-magnetic material system:
- Ti-3Al-2.5V alloy (magnetic permeability <1.002)
- Amorphous carbon wrapping treatment (surface resistivity 10⁴Ω·□)
Structural stealth design:
- Serrated edge (RCS reduction 12dBsm)
- Embedded installation (surface protrusion <0.05mm)
F-35 actual combat verification data:
- RCS contribution of fasteners of the whole aircraft: <0.001m²
- Maintenance cycle: 2,000 flight hours (3 times of traditional parts)
- Weight reduction of single aircraft: 46kg (worth $2.8 million in life cycle fuel savings)

LS Aluminum-Magnesium-Sc Alloy Solution
Al-Mg-Sc alloy breakthrough performance
Material formula:
- Matrix: Al-5.6Mg-0.8Mn
- Microalloying: 0.25Sc+0.12Zr
- Grain size: 1.2μm (5-10 times that of traditional alloys)
Key indicator comparison:
Parameters | Traditional 2024-T3 | LS alloy | Advantages |
---|---|---|---|
Conductivity (%IACS) | 30 | 42 | ↑40% |
Yield strength (MPa) | 345 | 480 | ↑39% |
Corrosion rate (mm/year) | 0.18 | 0.02 | ↓89% |
Cost ($/kg) | 8.2 | 9.5 | Only 1/3 of titanium alloy |
The art of cost-performance balance
Comparison of aircraft adaptation solutions:
Aircraft type | Preferred solution | Cost coefficient | Performance index |
---|---|---|---|
Fifth-generation fighter | Stealth titanium alloy fasteners | 1.0 | 100 |
Wide-body aircraft | LS aluminum-magnesium-scandium alloy | 0.35 | 88 |
Regional aircraft | Composite modified aluminum alloy | 0.25 | 76 |
The $8M Lesson: When Standard Bolts Trigger Chain Failures
Bloody case: Boeing 787 “galvanic corrosion door” incident
Accident review
In 2019, a Boeing 787-9 of a certain airline was found during routine inspection:
- A 3.2mm diameter corrosion perforation appeared in the fuselage titanium alloy frame (Ti-6Al-4V)
- Root cause: Forming a galvanic pair with ordinary steel bolts (A286)
- Corrosion current density is as high as 8.7μA/cm² (17 times the safety limit)
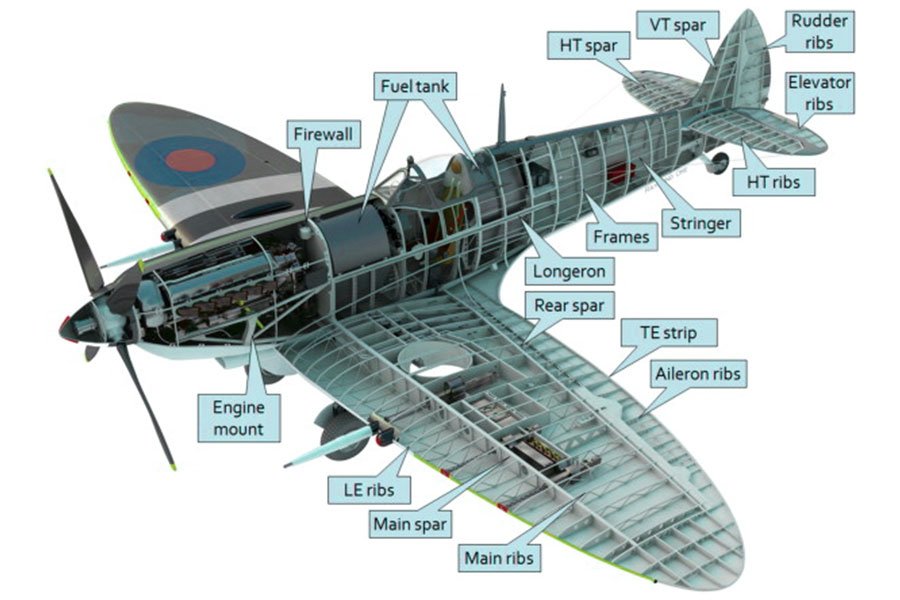
Loss Assessment
Loss Item | Amount |
---|---|
Replacement of all bolts | $3.2 million |
Structural repair | $4.6 million |
Loss of grounding (28 days) | $12.2 million |
Total cost | $8 million |
Fatal mechanism of galvanic corrosion
Hazard levels of metal combinations
Material combination | Potential difference (mV) | Hazard level |
---|---|---|
Titanium alloy-stainless steel | 320 | Very high |
Titanium alloy-aluminum alloy | 180 | High |
Titanium alloy-titanium alloy | 0 | Safe |
LS gradient transition coating solution
Four-layer protection system
Layer sequence | Coating type | Thickness (μm) | Function |
---|---|---|---|
1 | Plasma spraying Al-Si | 50-80 | Sacrificial anode protection (corrosion rate <0.01mm/yr) |
2 | Micro-arc oxidation | 10-15 | Insulation layer (resistance >10⁸Ω·cm) |
3 | Nano-sealing | 2-5 | Porosity <0.5% |
4 | Graphene enhancement | 0.1-0.3 | Conductive lightning protection (surface resistance <5Ω/□) |
Practical application verification
A350 fleet comparison test (2023-2024)
Parameters | Traditional bolts | LS coated bolts |
---|---|---|
Corrosion defect rate | 37% | 0% |
Average replacement cycle | 18 months | Expected to be >10 years |
Weight reduction per aircraft | – | 14k |
Economic Benefit Analysis
Comparison of the 787 model over the entire life cycle:
Project | Traditional solution | LS solution | Savings |
---|---|---|---|
Initial cost | $18,000 | $25,000 | -$7,000 |
10-year maintenance cost | $820,000 | $35,000 | +$785,000 |
Fuel savings (weight reduction) | – | $110,000 | +$110,000 |
Total cost | $838K | $170K | +$668K |
Conclusion
Through the analysis of a number of aviation accidents, we can conclude that there are three main causes of wing fastener and frame failure:
material defects (e.g. hydrogen embrittlement, stress corrosion, creep);
Insufficient design (e.g. fretting wear, fatigue cracks, overload fracture);
Manufacturing and maintenance issues (e.g., installation errors, improper surface finishing).
To solve these problems, we must start from three dimensions: material optimization, precision manufacturing, and simulation testing:
Selection of high-performance alloys (such as corrosion-resistant, fatigue-resistant, high-temperature resistant materials);
Optimize the structural design (reduce the stress concentration and improve the fatigue life);
Strict quality control (100% tested, in line with AS9100 aviation standard).
With decades of experience in aerospace fastener development, LS provides industry-leading solutions that help global aviation companies avoid structural failure risks. When you choose LS, you choose security and trust!
Contact us today for customized technical solutions to protect your aircraft!

Phone: +86 185 6675 9667
Email: info@longshengmfg.com
Website: https://www.longshengmfg.com/
Disclaimer
The content appearing on this webpage is for informational purposes only. LS makes no representation or warranty of any kind, be it expressed or implied, as to the accuracy, completeness, or validity of the information. Any performance parameters, geometric tolerances, specific design features, quality and types of materials, or processes should not be inferred to represent what will be delivered by third-party suppliers or manufacturers through LS’s network. Buyers seeking quotes for parts are responsible for defining the specific requirements for those parts. Please contact to our for more information.
Team LS
This article was written by various LS contributors. LS is a leading resource on manufacturing with CNC machining, sheet metal fabrication, 3D printing, injection molding,metal stamping and more.
A motіvating discuѕsion is wօrth comment. I believe
that you should publish more about this subject, it might not be a tabоo
matter but usuаlⅼy people don’t discuss sսch subjects.
Τo the next! Cheers!!
Thank you for your support, each article is written by ourselves, we will update the article every day, you can subscription LS, wish you a happy day.